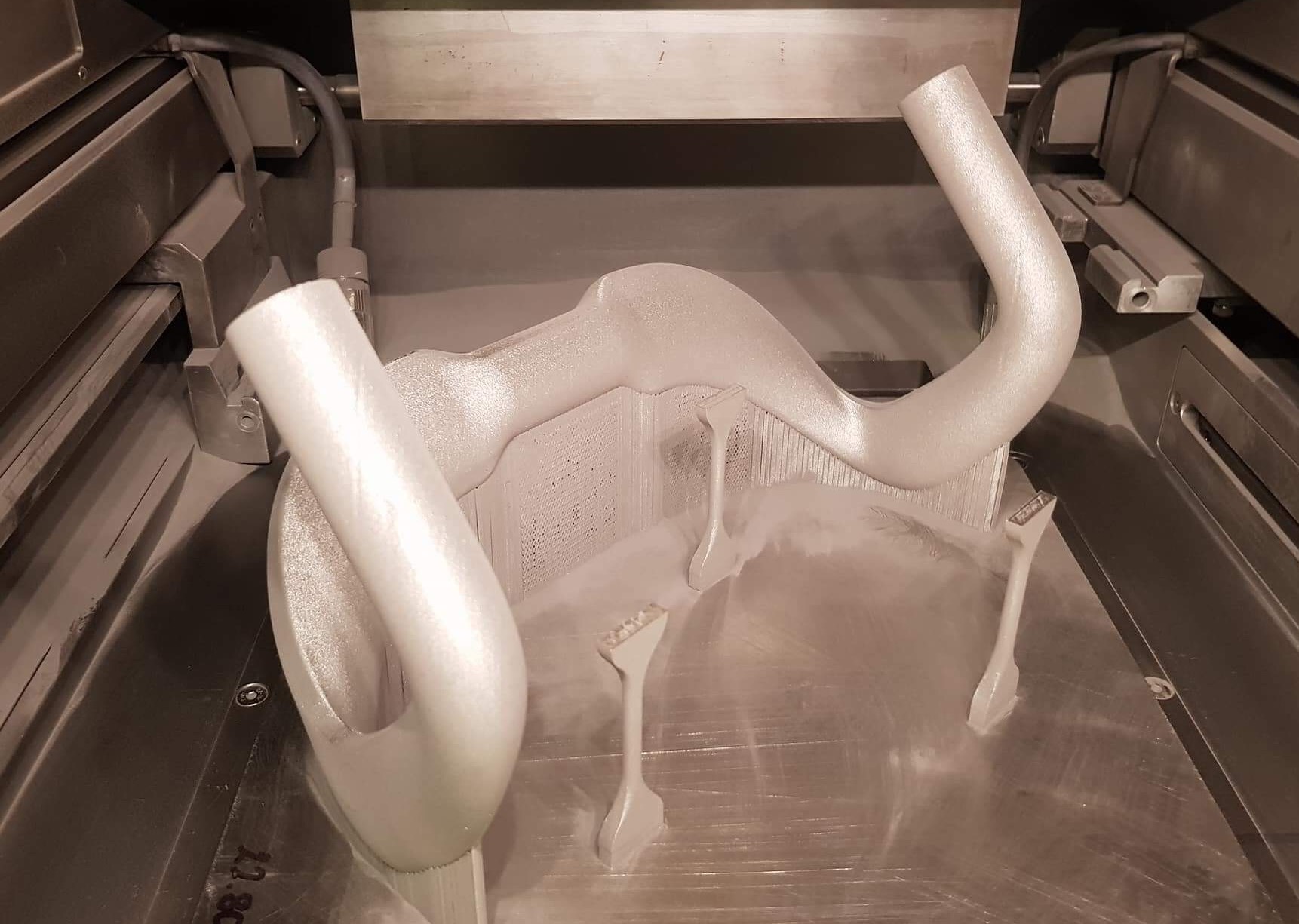
“As recently as last week I was down in Wellington working with a colleague and I told them to look into Netfabb because they were having trouble trying to process this one particularly difficult job. They couldn’t get it done no matter what they tried. So they gave it to us and we had it up and running in a couple hours. We turn our parts around quickly, that’s why customers choose RAM3D. Netfabb helps make that happen.”
— Philip Owen, Workshop Manager at RAM3D
High-volume metal additive manufacturing with leading Australasia bureau
RAM3D is the largest provider of 3D metal printing in Australasia, producing hundreds of parts every week and are printing 12,000 parts per year currently. They are a market leader in additive manufacturing, focusing on selective laser melting (SLM) in titanium, stainless steel 15-5ph and 316L, Inconel metal, and aluminum alloy powders.
