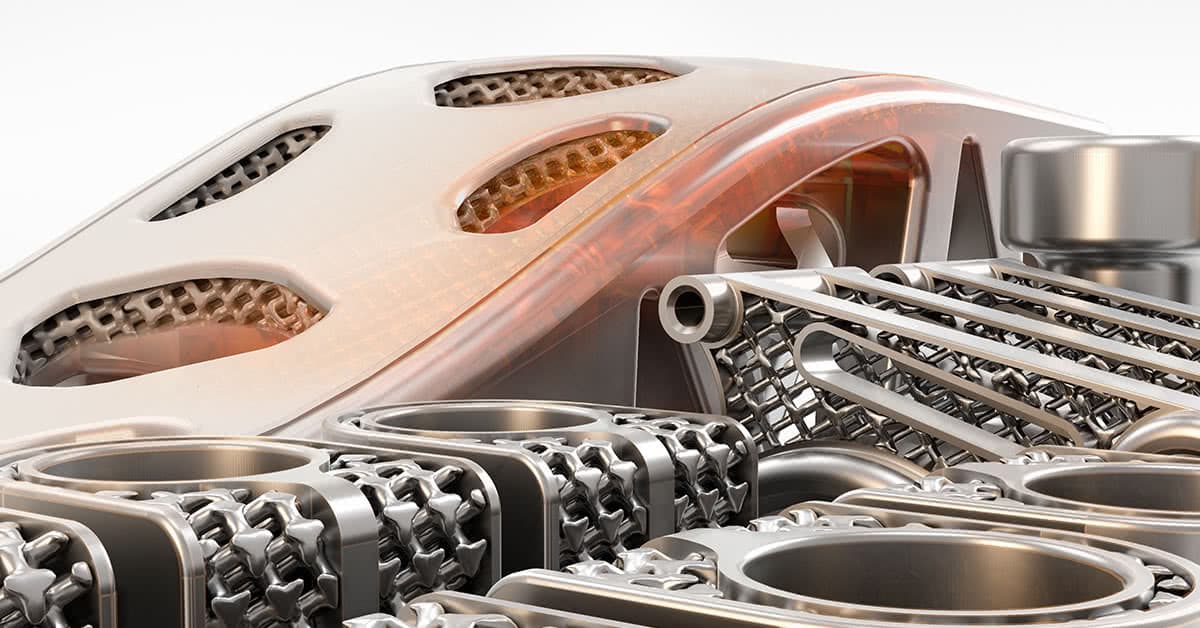
For machine shop operators considering milling machines, one of the most basic questions they have to answer relates to configuration: vertical or horizontal mill? The answer depends on the nature of the business—in particular the type and volume of work being done in the shop—but also cost, capabilities of the workforce, and the facility itself. All these factors contribute to making an informed decision.
Vertical Mills
In vertical mills, the spindle axis is vertically oriented. Milling cutters are held in the spindle and rotate on its axis. Typically the spindle can be extended, or the table raised or lowered to produce the same effect, allowing for plunge cuts and drilling. The two kinds of vertical mills are bed mills and turret mills.
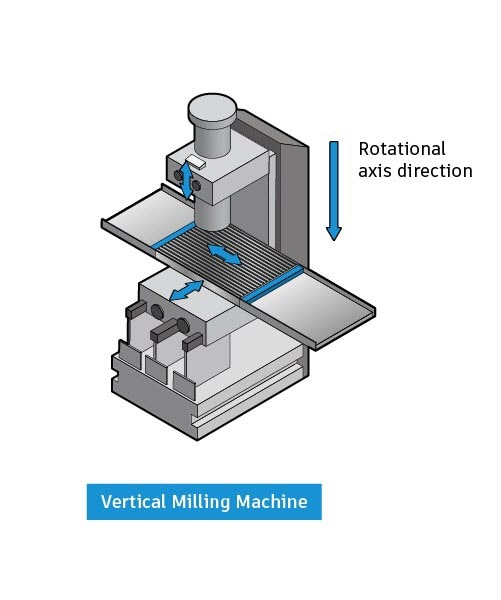
Vertical turret mills have a stationary spindle and the table is moved both perpendicular and parallel to the spindle axis to execute cutting. They often have a quill that allows the milling cutter to be raised and lowered in a manner quite like a drill press. Turret mills provide two methods of cutting in the vertical (Z) direction: by raising or lowering the quill, and by moving the knee.
In vertical bed mills, the table only moves perpendicular to the spindle’s axis, while the spindle itself moves parallel to its own axis.
Horizontal Mills
In horizontal mills, the cutters are mounted on a horizontal spindle across the table. Many horizontal mills also feature a built-in rotary table that allows milling at various angles; this is called a universal table. While end mills and the other types of tools used in vertical mills may be used on horizontal ones, they also have arbor-mounted cutters, called side and face mills, that have a cross section like a circular saw but are generally wider and smaller in diameter. Because the cutters have good support from the arbor and a larger cross-sectional area than an end mill, heavy cuts can be taken, enabling rapid material removal rates.
