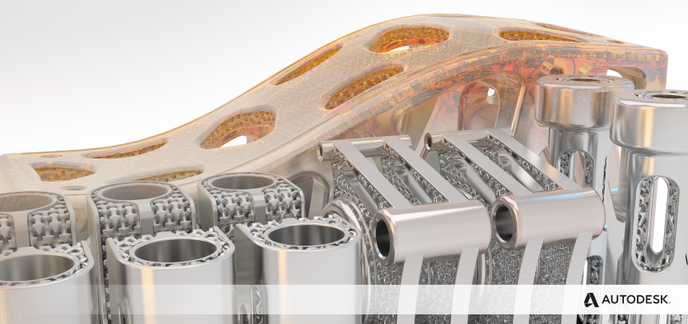
Introduction
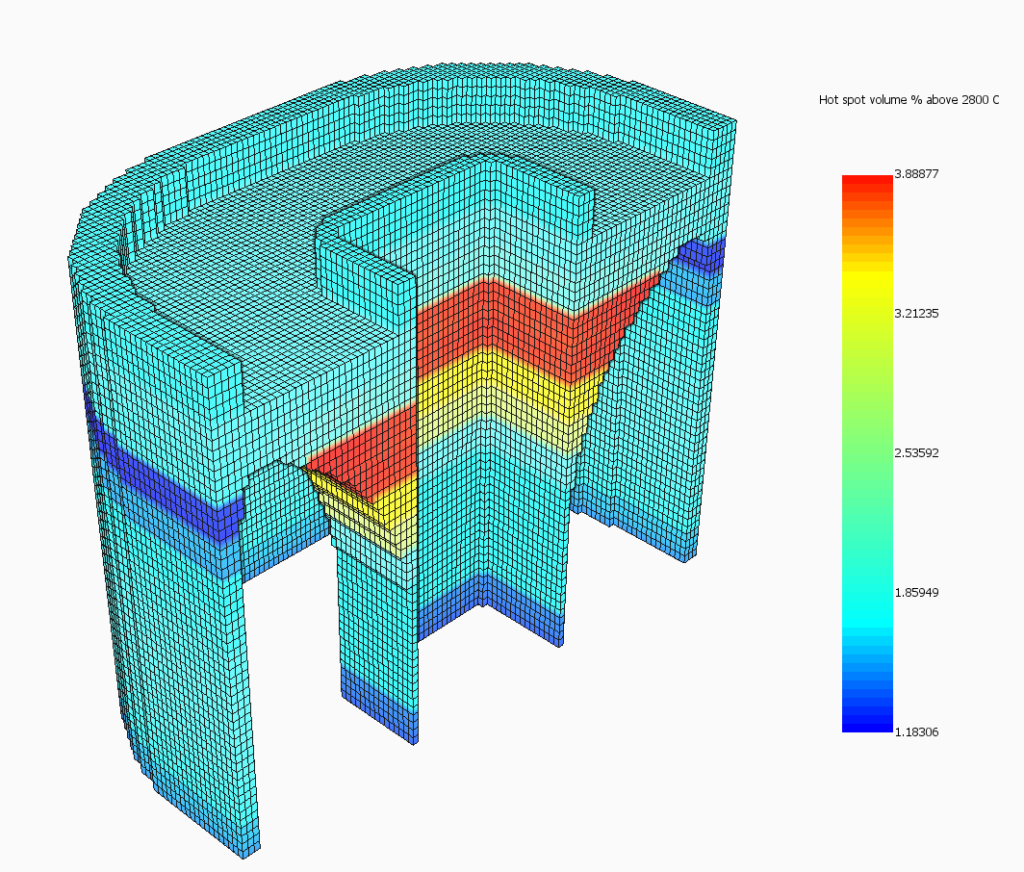
Interlayer Temperature, Lack of Fusion, and Hotspot results yield global results which can indicate to a user poor processing conditions, a lack or excess of build plate heating, or even point to a poor orientation in regions of extreme heat build up during Laser Powder Bed Fusion manufacturing. Like part scale distortion, the key processing parameters are input at the small-scale PRM generation level. Particular to these global thermal results are the thermal inputs: Lack of Fusion temperatures, Hotspot temperatures, and Interlayer Temperatures. This article serves as a guide to the proper selection of these values to guide more useful simulations.
