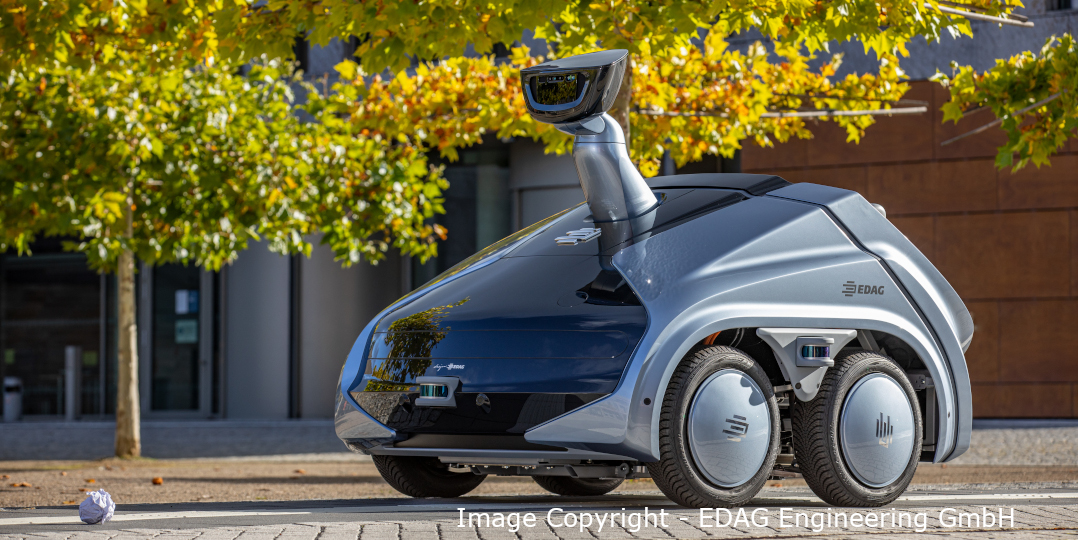
EDAG Group is one of the world’s largest independent development partners to the automotive and aviation industries. They have over 50 years’ experience in vehicle, production plant and electrics/electronics development.
A versatile, modular, configurable platform
At present, EDAG Group is working on a holistic mobility concept called EDAG CityBot. This concept is based around a multi-functional, fully autonomous robotic vehicle with swarm intelligence, which is completely emission-free. Due to its modularity and multi-functionality, the EDAG CityBot can be operated around the clock and, according to requirements, configured as a passenger cell, cargo carrier, city cleaning device and for many other usages by fitting add-on modules.
EDAG Group is involved in all phases of automotive product development and was looking for a step change in the reduction of development time with conventional methods. A possible limitation they identified for this is that there can be still disconnected workflows between design, simulation, preparation and manufacturing. Also, many manual steps could be required in traditional product development as well as multiple design iterations which can both increase the development cost. Additionally, the customization of specific parts towards changing usage conditions can be a very slow and expensive process with conventional methods.
To enable this step change, EDAG Group teamed up with Autodesk’s Global Consulting Delivery team to create a concept called “Closed Loop Engineering process” which connects an agile, automated and continuous development process using captured data to create a EDAG CityBot digital twin environment and flexible production process. The “Closed Loop Engineering process” is a product development process where information from the development, production and especially usage are tracked, captured and connected within a digital twin environment.
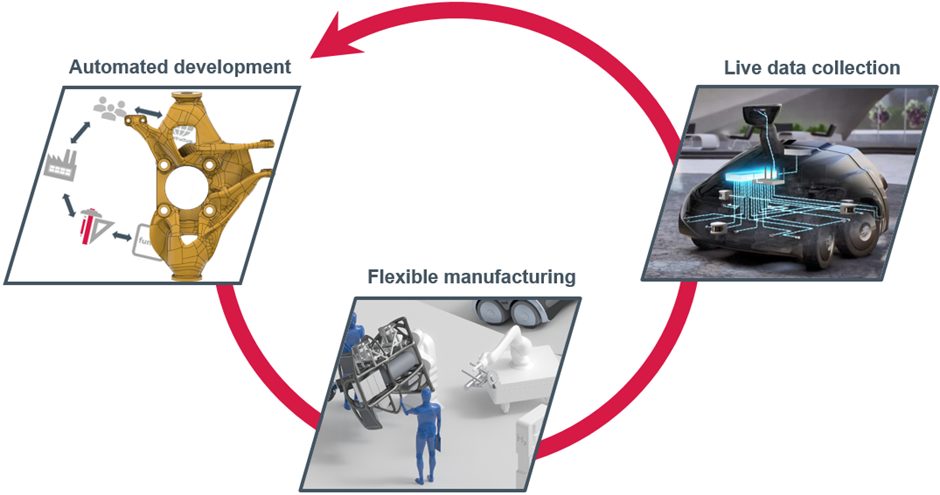
The system is initially configured with the data for the first design of the part. When the part is in operation, additional data such as number of accelerations and forces applied to the part will be tracked and this information will be used to optimize or change the next iterations of the part. The process is also able to capture changing operating conditions and create parts which suit a specific usage. For example, parts from the chassis could be stronger for an EDAG CityBot which is used to tow planes on an airfield compared with a part which is used in public transport.
Together with the EDAG Engineers this concept process was then verified on a selected part from the EDAG CityBot as an example. The part selected was the “Wheel mount” which connects the wheel with the steering and chassis. Multiple possible designs were created using Generative Design each addressing a different combination of preselected materials and manufacturing methods.
Bringing the process together
This process was achieved using Autodesk’s Fusion 360 platform, which connects design, simulation, generative design, manufacturing preparation all within one tool. Later this data can then be connected to other systems as all the data is centrally managed through Autodesk’s Forge technology.
With this concept process the EDAG Group aims to reduce manual steps within product development process though automation and reduce design iterations and development costs. Additionally, the project will be used to showcase EDAG Group`s capabilities in supporting their customers in the automotive development of the future.
By collecting new data for the updated parts or EDAG CityBots, the cycle is closed, and the automated process starts again. This allows EDAG CityBots to continuously adapt to changing mobility needs and requirements. Like living creatures in nature, technical products can now also continuously develop further – a technical evolution is achieved.
Sebastian Flügel, Project Manager EDAG Group
For more information on how Autodesk’s Global Consulting Delivery team can help you with your manufacturing problems contact your Autodesk Account Team.