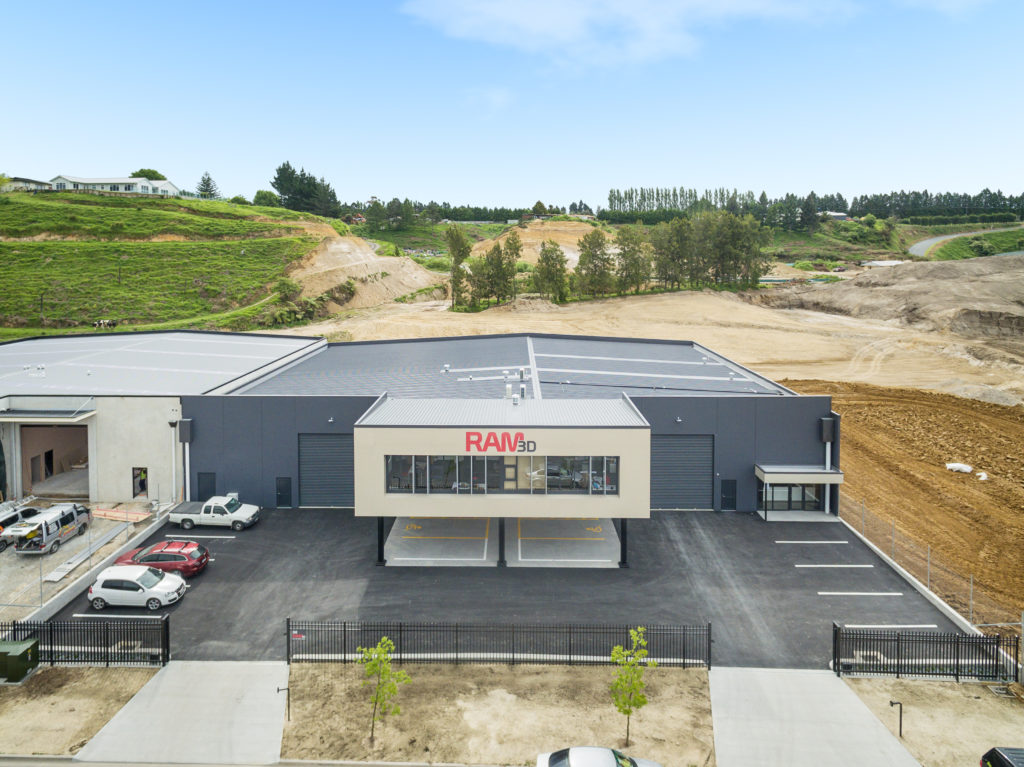
Originally the R&D arm of a titanium powder research organization (TiDA), the founders of RAM3D started metal 3D printing in 2009 as a research project but soon recognized the rapidly growing popularity of metal additive manufacturing and formed their own company in 2013. Today, the state-of-the-art RAM3D shop includes seven Renishaw AM250 SLM machines and one SLM Solutions 280HL. With these machines, RAM3D serves a wide variety of customers in the aerospace, defense, food packaging, marine, sports and specialty industrial markets. This mix brings its own set of challenges to daily workflow.
“We’ll be doing an aerospace part one day and the next it’s a keychain,” says Philip Owen, workshop manager. “Today it was a custom stereo faceplate. Then it’s bicycle parts and bottle openers, so quite a combination. That’s what is so cool about 3D printing. You can have six separate industries on the same build plate.”
