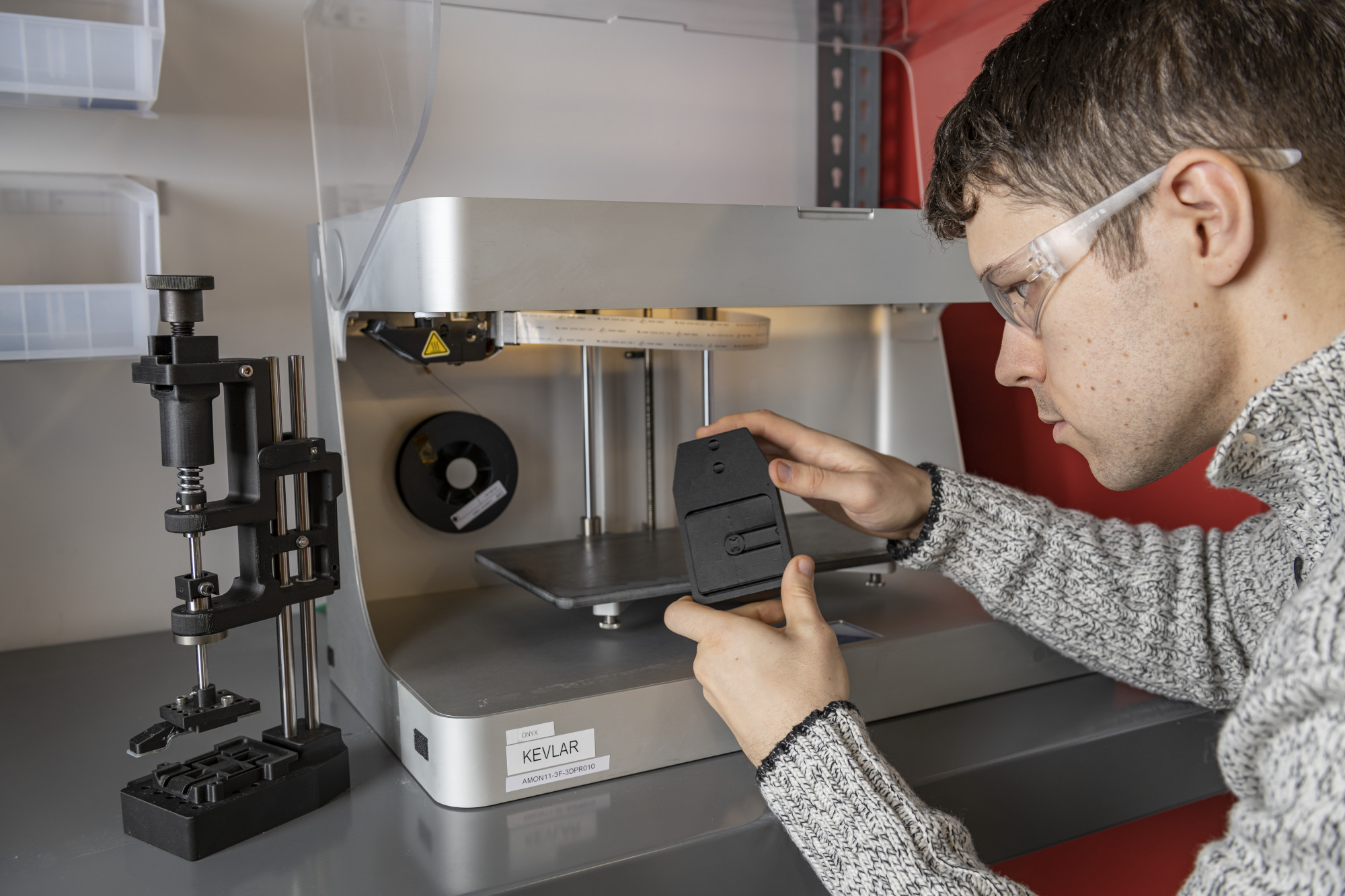
In 2000, archaeologists discovered a big toe made of wood and leather attached to the foot of an Egyptian mummy. According to LiveScience, after testing replicas of the toe on two volunteers, it was determined that the chances that the ancient prosthesis was functional were pretty good. From this finding, we can conclude that people have been making prosthetics for around 3,000 years, if not longer.
Prosthetics have certainly come a long way since then, especially in the last few decades with the arrival of technologies like 3D printing and generative design. According toABC news in Australia, this year marks the first successful operation for a 3D-printed titanium sternum and rib cage implant.
3D printing body parts
The rapid advancements in 3D-printing technology allow engineers to experiment with a number of materials in addition to titanium.ABC notes that in the future, engineers will likely be able to replicate bone and tissue materials and 3D print parts that contain a patient’s stem cells.
(image:news.discovery.com)
Is 3D printing the fountain of youth? Will people of the future be part cyborg and part human and live hundreds of years? The future of medical 3D printing does hold some exciting possibilities, but the ability to save lives with 3D-printed living tissue will likely happen sooner than we think. According to ABC, Queensland University of Technology has already been successfully testing 3D-printed tissues on animals, and human testing is the next step.
3D printing can be even more powerful when combined with milling.ConforMIS, a knee-replacement company, currently uses both technologies to custom design knee implants that function better than “off-the-shelf” implants. With a CT scan, ConforMIS uses proprietary algorithms to map 3D models unique to each patient.
Algorithmic design is important to rapid advancement in prosthetics, especially when it comes to generative design, a software solution that problem solves without the help of humans.
Endless design possibilities
Wired magazine notes that one of the benefits of generative design software is its ability to create without preconceptions. When it comes to generative design, rather than create, designers input objectives, goals or problems that need to be solved. Then the software iterates thousands of possibilities.
Wired describes a motorcycle part, known as a swingarm, designed byAutodesk’s Dreamcatcher software, a generative design tool. The intelligent software opted for bone-like material for the swingarm, rather than metal, because the bone-like material worked better with the weight and strength requirements.
Without generative design software, it’s easy to imagine a designer deciding to run iterations of prototypes that use bone-like structures for actual bone replacement. But as we see with the swingarm prototype, generative design software is not limited by human preconceptions. Metal is apparently not the first material that generative design software chooses for a motorcycle part, and this software may never even consider bone-like material to replace bones if there are better options.
Wired also notes that medical implants are likely to improve dramatically due to generative design solutions. Autodesk is already working on software that can design parts on a micro-scale, and the ability to design and make materials at that level will certainly allow us to make prosthetics that are more organic and work just like real body parts.
(image:blog.luxexcel.com)
Micro-scale design is still in the works, but engineers are already using the combined power of 3D printing, milling and generative design. With solutions likeAutodesk’s Within Medical software, engineers can make more organically structured, customized implants that perform well in the human body. It’s the combined power of these three technologies that will take us to that fountain-of-youth future when the difference between cyborg and human is negligible.