Lack of Fusion Temperatures
Lack of Fusion Temperatures are the easiest of the thermal analysis values to set. Lack of Fusion indicates the material did not fully melt, leaving unsintered powder where solidification was expected. Physically the material did not exceed the Liquidus temperature. This is the key value that should be set for Lack of Fusion. Users may also want to know if the material has at least begun the melting process, in which case they should also include the Solidus temperature for the material being simulated. Finally, advanced users may want to use the Lack of Fusion tool to investigate other effects that occur at known temperatures, for instance to see how much of a Ti-6Al-4V build plate crosses the alpha-beta transus temperature. There is negligible computational cost to compute the results at additional temperatures, so numerous values may be studied without slowing down the small or part scale simulations.
Hotspot Temperatures
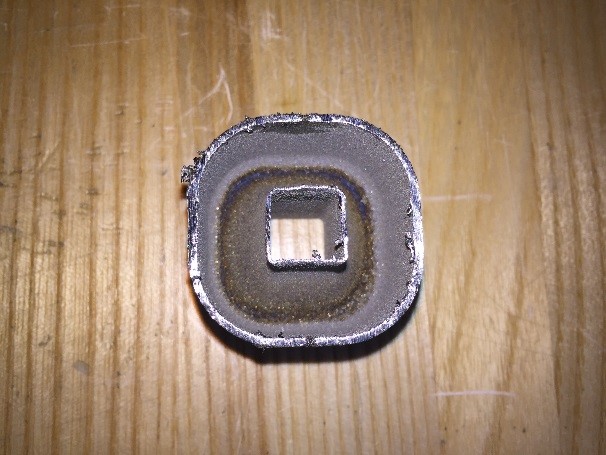
Hotspot temperatures are less intuitive to set than Lack of Fusion. A hotspot temperature is some threshold value beyond which undesirable outcomes are known to occur. At the extreme case, users can input the material’s boiling point to understand if the part is going to experience extreme overheating. However, material degradation typically occurs at much lower temperatures than the vaporization point. Like Lack of Fusion Temperatures, any number of Hotspot temperatures may be set without incurring a computational cost, so users may interrogate a large number of potential trouble temperatures, and then hone in upon the temperatures of concern by correlating with parts exhibiting burn lines. If experimental work is not yet available to guide setting these values, set hot spot temperatures around 50% above the solidus temperature.
Interlayer Temperatures
For the purposes of Netfabb Simulation, an Interlayer Temperature is the temperature of the deposited material and build plate after a layer has been completed, the next layer’s powder has been spread, and the recoater has returned to its position. This is the coldest point of the simulation. It also is the initial condition for the simulation of the next layer or group of layers. When setting the Interlayer Temperatures at the PRM generation level users need to input at least two values: room temperature and a higher temperature value. Typically, the higher temperature value is set at half of the melting point. However, users may want to use either experimentally derived or simulated interlayer temperatures to determine a better approximate maximum operating temperature to use for the higher temperature value. At the small scale simulation, at each Interlayer temperature Lack of Fusion and Hotspot volume fractions are calculated. During part scale simulation, the Interlayer Temperature results drive the predictions of Lack of Fusion and Hotspot volume percentages. For temperatures in between the Interlayer Temperatures selected at the PRM level, linear interpolation is used.
Unlike Hotspot and Lack of Fusion Temperatures, each Interlayer Temperature incurs a computational cost during the small-scale PRM generation stage. For each Interlayer Temperature a multilayer simulation is completed. Thus, it is wise to minimize the number of Interlayer temps used for any PRM generation. However, this instinct must be tempered with the need to accurately model the material’s temperature dependent behavior. This requires an assessment of how linear the thermal properties are between the chose Interlayer Temperatures.