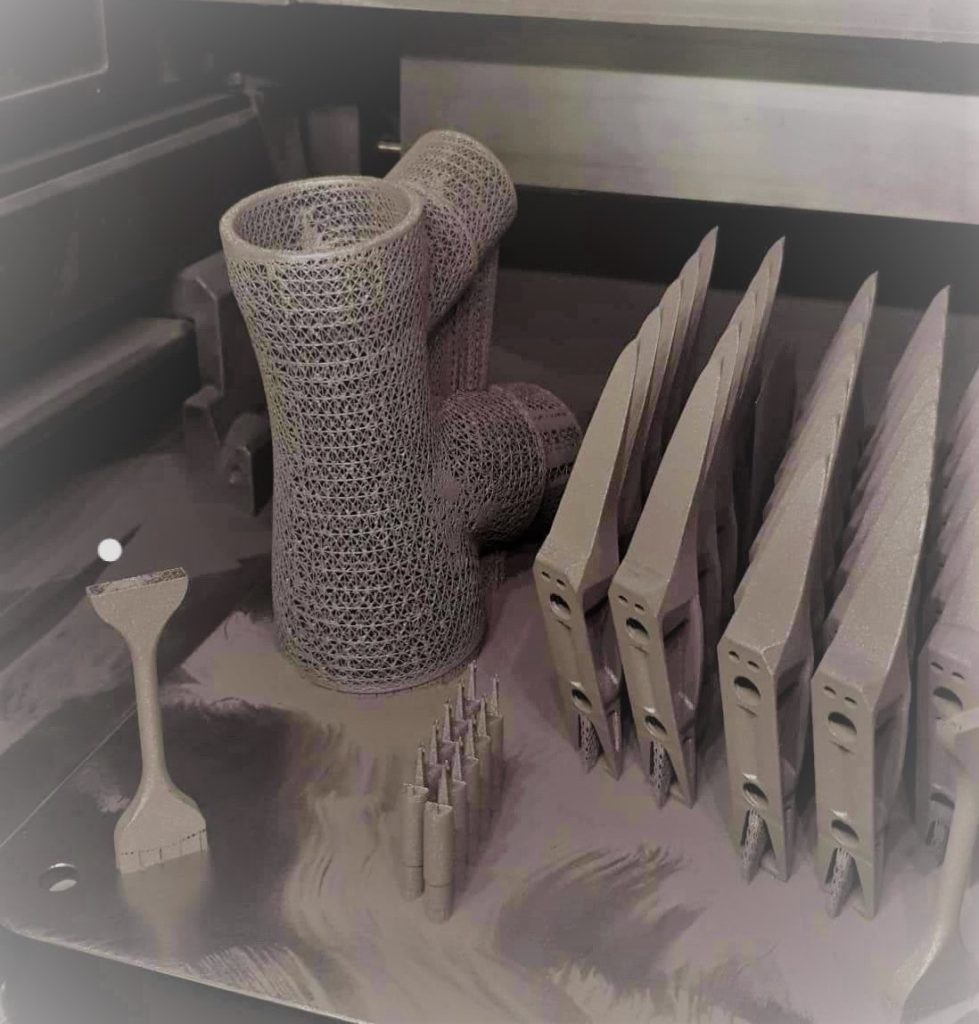
This variety of part designs and customer needs is also why metal 3D printing has challenging workflows. A Tier 1 automotive supplier, for example, might have an injection molding shop that only serves one OEM. But in the additive world, variety is the norm. But when you throw in a high volume of orders, the daily experience gets complicated.
“If you’re doing a production run, you drag and drop the parts on the plate and go,” Owen says. “You know how everything will be supported. But when you have a variety, the challenge is supporting them all uniquely and being confident it will run right the first time. Customers don’t understand the 3d printing process and still expect their parts on deadline, often the next day.”
What that means for RAM3D is that the software used to prepare the build plate needs to work seamlessly. Unfortunately, that’s not what the company’s previous software delivered.
“We were having issues trying to export build data and it would hang up, or it would process the job but it wouldn’t work on the machine and it was very difficult to figure out why,” Owen says. “No software is perfect. But we were not getting good support from the provider. They made it seem like it was our problem, and they weren’t willing to help us. We needed a change.”
Making the switch
Owen and Warwick Downing, CEO, were somewhat familiar with Autodesk Netfabb and successfully decided to run the software alongside the previous software for six months to see how they compared. It didn’t take long for the team to decide.
“Within a very short time, we were doing 99% of our work with Netfabb,” Owen says. “We had one customer who needed flight-certified parts, so he couldn’t switch until the part design changed. But as soon as it did, we were running everything on Netfabb, whether it was stainless steel 15-5ph, stainless steel 316L, Inconel 718, aluminum, or titanium.”
