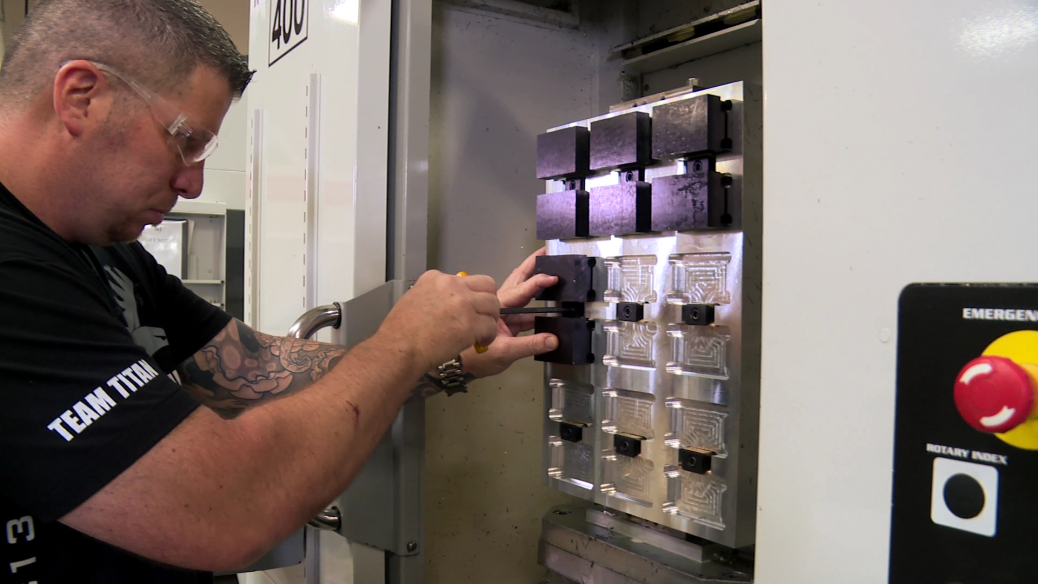
Shaping Your Future Part 2: Efficient Fixturing
How creative fixturing helps shops make the leap to next-level productivity
Speed makes your shop more profitable. But once you are running faster toolpaths and maximizing inches per minute on your CNC machines, what comes next? According to Titan Gilroy, it’s keeping the doors closed and letting automation do the work for you. A good fixture can help with that.
“Let’s say you’ve done everything you need to do to get part time down,” Titan says. “The program that used to take you 20 minutes now only takes four. That’s great. But you don’t want to open the door every four minutes and exchange one part. Even if you have four parts on vices, you don’t want to open the doors every 16 minutes. You want the green light to stay green.”
The next step toward elite HSM is combining the art of manufacturing with the science of fixturing. While other shops might be running two, four or eight parts at a time, Titan’s shop regularly runs 30 to 50 parts simultaneously.
“The point is to fixture as many parts as possible to be machined safely and consistently, so your machine runs nonstop,” Titan says. “You want runtimes in the hours, not minutes. This way, your machinists can program, set up and operate other machines during a long cycle time. It’s a huge advantage.”
Understanding and designing elite work-holding fixtures requires both creativity and experience.
For Titan, creativity might mean replacing a standard six-inch vice with a fixture plate on a four- or eight-sided “tombstone” that rotates within the mill. Each fixture plate slides down over Mitee-Bite pins that have been set into the tombstone. Precision-drilled holes locate perfectly on the pre-set Mitee-Bite pins. Once the fixture plate is in place, you simply take a T-Handle Hex Key or Allen and insert it into the pin and rotate. This expands the pin and locks the fixture plate to the tombstone, allowing each fixture plate to be installed very quickly and stay rigid throughout the long runtime.
“Creativity comes into play when you look at the part and figure out the best way to hold it and hit as many features and datums as possible in a single operation,” Titan says. “You need to hold as many parts as possible, as close together as possible, with rigidity so the CNC machine can run in a consistent and safe manner.”
There is also an art to holding difficult parts, such as those with an “S” shape. A square is easy to deal with, Titan says, but an S has contours and radiuses. The cutterpath may not be complicated, but getting the part to stay put definitely is. It’s critical to figure out how to hold these parts in a way that does not exert too much pressure but stays rigid enough for repeatability from run to run. When tackling this kind of challenge, Titan often cuts the exact shape into the fixture plate and then holds it in place with machinable Mitee-Bite Clamps. The contour of the “S” is actually machined right into the clamp.
Getting experience in fixturing, of course, takes time.
“Many shops won’t tolerate the price and time needed to complete one of these setups, so they put in vices and do it ‘quick and dirty,’” Titan says. “And that’s understandable. Because one piece of a material may cost one thousand dollars for a single job. And some of the larger setups could cost tens of thousands.”
Ironically, most shops that invest in elite fixturing end up saving money while their shops stay busy. In Titan’s view, if you have the right quantities in place and the jobs are repetitive, it’s an absolute must. Advanced fixturing techniques allow the spindles to turn and as Titan puts it, “If the spindle ain’t turning, you ain’t earnin’.”
“Once you invest, it’s done,” he says. “Now your part runs nonstop at a fraction of the previous cost, and your price can compete with any shop in the world because you took the time to tool it up correctly. Shops that do this are a big reason why we’re seeing less outsourcing and more reshoring.”
In a work environment where many companies are fighting over scraps left behind from outsourcing, many young machinists find it difficult to gain the experience necessary to understand advanced fixturing techniques. Older machinists don’t want to teach the younger ones because it could affect their job security. Companies struggling to get work are less motivated to share best practices online or on a public platform. Each company is in its own box and security comes from not sharing.
“That’s one of the reasons why we produce our show TITANS of CNC, formerly TITAN – American Built,” Titan says. “We bring in engineers and product designers and share different techniques about HSM, including fixturing. We show how a tombstone setup can let you run 30 parts at a time instead of four or eight. If you see new ideas, it can inspire you to do the same or come up with something even better.”
Titan also recommends talking to sales reps, even if this contradicts conventional wisdom.
“I was always told that meeting with the tooling guys was a waste of time, but that’s how I got a lot of experience in fixturing,” Titan says. “These guys see every single shop. They know it all. They can tell you what new products are available and how fast you could be running. They want to sell fixtures, sure, and one way they do that is by showing you exactly how to use them.” Titan also makes routine calls to technical support to discuss techniques and to bounce ideas off experts in a particular product.
Overall, the key is remaining open to new ideas and trying new techniques at every opportunity.
“Automation can help you do more with less,” Titan says. “But only if you let it. You have to keep your machines running. And you can’t do that without becoming an expert in fixturing.”
Titan will release his new Online CNC Educational Platform on November 11. The platform, “TITANS of CNC Academy,” will be available free to all teachers, students and machinists who want to learn CAD, CAM and CNC.
Add comment
Connect with: Log in
There are no comments