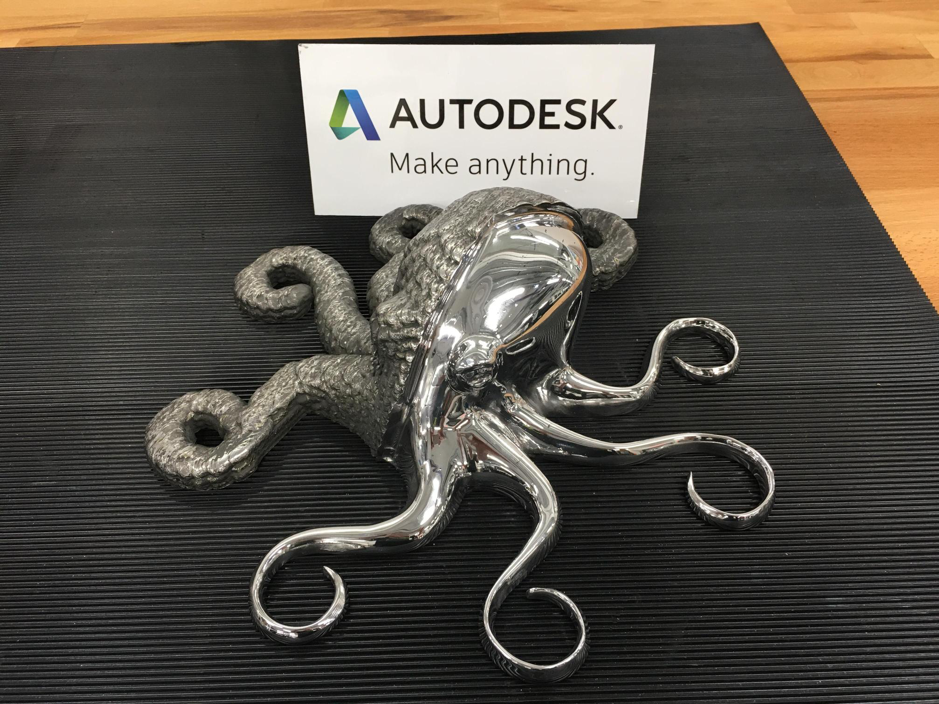
High-Rate Additive Manufacturing ‘Olly’ the Octopus
Autodesk PowerMill 2019 extended its hybrid capabilities this year to include high-rate Additive Manufacturing (AM). For decades, PowerMill has been an expert CAM product for subtractive machining. Over the years it has developed into an advanced hybrid solution, incorporating off-line robot programming, and for the first time high-rate additive functionalities.
PowerMill Additive is a plug-in that enables you to create tool-paths for additive or hybrid manufacturing. It utilizes PowerMill’s existing CNC and robot capabilities to create multi-axis additive tool-paths with detailed process parameter control along every point of the toolpath. These process parameters enable you to finely control the operations of deposition at a toolpath point level.
Metal 3D Printing Process
High-rate AM, commonly referred to as Directed Energy Deposition (DED), is where a metal wire or powder is combined with an energy source to deposit material directly onto a build tray or an existing part. Parts are typically large, without the need for tight tolerances.
DED is generally used to repair and maintain existing parts. DED machines usually mount a nozzle onto a multi-axis arm, which then deposits the metal feedstock to the surface. When used with 5- or 6-axis machines, the material can be deposited from nearly any angle and is melted upon deposition with a laser or electron beam. This process means DED can be used to build objects very quickly and is only limited in size by the reach of the robotic arm.
Education and the light-bulb moment
In the latest extension of PowerMill Additive, training is available on demand for partners, customers and staff wanting to gain a deeper understanding of DED along with machine/robot capabilities.
In most cases, attendees use their time in training to make small wire or power formed parts. However, it was technical consultant, Lee Sanders who started exploring different ways of depositing material for more complex shapes. For Lee, the light-bulb moment came from his involvement in the company’s Office of the CTO-OCTO, which explains the Octopus.
Eight arms are better than one
Octopuses are intelligent, behaviourally flexible, interested in play, and good at learning, which is much like those in OCTO.
Christened ‘Olly’ the octopus, the eight-armed part soon became an internet hit, reaching 100,000 plus views on LinkedIn alone. It was with this drive Lee decided to refine Olly and machine half the façade to show off PowerMill’s Additive and Subtractive capabilities.
Olly is a worthy example of how metal parts can be built from scratch to near-net-shape and machined back, generating a huge interest online.
Countdown to IMTS
For a more information and demo, visit us at IMTS 2018 Chicago.
#AutodeskIMTS2018