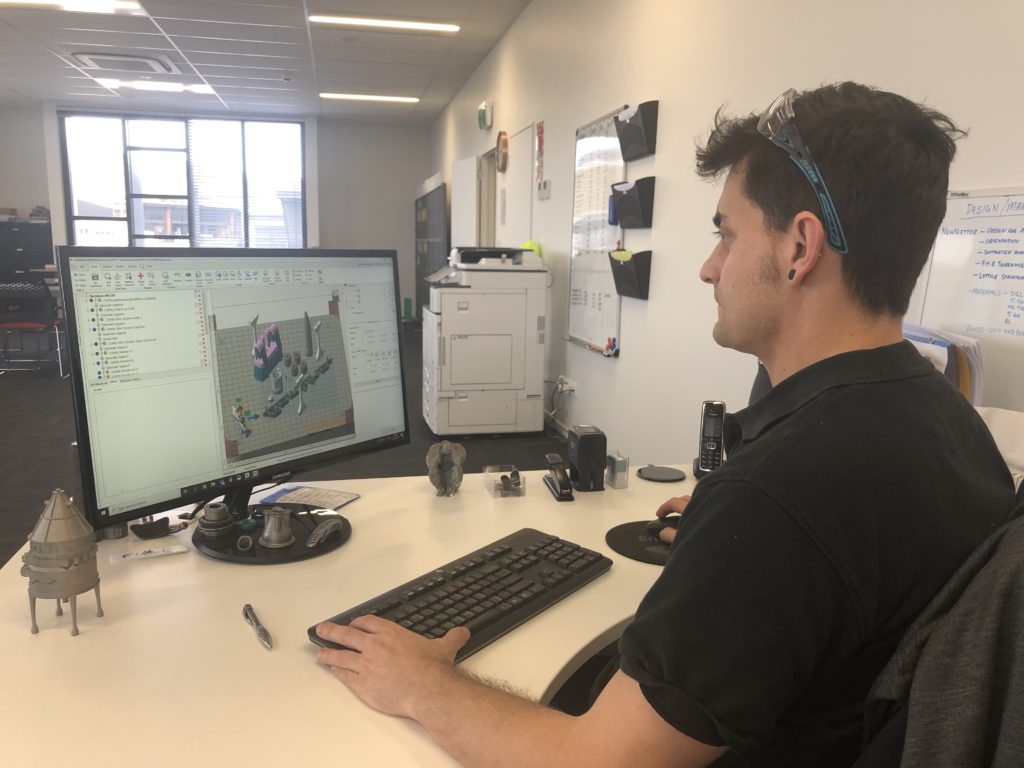
Owen had never used Netfabb before, but the interface made it relatively simple to figure out how to complete his normal daily tasks.
“It’s very easy to use and I like the interface,” Owen says. “It’s very convenient because I can see the build time change as I add parts to the plate, as well as build volume and build height. On the other side is the toolpath visualization, so I can see ‘spikes’ that represent a potential slowdown in scan time that could put a line or a warp in the build. I didn’t have this capability previously.”
Saving time, increasing quality
Switching to Netfabb has delivered important advantages for RAM3D. Using toolpath visualization, for example, has made Owen and others more confident that the build will be correct before exporting the data.
“That one feature has sped up our workflow,” Owen says. “We used to do one particular repeat job in about six hours from the 3D model to export. With Netfabb we reduce this time by 50%, and I think we’ll see more gains as we learn it better.”
Surface quality of parts has also improved significantly, due to Netfabb’s downskin control. This allows parts to be supported adequately with fewer points of contact, which means there are fewer areas that require post-processing cleanup with a die grinder. Ultimately this means a more consistent part surface, which customers appreciate, and higher efficiency for RAM3D.
“We have complex, multi-part build plates that used to take us three hours or more to clean up,” Owen says. “And with Netfabb it’s down to one hour, which the team really likes. Even if it’s just one or two plates a week, that’s a lot of time saved.”

Minimizing support is a relatively simple task in Netfabb, according to Owen, because he can specify the total volume of support material and then quickly review part orientations that conform to the desired volume. Netfabb also makes it possible to clone supports for more custom parts, which reduces calculation times on production runs, as well as automatically delete anchors. All of this means more time saved, less support material used, and less waste.
Partners in problem-solving
One of the most important differences for Owen and RAM3D, however, echoes the original reason why they wanted to switch in the first place: support. While the previous provider took a hands-off approach, the Autodesk team sees collaborative problem-solving as part of their responsibility.
“One thing we found with Autodesk is they are really, really good at coming back to us with a good solution if we do find an issue,” Phil says. “For us, that’s really important. Because the sooner we get the issue sorted out, the sooner our shop is back up and running.”
Owen has already recommended Netfabb to most of the companies with 3D printers in New Zealand.
“As recently as last week I was down in Wellington working with a colleague and I told them to look into Netfabb because they were having trouble trying to process this one particularly difficult job,” Owen says. “They couldn’t get it done no matter what they tried. So, they gave it to us and we had it up and running in a couple hours. We turn our parts around quickly, that’s why customers choose RAM3D. Netfabb helps make that happen.”
We have complex, multi-part build plates that used to take us three hours or more to clean up. And with Netfabb it’s down to one hour, which the team really likes. Even if it’s just one or two plates a week, that’s a lot of time saved.”
— Philip Owen, Workshop Manager at RAM3D
Add comment
Connect with: Log in
There are no comments