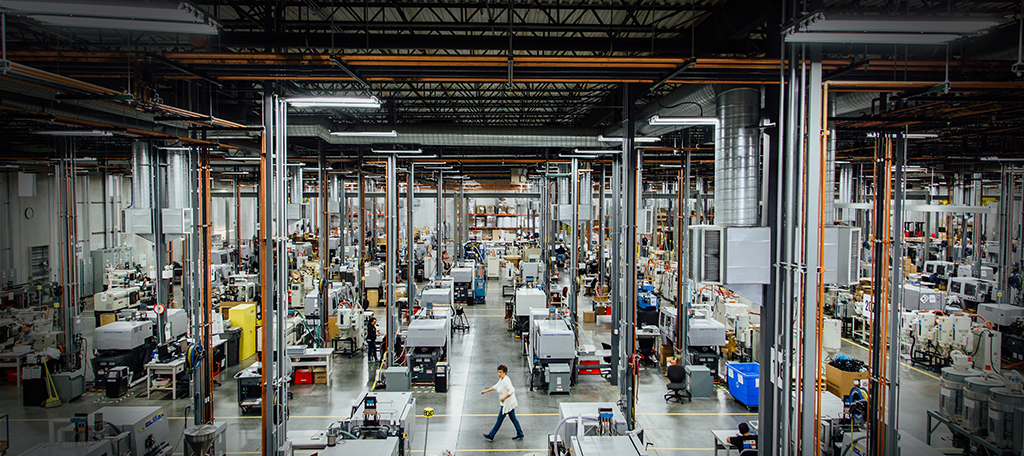
Additive manufacturing (AM) is the process by which a 3D object is created by adding successive layers of material in predetermined shapes and sizes. The shape of the layers is configured by software that analyzes an imported digital design model. It is sometimes referred to as Additive Layer Manufacturing (ALM), laser melting or, most commonly, 3D printing.
Renishaw is a large engineering company that has an additive manufacturing wing specializing in the manufacture of metal products for industrial, aerospace, automotive and medical applications.
Autodesk has been involved in developing cutting-edge design, engineering, and manufacturing software for many years. They are leading the way in creating Computer-Aided Manufacturing (CAM) software, including additive manufacturing with their Netfabb package.
In 2016, Autodesk and Renishaw AM started collaborating on developing the software, with a focus on integrating it with Renishaw’s additive manufacturing platforms such as the QuantAM workbench.
Why is this collaboration good news for manufacturing?
With manufacturing undergoing huge changes at the moment, as the industry transitions to smart factories and AI-driven manufacturing, there is an increasing focus on creating joined-up and interconnected workflows.
In other words, there needs to be seamless integration between the various manufacturing processes, and nowhere is this truer than in additive manufacturing. The complexity of the software, technology, and equipment involved means that if companies work on different parts of the process completely independently, there will be compatibility and integration problems ahead.
With the coming together of two companies that are pioneering the field of additive manufacturing, the future is likely to be bright and complication-free.
For instance, the tool paths that are created in Netfabb will translate seamlessly to Renishaw AM’s hardware, ensuring complete precision and high-quality finished products.
The collaboration also allows for greater optimization of the process. Netfabb has been developed to use multiple print-heads working simultaneously to 3D print a single item. Therefore, Renishaw AM has adapted their equipment to enable this innovation by including multiple print-heads, thereby speeding up production time.
The potential for further innovation
Stephen Anderson, software director at Renishaw AM, has stated that, “…we are delighted to be working with Autodesk to enable a streamlined additive manufacturing print experience for our joint customers. We look forward to future integration opportunities.”
This signals a desire from both parties to continue their collaboration and to drive forward innovation.
So, what could this mean for the manufacturing industry?
It will almost certainly lead to more efficient and streamlined processes. Autodesk are focused on cloud-based, smart workflows and with the help of Renishaw they can design these systems to integrate perfectly with 3D printing equipment. This will have a massive impact on profitability by speeding up operations and cutting costs.
As Autodesk’s Manufacturing Strategy Manager Mark Forth puts it, “The addition of cloud-based simulation, subtractive workflow capabilities, and collaborative 3D printing means that we are now providing our customers with the most comprehensive and powerful additive solution on the market.”
For companies that produce specialist 3D printed parts, medical implants for instance, this means considerable cost savings, some of which can be passed on to the customer. Therefore, it’s not an exaggeration to say that this collaboration can have a positive effect on wider society as well as the manufacturing industry.
A fully integrated AM workflow
The potential for further collaboration between the two companies is clear. Renishaw is heavily involved in metrology (the science of measurement), which is an integral part of the manufacturing process.
The future could see Autodesk generative design software automatically designing highly-optimized parts that are translated to 3D printing commands in Netfabb. Netfabb then automatically controls a Renishaw AM system to create the part which is then quality checked using Renishaw IoT sensors and probes. The data is then relayed back to Netfabb’s central cloud-based interface.
This vision of a sophisticated, yet affordable, smart manufacturing solution isn’t far off. In fact, the technology is already developed and available, so expect to see distributors offering these fully joined-up systems shortly.
Add comment
Connect with: Log in
There are no comments