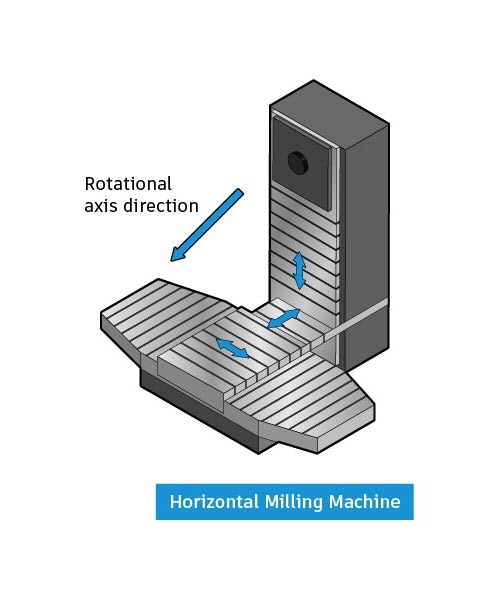
“If you look at general usage in the industry, most of the machines installed have been three-axis vertical mills,” says Angelo Juras, CAM product manager, Fusion 360, at Autodesk. “They’re easy to set up and it’s easy for technicians to access the work table. Also, when you have a workpiece or vise, it’s easy to load and unload because you just set the part on the table and gravity keeps it in place.”
“With a horizontal mill, the spindle points horizontally, which means that the surface the workpiece is mounted on is vertical; so it takes more effort for the operator to load or unload,” notes Juras. “But there are advantages and disadvantages to each configuration beyond ease or difficulty of use.”
Advantages and Disadvantages of Milling Machines
Because of their configuration, horizontal mills have much better chip evacuation, as gravity simply allows the chips to fall. This results in a more refined surface finish, and also prolongs tool life.
“When you’re machining a part with a deep cavity or pocket, all the chips you’re generating in the milling process fall out of the way,” comments Juras. “If you’re doing the same part on a vertical mill, all the chips stay in and can create problematic cutting conditions for tool life management and chip flow.”
Horizontal machines also have a fourth axis “tombstone” capacity. “When you buy a horizontal milling machine, the spindle is pointing horizontally, and the table is horizontal; but it is designed for threaded mounting holes or key slots, where a fixture or base is mounted, called a ‘tombstone.’ The tombstone points vertically and presents the workpiece on another axis,” explains Juras. In this instance, the workpiece is perpendicular to the spindle.
According to Juras, if someone is just starting up a machine shop, 99 percent of the time they start with a basic vertical mill because:
- They’re readily available.
- They’re easy to get into.
- The price point is much lower.
“Typically shops start with the verticals, then as work comes in, they may add a horizontal if it makes sense for the work parts they’re machining,” says Juras.
He recalls his experience when he ran his own machine shop. “We were running a part that took 47 minutes,” he recounts. “It required nine separate operations on a vertical mill. Eventually, I acquired a horizontal mill and reduced those nine operations to two. The part was then done in 22 minutes.”
Juras relates his experience working in R&D for an automotive manufacturer that had both vertical and horizontal mills, in terms of how the work impacts the better mill configuration: “We were doing fast turnaround of components, and each one required that a series of questions be asked and answered. How fast was it needed? How many operations were needed to produce the part? What was the availability of the equipment? How many were needed? All these questions determined whether we’d put the part on a vertical or horizontal mill. Typically, in R&D, it depends on the number of faces to be machined; but generally it was easier to get on and off the vertical mills. There were always pros and cons. So much comes down to workholding and fixturing.”
Two other issues make vertical mills attractive to start-up operations: training and real estate. In an age where manufacturers are crying out for qualified machinists, many more are experienced with vertical mills than horizontal ones. A tool is only as good as those who operate it, so in addition to the much greater capital cost of horizontal mills (typically three to four times the cost of a vertical mill), the shop owner has to consider the time and investment involved in training personnel for equipment they have no prior experience in using.
Further, particularly in areas where real estate value is high, the smaller footprint of vertical mills is a benefit. “I have seen small horizontals and big verticals, but that’s an exception,” says Juras. “Generally vertical mills take up significantly less space than horizontals.”
Final Milling Machine Considerations
To reiterate the general advantages of each mill configuration:
Verticals
- Significantly lower cost. With verticals available at $80K and horizontals running from $250K to $400K, its not surprising that machine shops purchase verticals over horizontals at a rate of four times or greater on an annual basis.
- Ease of use. It’s easier to see what’s going on inside a vertical mill.
- A greater pool of machinists is familiar with the technology.
- Smaller footprint—requires less floor space.
Horizontals
- Ability to execute parts with fewer operations and more complicated parts, and achieve greater spindle up time through less time expended on set up and fixturing for multiple operations.
- Greater throughput. A horizontal mill typically can do the work of three or more vertical mills.
- Can achieve better chip evacuation, improve finished work, and prolong tool life.
“In the end, it depends on the work and how far your business has evolved,” says Juras. “When you start out, buying that vertical mill is like getting your first car. You need it to get from point A to point B, to get you to work, etc. Once you’ve worked for a while and improved your situation, you move up to a better car. That’s the way it is with machine shops. Once they‘ve been in business and proved themselves—acquired more sophisticated parts to machine, started to product in volume, and accrued investment capital—they may find adding or moving up to a horizontal mill makes sense.”
This post was originally published on Autodesk’s Resource Center. You can read the original and other’s like it here.
Add comment
Connect with: Log in
There are no comments