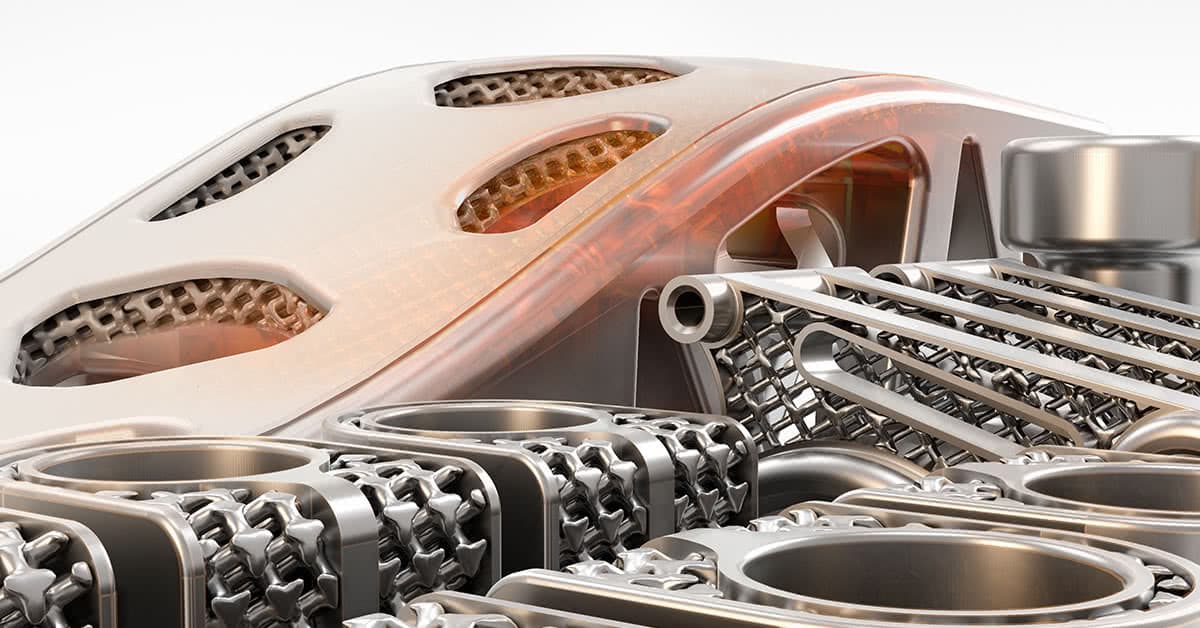
Lean manufacturing is the concept and theory behind prioritizing waste reduction in your manufacturing and production processes. Going lean is widely held has a steadfast way to improve your output and, in turn, your bottom line.
While this concept might seem like a slam dunk, that may not necessarily be the case.
Tools vs Philosophy
When you’re a manufacturer or engineer, you have a tendency to like tools. This goes for that shiny set of wrenches in your shop as well as that app that you thought would help keep you organized.
The tools that the concept of lean manufacturing provides are fantastic, and they can do great things for organizations big and small. The challenge comes when implementation of the tools takes precedence over the philosophy of going lean.
Implementing the tools of going lean (like Value Stream Mapping (VSM), Poka-Yoke, etc.) is important, but adoption of the philosophy throughout your manufacturing network is important. This can be a challenge for both large and small manufacturing orgs.
Your entire team needs to be dedicated to not only implementing lean processes, but also be prepared to help identify the challenges that going lean can solve – and more importantly, the challenges that going lean CAN’T solve.
Finding the Right Problems
Most of the lean manufacturing concept comes from the Toyota Production System (TPS), which focused on reducing waste. When Toyota implemented this style of production management, they had some very specific issues to address – specifically, wasted resources.
The issue with this parallels the old adage: When you have a hammer, every problem looks like a nail.
Many lean initiatives are still based on the TPS model, which is a great case study to exemplify what lean can do, but the tools with TPS were put to use for specific problems. The tools might not be beneficial when applied the same way at other companies, but the theory behind the tools holds true.
The best way to solve this is to study up on the method of finding the root cause of your manufacturing challenges and then finding ways to adapt the tools of going lean to your process.
Solving Problems Makes More Problems
While the concept of going lean is appealing and potentially valuable, doing so at the sacrifice of vital elements of your supply chain or design process can be detrimental to your business.
Going the path of least resistance may not be the best solution. Which is why identifying the right problems – finding out what the nail looks like before picking out a hammer – is key to successfully going lean.
While these aren’t really reasons you shouldn’t go lean, they are definitely pitfalls to watch out for as you implement this tried and true method of making your manufacturing better.