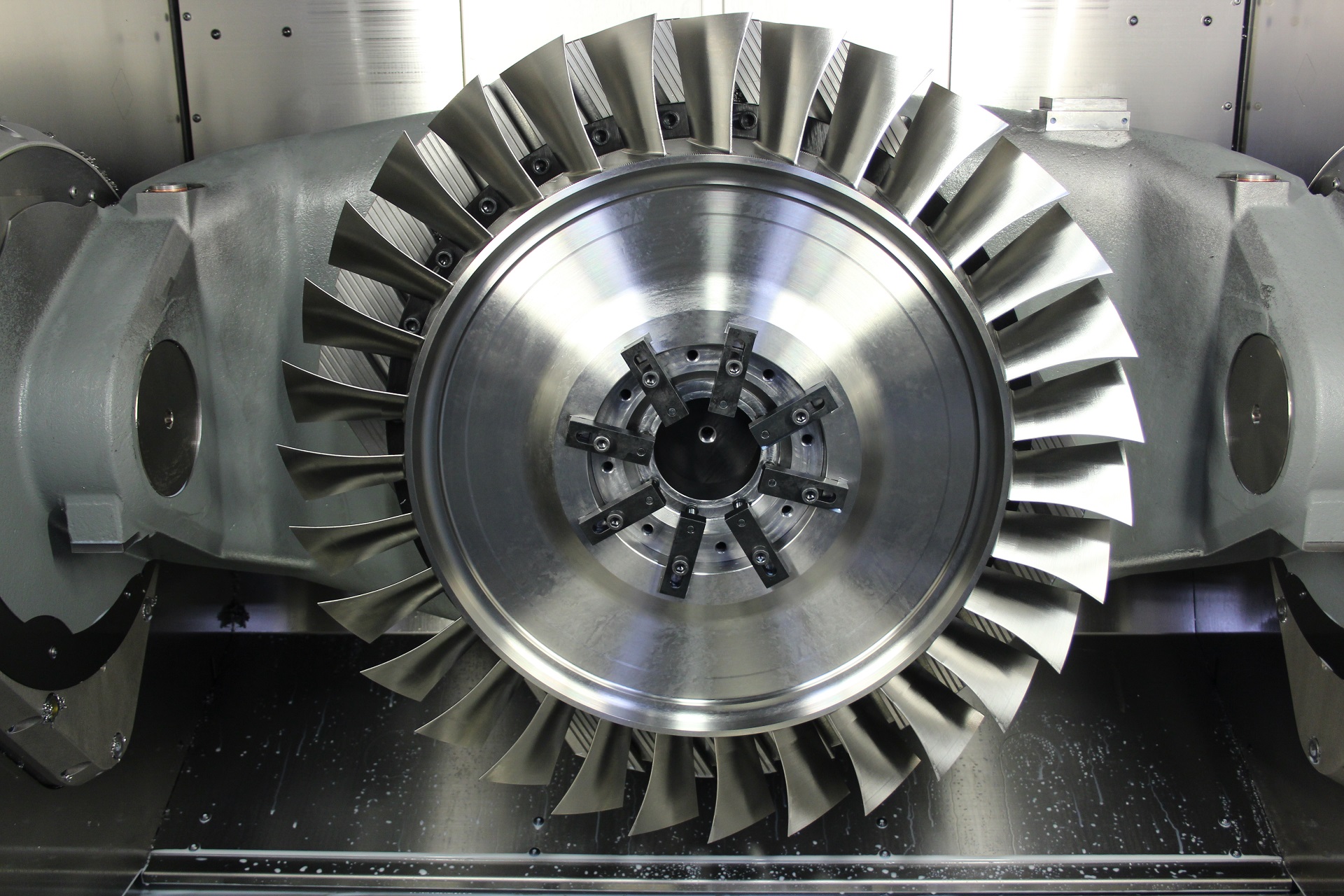
The word ‘Blisk’ is a portmanteau of ‘Bladed Disk’. It is a single piece component comprised of a ring of aerofoil blades arranged around a central hub where the Blisk generates rotational motion from the force of air blowing through an aeroengine. Blisks have traditionally only been found on military aeroengines, for example the low-pressure combustion stages of the EJ200 Euro Fighter and the F35 Lighting II – Joint Strike Fighter due to manufacturing complexity and associated costs.
Toolpath optimisations to increase customer productivity
Advancements in CAM and increasingly capable machine tools have enabled Blisk technology to become more readily available for use in commercial aeroengines.
Autodesk’s Global Consulting Delivery (GCD) team were contracted by an aerospace manufacturing company to deliver process development improvements on their Blisk production. The customer’s objective was simple; cut costs by reducing machining cycle time. The constraint was that customer did not wish for the cutting tool suite to be changed, especially for finishing.
The reason for this is that aerospace components and their defined manufacturing processes are tightly controlled; any changes must go through lengthy validation processes. Maintaining cutter consistency prevents this revalidation being required and thus the process improvements could be implemented immediately.
Given the constraints imposed, the overall benefit was limited . However, even with these limitations, by using powerful machining strategies within Fusion 360 with PowerMill the customers machining cycle time was reduced by 40% and the project goals successfully met. During the project close-out review the GCD team wondered what could be achieved without any such limitations; how far could the software and hardware be pushed and how much could the machining cycle times be reduced?
