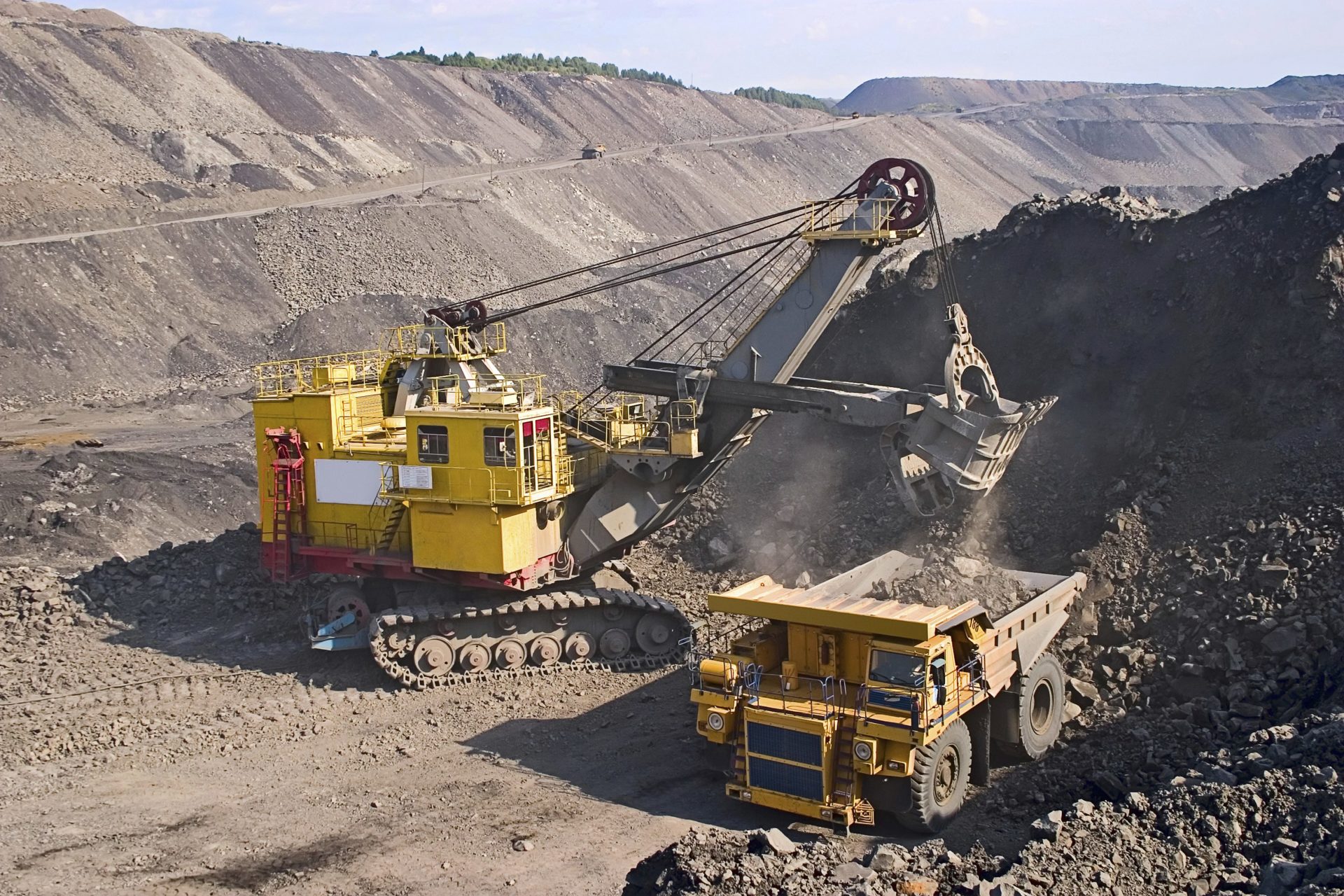
A mining industry manufacturer with locations in many countries specializes in the production of spare parts for material handling. These parts are associated with mining vehicle spares, as well as very large mixing machines. Due to the use of all kinds of rock, these working materials suffer and need to be replaced at regular intervals. The manufacturer saw an opportunity to reduce their time to produce spares by using optical scanning and reverse engineering.
Delays in replacement parts can have a significant impact on profits
The extraction of mining materials is a very abrasive and dirty process. This leads to a high wear rate of the components used in vehicles and machines. As a result, the mining industry needs to constantly replace parts and procure spare parts. This can be a costly and time-consuming process. If a spare part is not available, any downtime can have a significant financial impact on the company and projects.
For one manufacturer, the process of creating spare parts previously required several different applications. Although this process was successful, it was time and work-intensive and required extensive user training. Switching between the different applications caused problems with data transfer during export and import, which further slowed down the creation of spare parts. The use of different software providers is costly and time-consuming in terms of procurement, installation, and licensing.
Process development with Autodesk Consulting
The manufacturer turned to Autodesk’s Global Consulting Delivery (GCD) team for help. After understanding the process and the required outcomes, the consulting team developed a process using only Autodesk software packages Autodesk ReCap and Autodesk Fusion 360 with PowerShape. With these applications, it was possible to reverse engineer parts of all sizes. The reverse engineering department was able to reduce the time needed for the work and improve the accuracy of the final geometry to a level of +/- 2 mm for a complete truck body and truck lining elements. The process and applications were easily able to handle data files in excess of 1.7 GB, and with significantly fewer products involved, the time spent importing/exporting and translating data between different products was eliminated.
The process that was developed imports directly from the scanner into ReCap to simplify the process of capturing the data. The user can view the captured data and decide whether to capture additional data or remove areas where excess data has occurred. Autodesk Fusion 360 with PowerShape is then used to convert the scan data into CAD using PowerShape’s reverse engineering and modeling capabilities. Finally, PowerShape’s model deviation calculation feature could be used to simplify the quality assurance process of checking the created CAD data against the scan data from hours to minutes.
Autodesk’s GCD team is able to partner with the manufacturer for training on this new process and helped the manufacturer in the early use of the new tools to ensure a successful implementation. The future plan is for the process to be rolled out across the manufacturer’s global operations.
For more information on how Autodesk’s Global Consulting Delivery team can help you with your manufacturing problems contact your Autodesk Account Team.
Add comment
Connect with: Log in
There are no comments