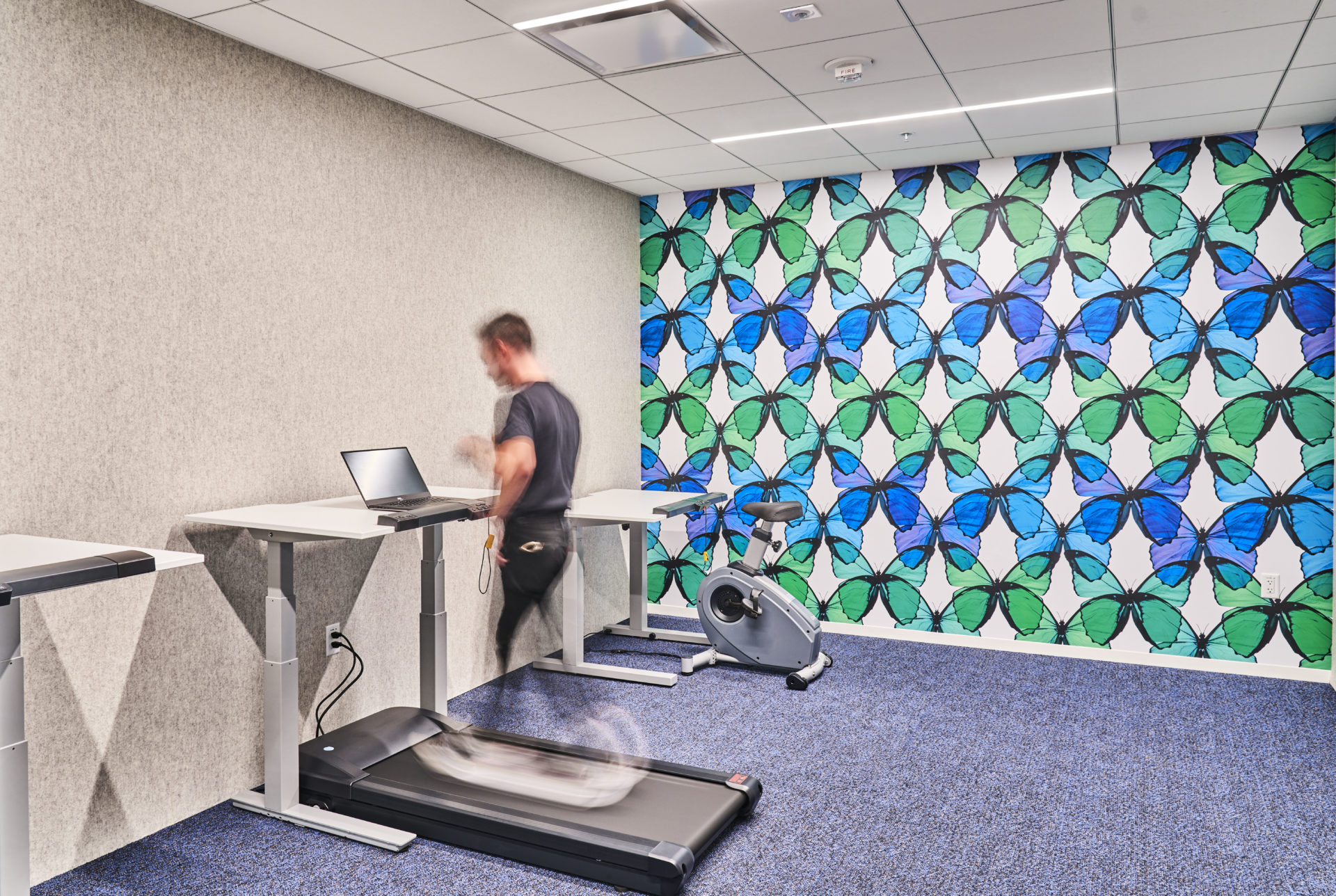
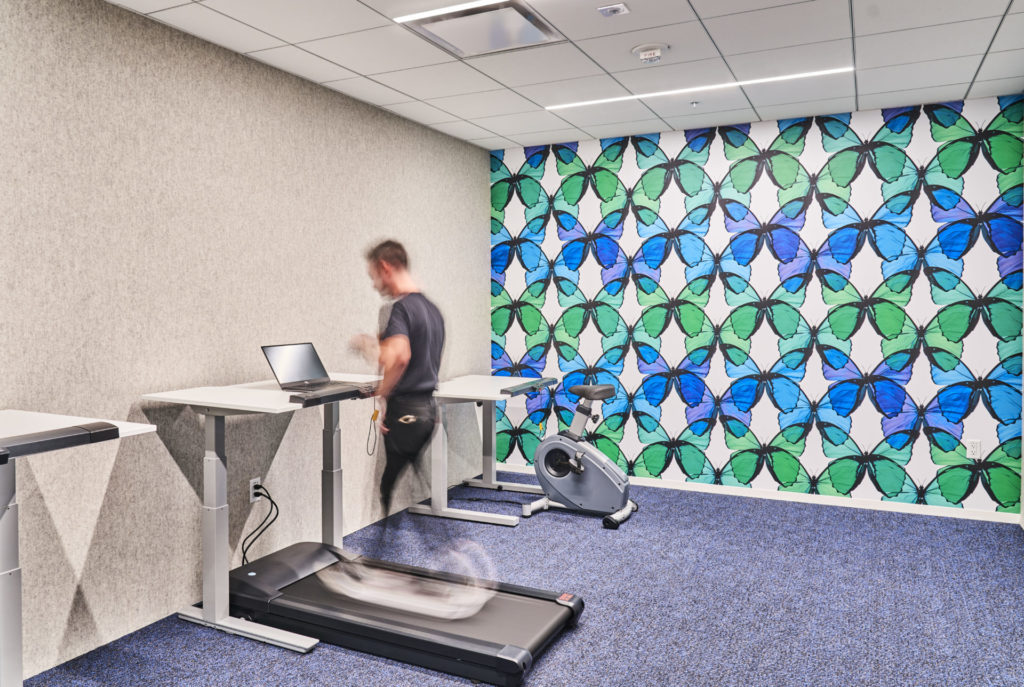
Autodesk Global Consulting Delivery (GCD) have recently worked with a company that designs and manufactures high-quality custom inner soles, for the footwear industry. The manufacturer was looking to grow their current annual output of orthotics and worked with GCD to create an automated process to achieve this.
Historically, like many of its competitors, this manufacturer started out making orthotics using a process of pouring plaster into foam boxes, applying corrections, and creating high-quality, custom-made devices from those casts. Over the years they have moved to digital processes in an iterative way, each time obtaining new efficiency gains.
The manufacturer’s main challenge now is finding the most efficient way of maintaining that same high-quality and reliable production whilst producing such a high volume of custom orders. To cope with this demand, in collaboration with GCD, they have now moved their production to Autodesk Fusion 360 with PowerMill to enable the automated design and manufacture of these individualized inserts.
Process automation improves quality and saves time
Orders are received through an ERP system and automatically added to a production database. For each order, an operator scans a foam box imprint of the patient’s feet using integrated 3D scanning technology. The scan data is then imported into a custom application created by the GCD team. This application integrates Autodesk Meshmixer to allow the operator to remove any unwanted ‘noise’ to make the scan data easier to work with.
The operator configures various options based on clinical appraisal and prescription, such as the shoe profile, orthotic thickness, and any additional support areas. The automation software then evaluates the foot scan and in addition to the configured options is able to determine the parameters of the orthotic required.
