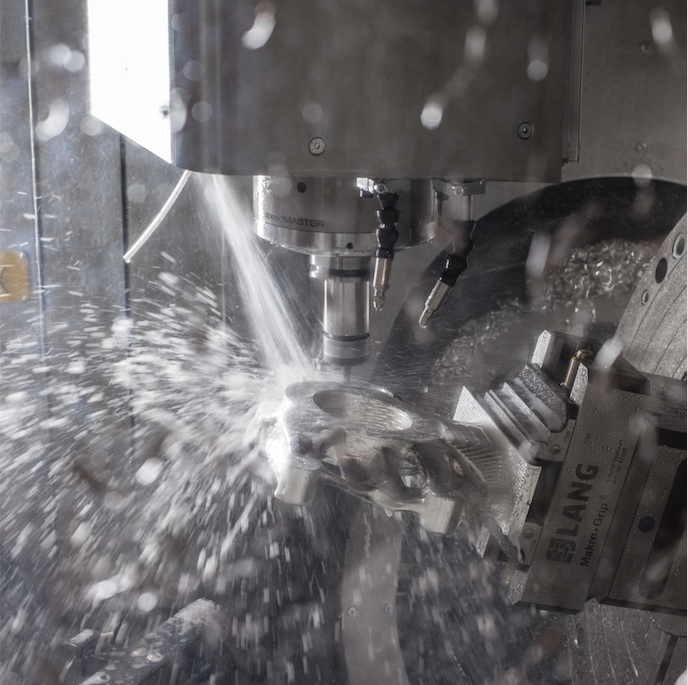
Human creative freedom has always been limited to two fundamental restrictions; the capabilities & limitations of the tools available to make objects, and a solution domain limited to the creativity of individuals. Take for example the development of software for a self-driving car, but apply that solution to a horse drawn carriage. Of course, neither the concept or the need for a solution would have presented itself as a problem to solve ergo the two restrictions. Yet, as the problems we are asked to solve become more complex, the industry will demand access to tools that empower us to explore more ideas in shorter time, automate or eliminate redundant tasks, and explore higher volume use of advanced means of production. The tools we use to design and manufacture to will have to first take into account how the product can be produced so as to accurately inform what is possible with the design of a product.
Furthermore, the pressure to innovate is pervasive across every industry, and touches every person responsible or that contributes to the design process. Creativity is a finite resource. It cannot be scheduled, and most creative types are either trained to or have learned to capture an idea at the point of inspiration in order for it to evolve from idea to physical reality. Just as we have augmented the process of analyzing data through tools like Watson from IBM, innovators will be empowered to explore a solution domain much larger than any one person, or teams of people would be able to explore in a shorter time frame than it would take to converge on a single concept with Generative Design & Manufacturing.
“Overcoming these obstacles throughout the industry poses a higher barrier to adopting new design & manufacturing methodologies than the current higher cost of production.”
New and Emerging Means of Production
For decades engineers and designers have been taught that complexity equals cost. If you consider subtractive machining, stamping, mold tool and die, or other more common means of production, yes. Complexity equals cost. Subtractive processes suggest that every machining operation to remove material increase the cost to manufacture. The inverse can be suggested when you consider additive manufacturing as the means of production. For every gram of material added to the design, it increases cost to manufacture.
Dismissing for a moment the early market costs associated with metal additive, and assuming production costs will reach near parity through technological advances, additive manufacturing makes possible products that cannot be produced by other means. Therefore, taking into consideration available means of production at the point of design opens a realm of potential design solutions beyond the current learned constraints of mainstream production processes. Adopting new design methodologies will take a considerable amount of time to re-train current engineers or incorporate into new curriculum of the next generation of designers, yet with the current pace of technological advancement any curriculum developed is out of date the moment it is printed.
Overcoming these obstacles throughout the industry poses a higher barrier to adopting new design & manufacturing methodologies than the current higher cost of production.
Changing Nature of Work
Product design teams are constantly pressured to introduce more products, solve more problems, with the same or fewer resources as compared to even 20 years ago. An aging labor force, combined with the lack of a repeatable “science” in the design and manufacturing process, the industry is facing a dilemma between the demand to innovate, the desire to produce more locally, and the loss of retiring employees and the tribal knowledge that leaves with them.
In addition to an evolving workforce, nearly every aspect of the human experience is augmented by technology. An industry that in comparison is behind this trend is the design and manufacturing industry. Protectionism, and not in a negative connotation, perhaps plays a key role in the advancement of a hyper connected manufacturing marketplace. Yet more and more organizations are making critical business decisions on mobile devices or connected to WiFi enabled air travel to business systems containing sensitive data. The design and manufacturing industry will expect the same level of access to design data in that it will be unacceptable to delay a production decision or approve a new design proposal to the same speed and efficiency enjoyed in finance, HR, or customer relations.
