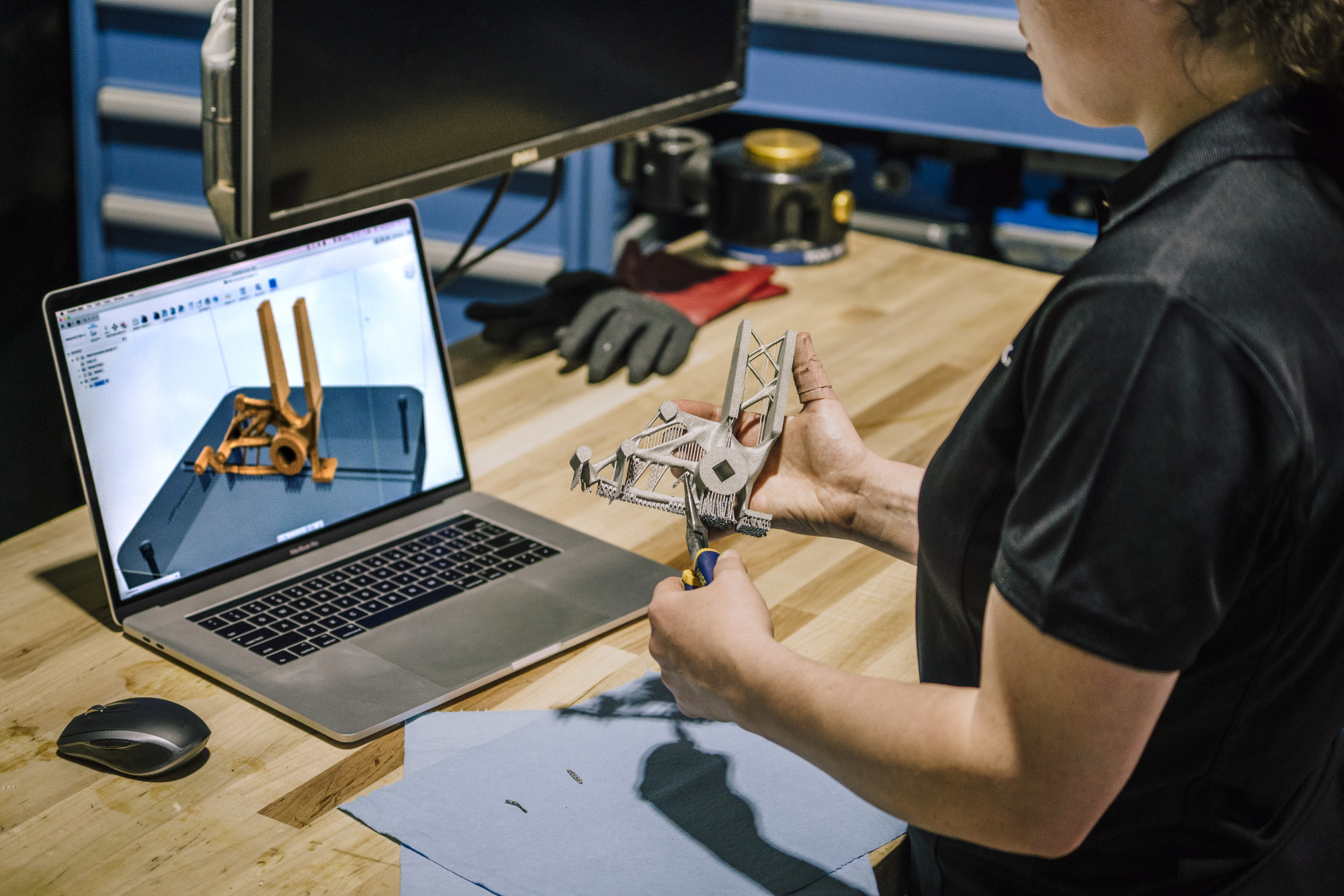
GQsystems defines lean manufacturing as a system of techniques and activities designed to eliminate “all non-value-adding activities and waste.” Although designed is not a word GQsystems uses in their definition, it has been added here because any lean-manufacturing operation has its foundation in factory design.
If lean manufacturing is your goal, when designing the layout of your plant, it’s important to keep the following in mind:
- Waste reduction
- Workflow optimization
- Customer-focused design
Waste reduction
Waste in a manufacturing plant can mean anything from lack of attention to detail to worn and neglected equipment. But one of the main focuses when designing a lean factory space should be on reducing actual material waste and reusing whatever waste you can’t completely eliminate.
According toAssembly magazine, lean manufacturing plants use space in a way that makes waste highly visible. Even when minimized, waste will build up, and when it’s always in plain view, employees are motivated to reuse the material.
Once you start your factory design with reducing material waste in mind, turn your attention to reducing other types of waste. GQsystems notes that wasted resources affect costs, quality and delivery of products. Issues such as inventory buildup, inefficient processes and wasted time can all be resolved by optimizing your space.
(Image:www.pmcorp.com)
Consider the time employees spend walking the factory floor, for example. Ask yourself how you can you reduce that time by your choice of asset placement. You’ll find that the amount of time you save by decreasing walking distance directly correlates with reduction of wasted materials.Total Excellence Manufacturing (TXM) suggests designing U-shaped cells to decrease walking distances. There are many options available when it comes to reducing the time involved in work processes.
Work-flow optimization
(image:pds.docsol.sfu.ca)
Your factory layout not only affects how much waste you produce, it affects productivity. The right layout will increase productivity by making communication among employees quicker, easier and more efficient. This can benefit your business in a number of ways, such as:
- Improving morale
- Encouraging teamwork
- Streamlining processes
Think about how your parts and products travel from station to station as they’re being made. Ask yourself how you can cut what’s unnecessary to improve efficiency.
Customer-focused design
Staying focused on reducing waste and improving workflow is a good place to start when designing your factory, but believe it or not, customer needs and wants also play an important role. TXM notes that manufacturers should determine their rates of production by customer needs. Be sure to keep this in mind as you plan your design.
Assembly provides a good list of things to consider when it comes to customer-focused factory design, including:
- Just-in-time delivery
- Parts sequencing
- Assembly and kitting
Autodesk Factory Design Suite
Because there’s so much to consider, manufacturers don’t always think about everything involved in factory design. WithAutodesk Factory Design Suite, you can make sure that all necessary considerations are covered. Subscribing to Factory Design Suite will give you the power to simulate many design variations before you ever move a piece of equipment, and you’ll soon have the lean-manufacturing operation you want.