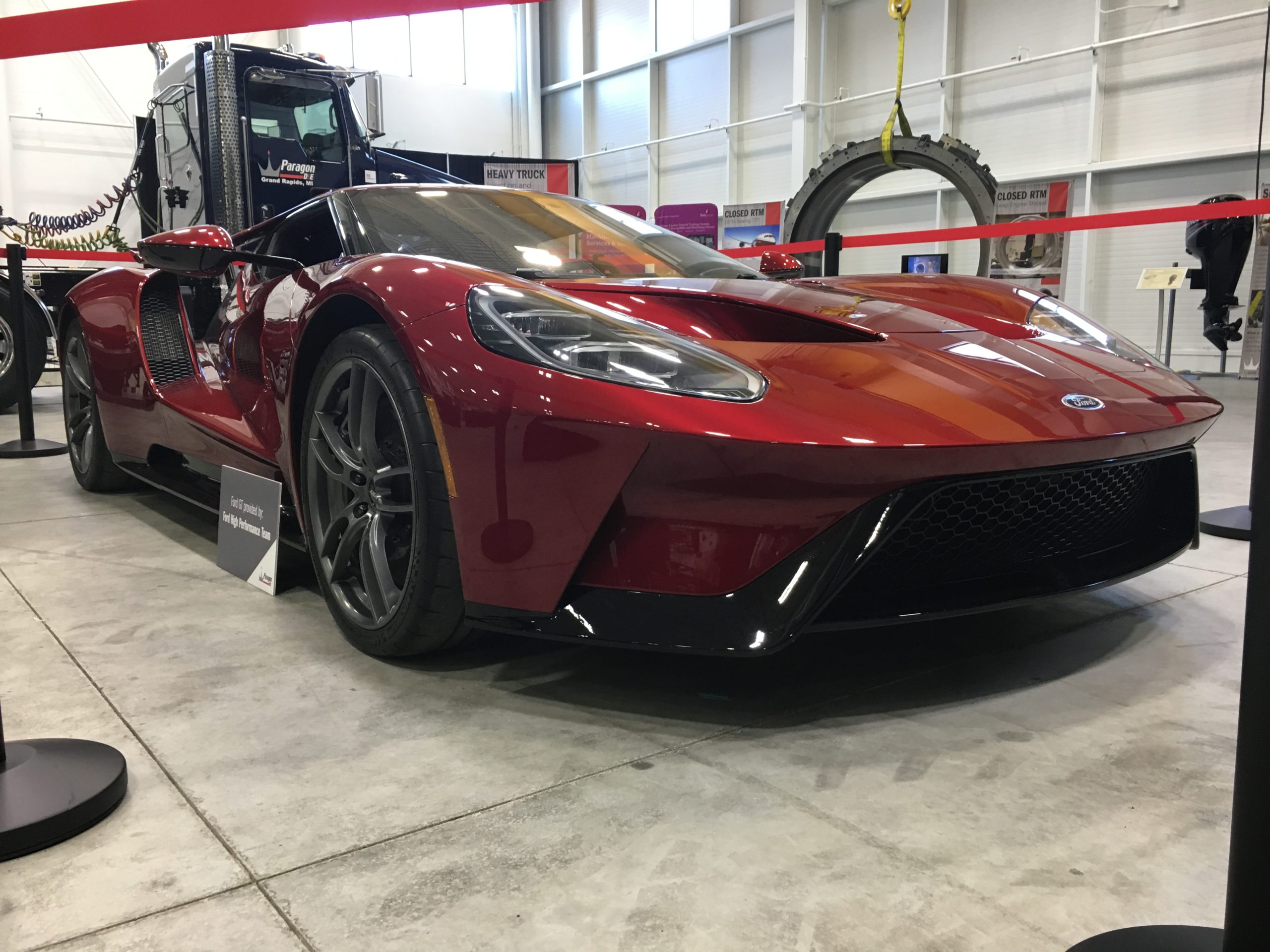
The automotive industry has always been on the forefront of technological developments and tends to be the first adopter of new technology. Even if these new technologies are only used initially on their concept vehicles or in high-performance racing vehicles. The massive manufacturing advances being made across the board point to a future of significant energy and cost efficiency, and generative design has placed itself firmly in the middle of this revolution.
What is generative design?
Generative design is machine-learning-assisted design and is used to optimize a given design based on a set of user-specified parameters. Autodesk is at the forefront of this technology, and has termed its system ‘Autodesk Generative Design’ (AGD).
AGD mimics natural evolution in the way it iterates a design solution based on external factors. It must not be confused with topology optimization which is focused on improving an existing design. Furthermore, it takes manufacturability into account when creating all the different configurations. This ensures that you don’t end up with a good-looking design that would be completely impractical to manufacture. Another advantage is that homogenous parts can be created that replace sub-assemblies of multiple different components.
Types of inputs
When a designer sets up an analysis in AGD, the following parameters must be defined:
- Material
- Part Mass
- Part Size
- Manufacturing Methods
- Cost Constraints
These factors are then used as a basis for the algorithms to iterate through. Multiple configurations are presented to the designer and each of these configurations meet all the criteria in different ratios. The designer can then choose the best configuration. However, if additive manufacturing techniques like SLS (Selective Laser Sintering) are being used then it is not necessary to do any modifications on the part as it can be directly printed.
Automotive applications
Generative design has massive potential in the automotive industry since there are thousands of components that make up a vehicle, and many of these can be revised using this system.
General Motors have historically been one of the early adopters of new manufacturing technologies. For example, GM has been 3D printing components for the last decade and has created over 250,000 prototype 3D-printed parts. GM plans on using AGD software for mass reduction and part consolidation. The first test case at GM was a seat bracket that was made 20% lighter and 40% stronger than the original part. Furthermore, the original bracket consisted of eight parts and the redesigned bracket only consisted of one part, thus drastically reducing component complexity and manufacturing time.
There are many benefits of using AGD for automotive engineering, some are listed below:
- Cost Efficiency – Components created with AGD use less materials, less energy and less time. This results in an overall cost saving for automotive manufacturers, creating more value for customers.
- Simulation – Usually components are designed and put through extensive simulations to verify the design, thereafter the part is tweaked and simulations are run again. With AGD, the simulations are run during the design phase and each of the thousands of iterations created have already passed a strength test.
- Modeling – This design tool also has the advantage of reducing time spent on the development of conceptual designs as the 3D CAD (Computer Aided Design) model is generated as part of the process, freeing up the designer to focus on more top-level design concerns. Once the designer decides on the final configuration, it can be slightly modified to meet the designer’s preference.
In conclusion
Autodesk is the undeniable leader in the practical application of generative design. Their latest iteration of the software can be found in their innovative design package, Fusion 360. This allows seamless switching between the traditional CAD design environment and the AGD system.
If the design is too organic for traditional manufacturing techniques you can export the model into Autodesk’s Netfabb package to prepare the file for metal 3D printing.
With the advent of ever more efficient additive manufacturing techniques, AGD will become increasingly relevant as an alternative product development technique, and we can expect to see organically designed components appear in our vehicles, buildings and consumer products.
Add comment
Connect with: Log in
There are no comments