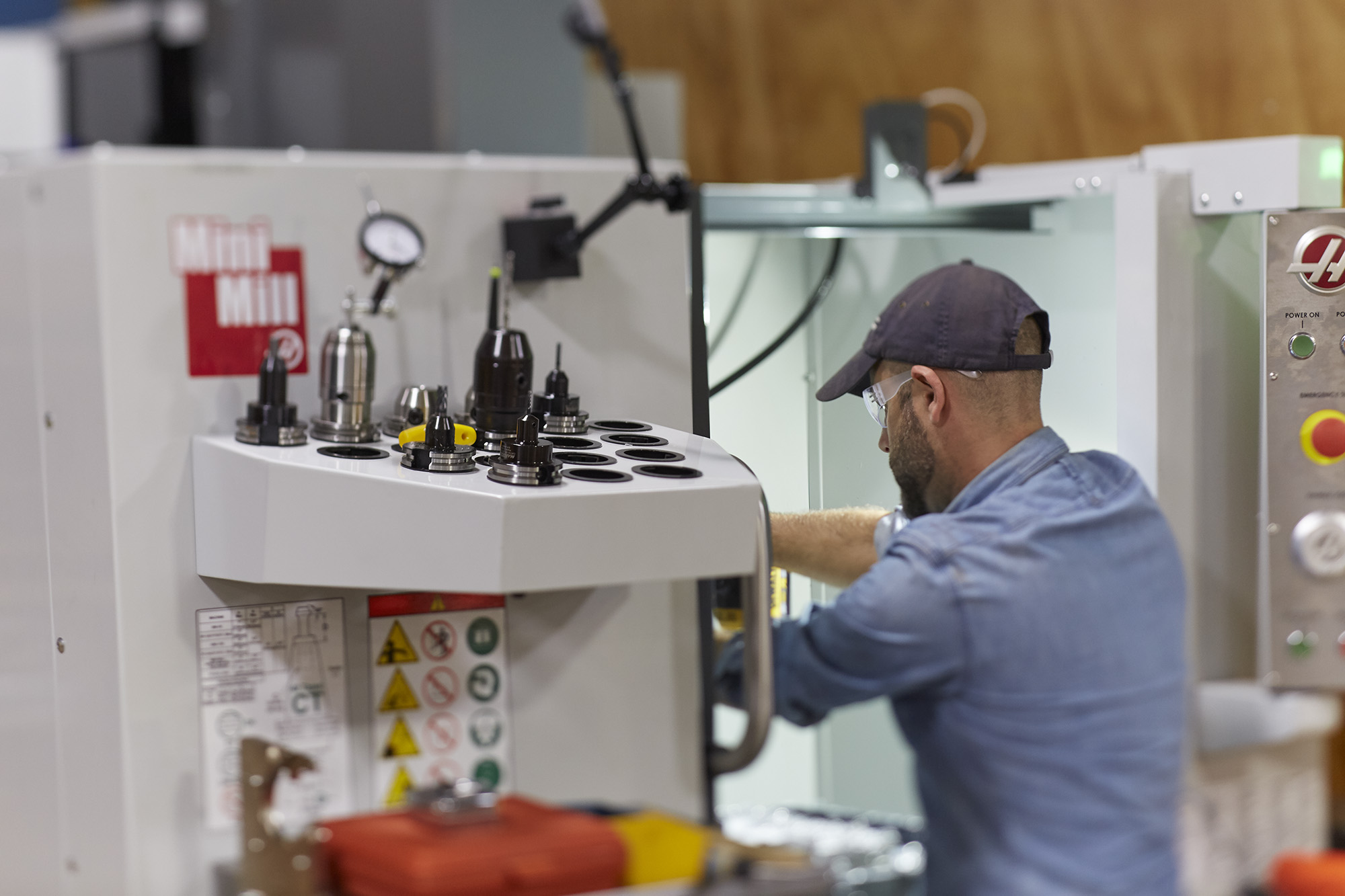
Problem solving in engineering is important, but finding solutions to manufacturing processing problems is crucial to maintaining the flow of the entire supply chain. So, what skills do Manufacturers use?
In manufacturing problem solving, a key method stands out: Lean. This problem solving method focuses in on eliminating waste and finding a solution as quickly and efficiently as possible. This is by far the leading method that manufacturing engineers use to solve problems throughout the production process, so let’s take a look at some of it’s various methods at getting the job done.
Lean manufacturing is broader than just problem solving, it is a way of approaching design, manufacturing, and virtually every aspect of production. This could be said of any problem solving method, after all, as engineers we are trained to anticipate problems and design around projected issues. Looking first at a way to prevent problems from occurring, we can see the process of 5S. 5S is essentially a way of categorizing your workspace and your thought process through, you guessed it, five S categories. This process goes Sort, Set in Order, Shine, Standardize, and Sustain. First you sort your workspace and processes into respective categories, then you organize them, clean and inspect the workstation, create a standard method of workflow, then regularly sustain all of the above processes. Following along with 5S problem solving, or should we say problem prevention, method will allow you to be the most efficient manufacturer you can be.
However, what happens if you actually encounter a problem? After all, even the most categorized and standardized workflow is still going to run into the occasional problem. Your problem is ultimately going to differ depending on your industry, but whatever it may be, we need to apply Root Cause Analysis to the situation. As tempting as it may be to just fix a problem by slapping on some duct tape, it becomes important as a manufacturer to get down to the initial cause. In this method, we have to tap into our inner 5-year-old and ask why as much as humanly possible. Generally, however, it’s good to stop somewhere in the range of asking 5 times as not to annoy your coworkers. When we get into the habit of asking “why?” we begin to see that a small problem on the surface may actually be evidence of a bigger problem developing deeper in your manufacturing process. So, work to solve the root problem, not just the surface issues.
Finding the root cause can take a long time if your process isn’t designed to facilitate problem solving. This means no haphazard engineering, as fun as it may be. It’s important to maintain a Standardized Work Procedure to allow for quick and easy problem solving. As you may be starting to tell, a lot of the Lean problem solving methods aren’t actually problem solving, rather they’re problem prevention.
In many senses, preventing problems from occurring can drastically increase your value as an engineer, although this tends to be a more thankless side of the industry. As a manufacturer, we have to be willing to go the extra mile in the planning and design phase to make problem solving easier down the line. If you do encounter a problem and your assembly line is a mess, try to approach it in the most methodological way possible, and ultimately find the root cause. Working fast is great to keep the assembly line moving, but it means nothing if bigger problems occur in the future as a result.
Sources:
Image Sources:
Add comment
Connect with: Log in
There are no comments