At the point in which this occurs, the relationship between manufacturers and the tools they use to design, and manufacture products will evolve from documenting an already determined outcome for the means of communicating an idea, to using the technology to define a series of ideas, narrowing the decision process down based on criteria that cannot be defined by geometry. By augmenting the ability to produce a result based on its function, engineers will spend less time defining the shape of an object, and more time making trade-offs between performance, cost, or material availability. When combined with machine learning and artificial intelligence the experience is further augmented by eliminating the need for engineers to repeat common tasks. The tools will learn patterns of decisions that will lead to a more predictive interaction with the tools, providing suggestions based upon potential impact of tooling changes, or insight into where failures have occurred in components of similar purpose.
“This combination of investment in physical space and acquisition of CAM technologies has become a catalyst for change at Autodesk through the functionality we put into our products, and more importantly a change in relationship with our manufacturing customers.”
The Future of Making Things
You may have heard Autodesk talk about each of these trends in a discussion framed around what we call The Future of Making Things. It’s a discussion framework meant to articulate our understanding of the manufacturing landscape similar to what I’ve described above. It provokes a meaningful dialog with customers, and it also provides us direction into where we should be investing our efforts, what direction our products need to go in order to best address the demands of our customers.
Autodesk has taken radical steps to both transition existing customers to a broader set of available functionalities with a subscription to industry focused collections and lowered the barrier of entry with cloud services and consumption-based access to more advanced technology. While these steps are the most public and impactful on existing customers, they are only a part of the overall response to the future market demands that consumers will have of Autodesk technologies.
In 2013 Autodesk launched an exploration of the future of making with the opening of Pier 9 in San Francisco. The effort quickly expanded to the BUILD Space in Boston, and most recently with the Advanced Manufacturing Facility in the UK. These Autodesk Technology Centers (ATC’s) enable Autodesk to firmly transition from a design focused technology provider to a design and manufacturing partner. For nearly 30 years, producing the designs documented through Autodesk’s design tools were the domain of other technology providers. As suggested earlier, with new and emerging means of production this state could no longer provide customers with the tools they needed to embrace the convergence of design and manufacturing. This combination of investment in physical space and acquisition of CAM technologies has become a catalyst for change at Autodesk through the functionality we put into our products, and more importantly a change in relationship with our manufacturing customers.
The ATC’s have become the center for Autodesk to experiment and explore with other risk-takers from industry, startups, and academia, to speculate, validate and test ideas about the future and inform Autodesk’s product and business strategy. The most recent series of explorations have utilized generative design and manufacturing technology that utilize the power of cloud computing to explore alternative manufacturing methodologies, materials, strength and performance criteria, aesthetic, and cost. Not in a series of marginally improved iterations rather, each criterion is considered in parallel providing the engineering team with number product alternatives beyond the ability for any one or teams of engineers to produce in a staggeringly compressed time frame to do so.
Autodesk is introducing a connected design to manufacturing platform that provides line of sight from design to manufacturing, and from manufacturing to design. By connecting all of the information on a single cloud connected platform, more of the design information is available for more services to automate tasks, even provide predictive insight into manufacturability or how a product might perform. Less time is wasted exchanging files between the different disciplines required to design and manufacture products, and the digital continuity of the data is never broken. This is the first critical step toward a more augmented relationship between designers and the tools they use to assist in the design process as opposed to simply utilizing design tools to document an already defined outcome.
Learn More
Throughout the course of the year, Autodesk will host a series of generative design workshops. These hands-on workshops will provide an opportunity to explore how some of the concepts discussed in this article can be applied today. Generative design with Fusion 360 is racially different than the design tools most of us have been trained to use. So familiar we are with those tools, they have influenced how we think about design and engineering, how they have become an extension of our thought patters and the way we mentally dissect design challenges. Here is just a glimpse of what you will learn during the event:
Fusion 360 Generative Design Technology
The workshops will be posted to the Fusion 360 Event Calendar where you will be able to attend the live events. Subscribe to the calendar for updates, or contact me directly at rob.cohee@autodesk.com. This is an exciting opportunity for all of us in the design and manufacturing industry. Don’t miss out on being one of the first to get your hands on this transformative technology. If you can’t make it to one of the live presentations, let’s connect virtually to discuss how you can start incorporating generative into your design process.
Originally posted by Rob Cohee on LinkedIn. You can read the orignalhere.
Add comment
Connect with: Log in
There are no comments