This information is then passed to Autodesk Fusion 360, where a fully parameterized surface model is updated and automatically exported to PowerMill for toolpath processing. Updating these model parameters and adapting the orthotic surface for each new order negates the need for complex CAD modeling to be completed manually from scratch every time. This has resulted in more than a 90% reduction in operator time needed to process each order compared with the first digital modeling system employed by the manufacturer.
Using optimized toolpath templates, PowerMill is then utilized to automatically calculate toolpaths and output NC code to the shop floor where each machine can manufacture multiple orders in one go, thus maximizing the machine utilization.
Zero wait time reduces time to market
Using Fusion and PowerMill together enables groups of designs to be processed and toolpaths to be calculated simultaneously, resulting in zero wait time on the shop floor. The collation of designs and NC files ensures that the correct NC file is delivered to the machine for each order every time, meaning that the incorrect orthotic cannot be sent to the wrong patient.
Automating the process using Autodesk Fusion 360 with PowerMill has turned a complex modeling and toolpath programming workflow into an easily repeatable, scalable data entry process without losing focus on the need to customize each orthotic to the individual patient. The custom application has reduced training times for new operators, enabling the manufacturer to scale operations to a second facility and increase the production of accurate, high-quality orthotics in a timescale that meets their customers’ expectations.
For more information on how Autodesk’s Global Consulting Delivery team can help you with your manufacturing problems contact your Autodesk Account Team.
Add comment
Connect with: Log in
There are no comments