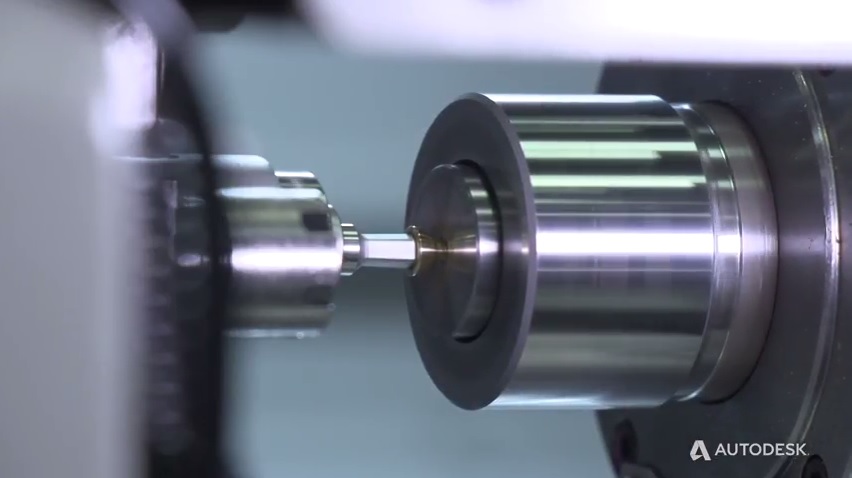
By Sanjay Thakore, Product Marketing Manager
Autodesk, GenSwiss and Tsugami/Rem Sales have teamed up in a three-part collaborative video series focused on screw making, to help explain the benefits of thread whirling, back turning and broaching taking into consideration CAM programming, tooling and machine specifications.
Today’s range of CNC Swiss-type lathes have more capabilities than ever before. They are becoming more prevalent in the market, as more companies are discovering the benefits these sliders can bring to their organizations.
A common application is producing screws, often for the medical industry. These can range from bone screws to orthopaedic implants. The fact that these machines can achieve tight tolerances makes them well suited to screw making. As cutting occurs close to the guide bushing, the material being cut is better supported and basic mechanics tells us; better support means less deflection. Stationary tools and a sliding headstock mean that parts with a larger length to diameter ratio can be produced.
But it’s not solely precision alone that makes these CNC machines appealing. With the onset of smaller lot sizes and shorter deadlines for micro-components, there’s more of a need to increase throughput. Due to the multi-tasking nature of Swiss machines, process synchronization is certainly one way to achieve productivity gains. The option of either synchronizing multiple tool posts on the same spindle (such as pinch milling or follow turning), or on opposing spindles is a great way to lower cycle times and increase throughput.
Another is influenced by tooling. There are often numerous ways to machine a screw on a Swiss machine. Take for example threading; if a high percentage of parts in a shop have threaded profiles, it’s worth considering thread whirling as opposed to single point threading. I’m talking about whirling inserts and holders, rather than a dedicated machine. It may well be more cost-effective given the batch size to invest more money upfront on this type of tooling for a higher return on investment. This is achievable through the benefits typically associated with thread whirling, such as:
• Faster machining of deeper thread forms like Acme
• Prolonged tool life due to the increased strength on the cutting edge of a whirling insert
• More productivity by removing the need for multiple passes
• Reduced deflection through improved rigidity and support, helping to machine longer threads
The same consideration can be applied to turned profiles. The objective is to achieve a finished surface that conforms to the design specification by only using a single pass. This can be a challenge when using conventionally angled turning inserts to turn a shape like a screw head, as there can be issues with clearance when machining past the large diameter. This is where back turning tools come into play with their unique geometry and cutting characteristics.
Back turning can not only provide more clearance when machining past a larger diameter, but can also introduce other benefits to the process. When using wiper geometry, the front side of the tool essentially cuts and the backside burnishes. This adds strength to the leading edge and leaves a high surface finish, removing the need for secondary operations.
One of the final steps in screw making is cutting an often-polygonal shaped internal drive feature on the back of the screw head. This drive feature is what later houses a hex or allen wrench to tighten the screw. To avoid any internal radii in the corners of the drive feature (which you can get from polar milling), a common technique used is broaching. Rotary or wobble broaching is an efficient method for cutting these types of polygonal shapes. The cutter and spindle are synchronized allowing for a single operation to create the finished shape. Other types of broaching include index punch or static.
Brian (Autodesk), Scott (GenSwiss) and Derek (Tsugami/Rem Sales) tell us more about these three applications that can significantly help reduce cycle times and machine parts complete when manufacturing Screws. Check out the videos below for tips, tricks and useful considerations including CAM programming, tooling and machine specs:
Swiss Screw Making: Thread whirling with Autodesk, GenSwiss & Tsugami/Rem Sales
Swiss Screw Making: Back turning with Autodesk, GenSwiss & Tsugami/Rem Sales
Swiss Screw Making: Broaching with Autodesk, GenSwiss & Tsugami/Rem Sales
Add comment
Connect with: Log in
There are no comments