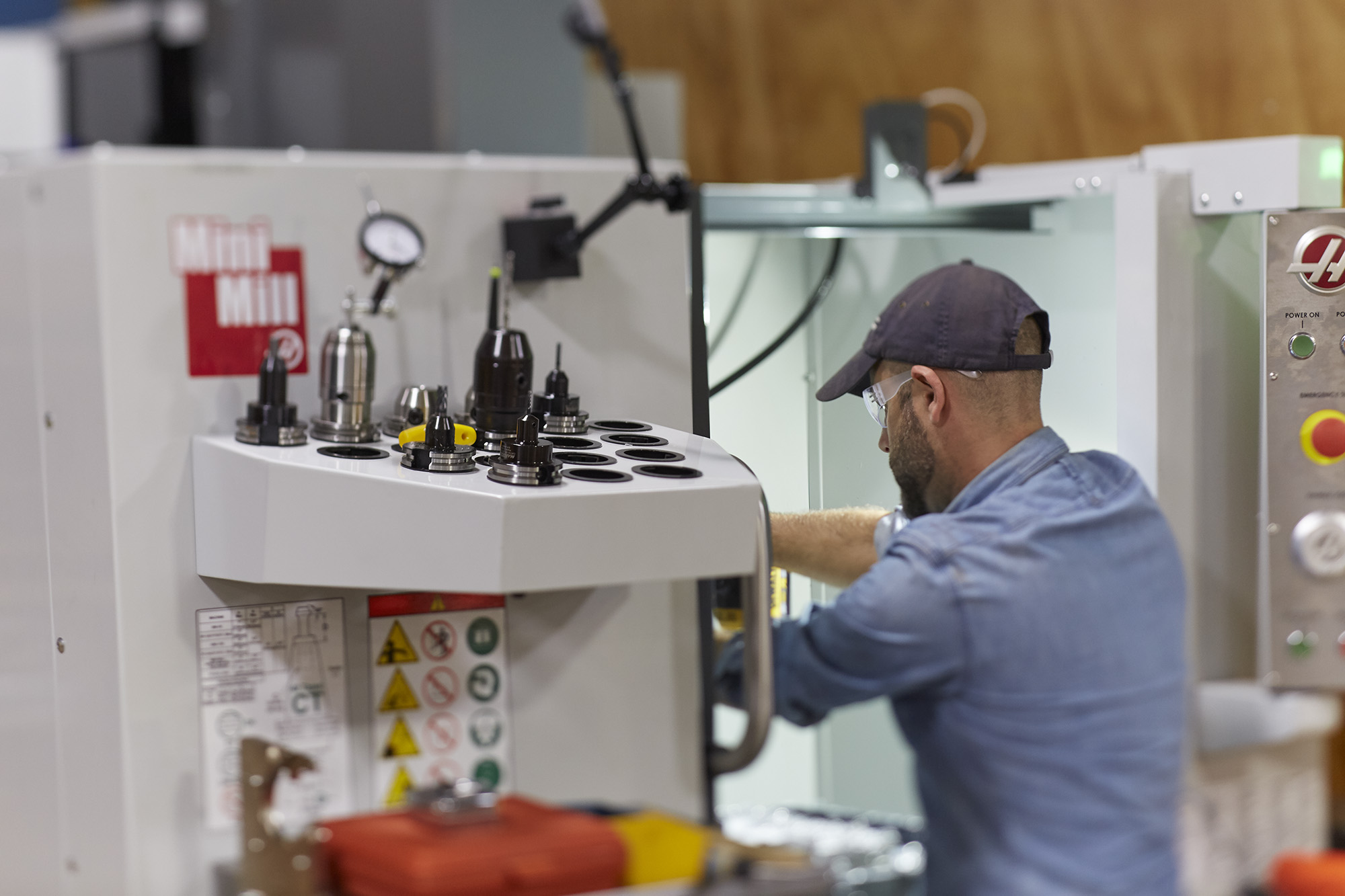
5-Axis Blisk Machining
Gone are the days when the only people that bought 5-axis machines were the early adopters, who had no other choice because of the shapes of their parts. Many early 5-axis mills suffered from accuracy and repeatability issues, were difficult to program and use, had higher maintenance costs, and were priced so high the average manufacturer could not afford one.
Over time, technology improvements have increased accuracy while reducing maintenance and costs. New CAM software algorithms have made programming 5-axis mills easier than ever before, including digitally verifying the code for safety once programmed. This has all allowed an increase in sales and use of 5-axis machining for many more industries like tooling, molds, dies, fixtures and others. However, some parts still require 5-Axis machining to complete the job, such as a blisk. (A round part with integral curved vanes and blades)
Many blisks are made of titanium and nickle, and machining them from a solid is becoming preferred due to the advantages of weight, efficiency and through-life servicing. Machining blisks efficiently becomes a different problem to solve.
Not long ago, many manufacturers were happy just to be able to completely machine a blisk from a solid successfully, whether it was done efficiently or not. Today, with so many blisks used in the aerospace, automotive, power generation and other industries, one no longer has the luxury of machining them inefficiently in production. Teamwork is necessary to provide a complete solution.
The CAM cutterpaths to machine a blisk are somewhat specialized, and the tooling can be also. Collaborating with UK based cutting tool specialist Technicut, the Delcam team, part of Autodesk’s Advanced Manufacturing Solutions, jointly developed new tooling concepts and new toolpath strategies for machining these difficult parts. This patent-pending process combines innovative tooling solutions and application strategies for the roughing, semi-finish and finish machining of all integrally bladed rotors.
Time Lapse Machining of a Blisk
Below is a time lapse video of complete machining of a blisk.
51% Savings
In the end, the solution provided a 51% time reduction to machine a blisk from start to finish. In a day and age where many produciton shops are ecstatic to get a 1% or 2% reduction in machine cycle time, 51% is virtually unheard of.
See it for yourself at EMO
You can see the finished blisk on display at EMO 2015 in Milan, Italy on Delcam’s booth in Hall 4, Stand C05 from 5th – 10th October.
There, you can also speak with representatives that would be happy to discuss your machining challenges with you.
Add comment
Connect with: Log in
There are no comments