Beyond limits
Case Study Details
- 800mm Diameter Blisk
- Material Ti-64
- 31 Blades: 120mm high, 84mm chord length
- Solid pre-turned Billet
- Baseline cycle time at Autodesk facility: 135 hours
- Current cutter cost: £2,200
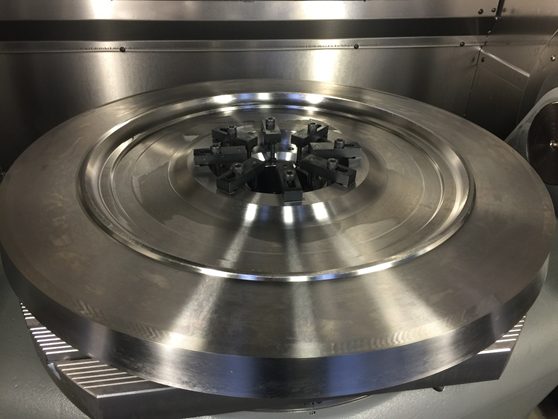
GCD’s intent was to make a huge reduction in machining cycle time. To achieve this all aspects of the machining process were considered; not only the cutting strategy but also the machine tool, fixturing, cutters and cutter holders too.
Blisk aerofoil toolpaths usually consist of many shallow roughing, semi-finishing and finishing passes utilizing ball nosed cutters. This presents a few challenges. Aerofoils are typically tall and thin and so they move and vibrate during the machining cycle which causes problems. In particular, the motion of and load on the cutter is constantly changing. This results in a constant push/pull effect on the material and aerofoil being machined. These unpredictable forces result in either inconsistent material conditions or machining marks being left on the aerofoil surface. The toolpath combination and approach used was completely different from the conventional approach which would traditionally comprise of many shallow but fast cutting passes and be limited to Ball cutter types. This approach was modified to use a slotting operation to cut out each aerofoil profile removing the maximum amount of material in as little time as possible to produce a near-net shape. Barrel type roughing and finishing cutters were then used to finish the part. The Barrel form enables a greater stepover to be achieved and cycle times to be reduced. Typically these cutter types can be difficult to program and control due to a combination of the large radius cutter form and desire to minimize the tool-axis motion whilst avoiding holder collisions with the part. PowerMill’s dedicated Blade, Blisk and Impeller (BBI) tool axis control and smoothing algorithms coupled with automatic collision avoidance and verification made the programming experience faster and easier with few iterations and minimal post-calculation editing required.
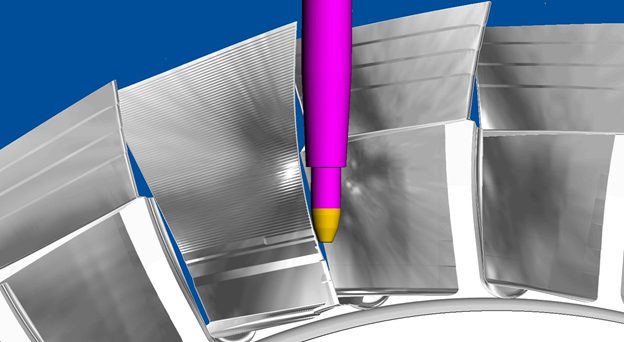
Key to the success of the machining strategy was availability and range of equipment available in-house at Autodesk’s UK technology centre, where access to a multi axis CNC machine commonly used in aerospace was available for process development.
Also vital to the success was GCD’s strategic partnership with a specialist cutting tool company whose speciality is designing and manufacturing cutters to extremely tight tolerances and making them for each specific process. They produced the exact size, shape, and tolerance cutters required including the cutter holders and provided the expertise to hone the cutting parameters for the process.
These optimized cutters enabled the toolpath strategies to be fully optimized, maximizing the cutting speeds, feeds, depths and widths of cut and machine tool power and stability characteristics. Titanium is a very expensive material and Blisks require huge investment in time and machinery to produce, making them highly valuable items and expensive to produce. To ensure close control over the part quality, measurements were performed in-process throughout the machining cycle using Fusion 360 with PowerINSPECT. On Machine Verification (OMV) is a process of using a touch trigger probe in the machine spindle to take measurements of the component. Measuring the Blisk on the machine tool in this way verified the correct amount of material removal, as well as ensuring that the aerofoils were stable and not deforming. This provided validation and assurance that these expensive parts would be accurate and correct once the machining cycle was finished. Final inspection was performed in Autodesk’s UK technology centre quality control department using a Coordinate Measuring Machine (CMM) and 3D optical scanning equipment.
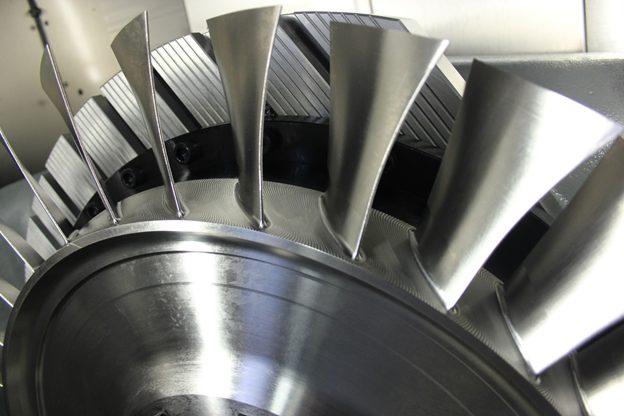
Case Study Completion Details
- Cutter Cost: £1,217
- Total Cutters used: 18
- Tolerance Achieved: ~0.01mm
- Cycle time achieved: 35 hours
Savings in summary
The total saving on cycle time was 135 hours reduced to 35 hours, equating to a 74% saving. Incredibly the tooling cost was also reduced by 45%. All this would empower the manufacturer to change the way they see these products and potentially disrupt their product portfolio.
For more information on how Autodesk’s Global Consulting Delivery team can help you with your manufacturing problems contact your Autodesk Account Team.