Additive manufacturing made a splash in the consumer market over a decade ago, but 3D printing has been around much longer than that. Now that 3D printers are available and functional for anybody with the internet and $200 USD, they have become a necessary tool in most engineering environments. But what about manufacturing?
1. Rapid prototyping
Printing with PLA or ABS plastic provides the opportunity for fairly quick and inexpensive prototyping. While you might think that should be left to an engineering firm, prototyping in a machine shop can save you headaches by getting a part in-hand before cutting (and potentially wasting) raw material.
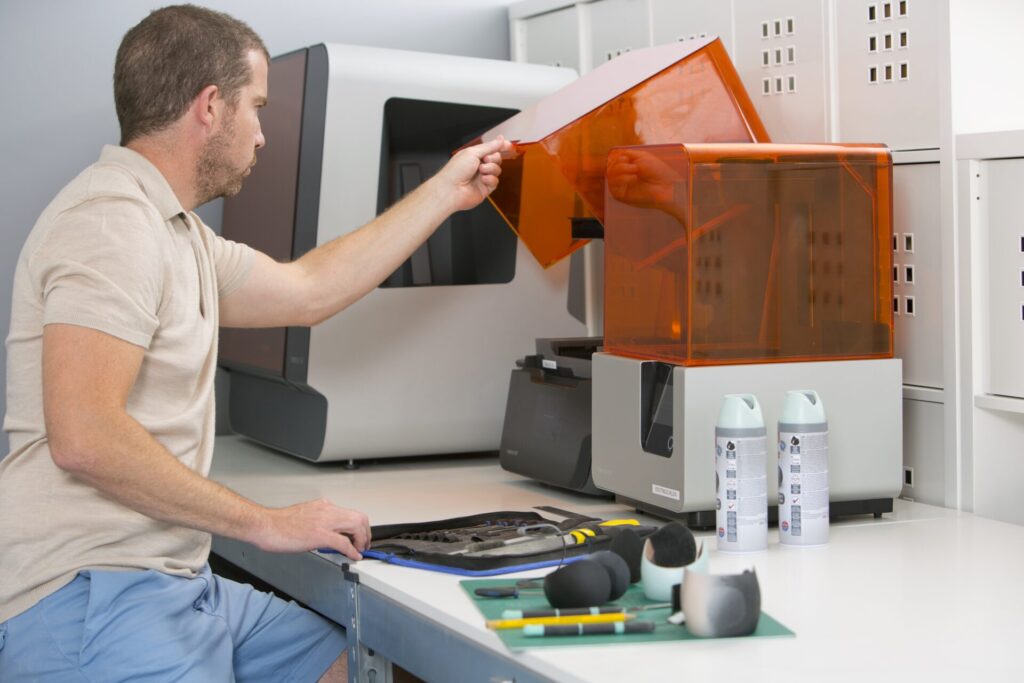
Moving from CAD to prototype to CAM to machining is an efficient workflow that can help not only make parts faster, but it can help make better parts more efficiently. What’s more, it helps to demonstrate workholding needs and manufacturing challenges that you can easily present to a customer.
Speaking of workholding, there are a number of opportunities to utilize a 3D printer for workholding. Creating soft jaws is quick and easy with a 3D printer, so long as you aren’t planning to machine with a lot of force.
Printed workholding is also a great way to hold odd-shaped parts or if you want the workholding to be more sacrificial than aluminum.
2. Simplifying Design for manufacturing (DFM)
Similar to the perks of prototyping in a machine shop with a 3D printer, they can also help simplify the DFM process. As the gap continues to close between designers/engineers and manufacturers, the need for properly designing parts for manufacturing is more apparent than ever. 3D printing in the machine shop provides the opportunity to test and vet designs before they are ever manufactured.
3. Affordable metal 3D printing
Metal 3D printers used to cost millions of dollars, and the material wasn’t much less, but they helped make unique parts that could only be 3D printed in the high-end aerospace and automotive industries. With the cost of this technology dropping, these printers are emerging in more industrial spaces.
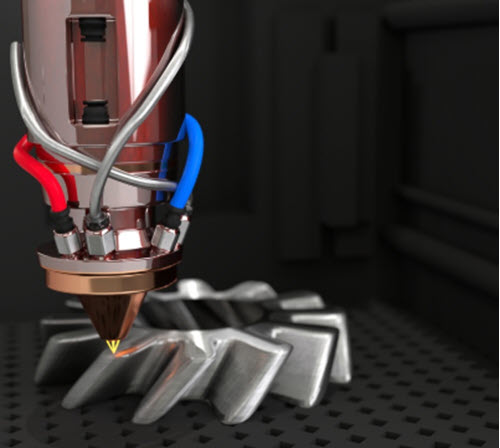
These printers have the ability to help machine shops save money. Similar to casting a part, metal printers can create parts without purchasing billet, which can then be machined to a refined tolerance or finish. Having this ability to essentially create a cast without a mold provides some unique opportunities for a machine shop.
Not the end of machining
While the need for 3D printers in the machine shop may be relatively new, they are far from replacing traditional manufacturing. 3D printing has become much less expensive, and it’s the perfect tool to help make the machine shops become more efficient and productive.