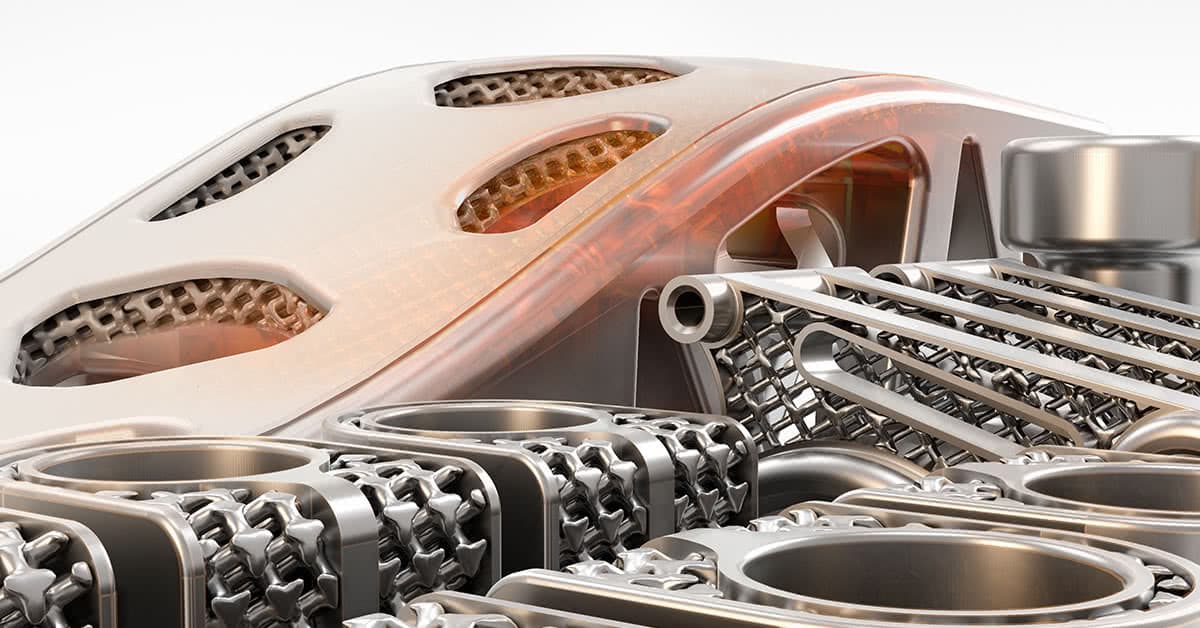
Can you make this?
It’s one thing to design something, but can it actually be made? That’s what design for manufacturing is all about.
First, there’s the question of whether it can be made at all. George Lucas may be able to design a “Death Star” but that doesn’t mean it can be manufactured with today’s technology. As silly as it sounds, if we had the material resources and power generation, we could theoretically build something that large, and nearly as destructive, it just might take a long time.
Then, there are the things that are designed, and can be manufactured, but is the process practical? The manufacturing process, for the designed part, may make the part totally impractical, versus altering the design for a different manufacturing process. For example, you may be able to buy all the pieces you need, and have Amazon ship them to your house, to build an automobile. However, that will be terribly expensive compared to the traditional assembly line and picking up a finished car at a dealer.
Also one should design for the material. You may design a plastic part with a really sharp corner, however it is more difficult to mold plastic into a sharp corner than not. This is why small fillets are often found on plastic part edges.
Can you mill this?
Design for manufacture comes into play in the CNC machining world as well. When designing a part, one should keep in mind the machining processes that will be necessary to make the part. Where if the part is overly complex, machining it may become difficult, expensive or impossible. Some things one needs to take into consideration when designing a part to be CNC machined:
- Will it fit on my mill?
- Will it need really long tools?
- Will it need really small diameter tools?
- Will the tooling, spindle or other portions of the machine interfere with the part?
- Can you reach all of the areas with a tool?
For example take the part below. Around the time of the 2016 Olympics, we wanted to get in on the hype with some medals of our own. The plan was to CNC mill the medals with Autodesk HSM CAM software. Since the Olympic committee frowns upon companies using their images, trademarks and copyrights without permission, a person in another department volunteered to design a medal of our own.
Without a doubt, this is a fantastic looking medal, it is original and borrows nothing from the Olympic design. Downside is, it’s not very millable. There are a lot of shallow areas, with 3D contoured shapes and sharp corners. Very small areas around the text. Round tools don’t do such a great job of making a sharp corner, at least not along the tool axis.
To accurately mill this medal, one would need to go to smaller and smaller cutter diameters to pick up more of the detail in the tiny edges and features. Every time you go to a smaller cutter, you incrementally increase the costs. One not only has the cost of the smaller cutter, but also the additional mill time required to run the smaller cutter. Since the cutter is smaller, and breaks easier, you have to run slower, adding to the costs.
Below are the medals from a Tormach 440 CNC milling machine. We went down to a 1/16″ ball nose on the medal and used a 1/32″ to mill the small slot. If we were to continue with smaller tools for the main part of the medal, we would definitely get more detail into the shape, but it would add double possibly even triple the milling time. The question is whether the customer wants to pay double or triple for the work?
How small can you go?
If you absolutely had to have the sharp corners in the medal, one may resort to a different manufacturing process. For example they may try 3D printing, or possibly some form of casting or powdered metal fabrication process. The tooling would be made from a combination of milling, EDM (electrical discharge machining), and other operations.
Dies for creating coins, like at a mint, are often CNC milled in this day and age. To get the detail of a coin, they are milled with smaller and smaller cutters, often going as small as 0.006″ in diameter, the width of about 6 human hairs. The cumulative milling operation can take two days of milling time, for something the size of a quarter. Not only do you need special tools to do this, but you need mills with very high accuracy. There is no point milling for that kind of detail if the mill its self is incapable of being that accurate.
So when it comes to designing, remember to consider how something is going to be made, when working on the design.
See Design and Manufacturing together:
Autodesk University is a venue where one portion showcases design and manufacturing together. It is held from Nov 15-17 in Las Vegas. Sign up before October 10th to get reduced pricing.
Add comment
Connect with: Log in
There are no comments