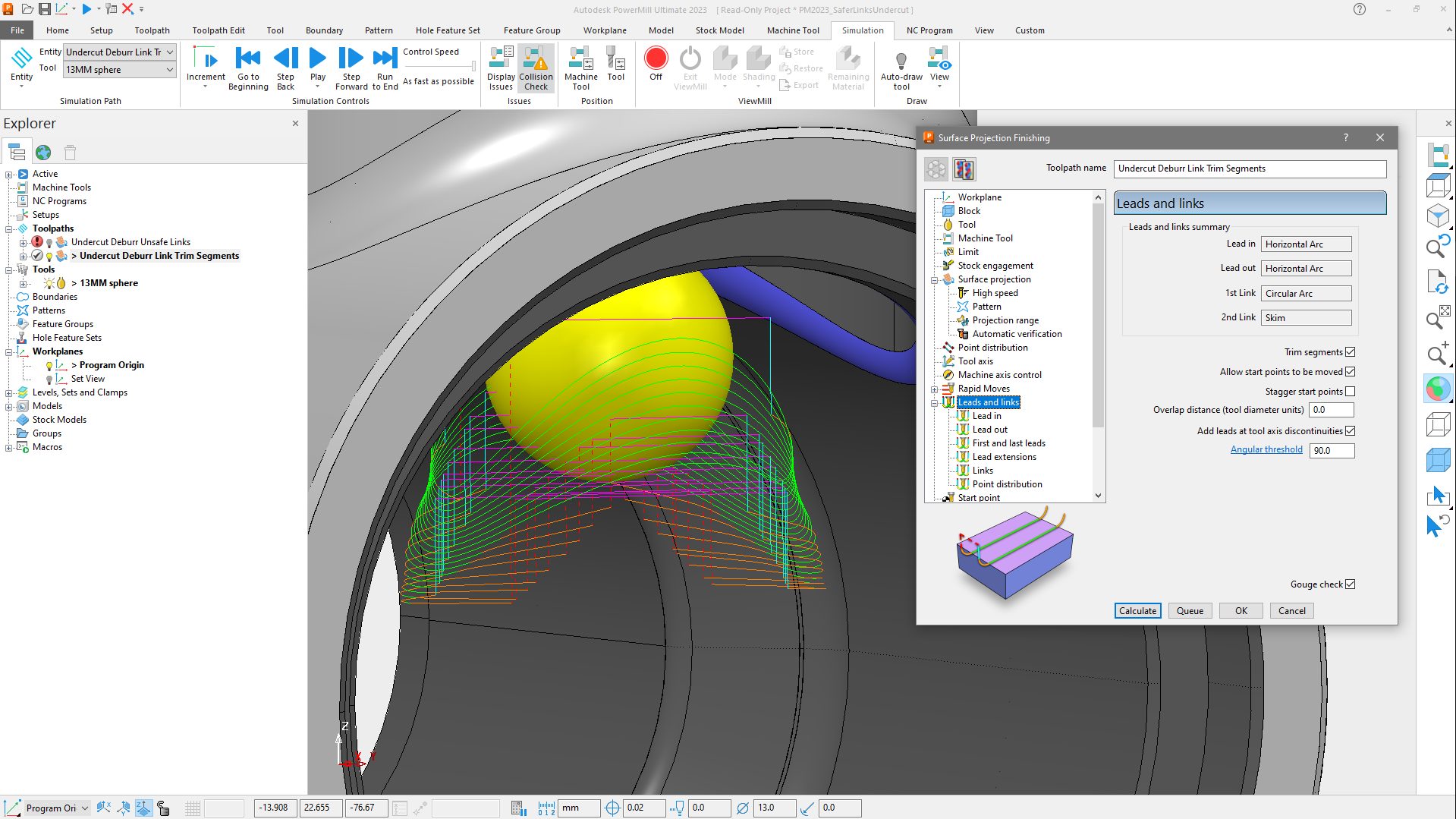
Workforce availability is reduced, lead times are getting ever harder to meet, and you need to make the most out of every minute worked. Fusion 360 with PowerMill (version 2023) delivers here with simpler automated workflows, decreased calculation times, and increased safety.
PowerMill 2023.0 – Customer Release: May 11, 2022
In this blog, we will provide a brief overview of the major release highlights and links to more detailed tutorial videos (for those of you wanting to see the improvements in action).
Calculation speed improvements
Never being satisfied, the Autodesk PowerMill development team continues to look for opportunities to optimize algorithms and calculation processes creating yet again more speed improvements. The chart below shows 4 new areas that have benefited from a speed improvement. Some commonly used commands see very large gains, such as a 61% increase when creating spun profiles and a 33% calculation time increase when using Curve Projection Finishing. Even seemingly small increases though can become large time savings when we start thinking about their use over a period of days, weeks, months, and years. When we start to add all these individual speed increases together large time savings and productivity gains are to be had.
To learn more about these speed improvements, watch this tutorial video
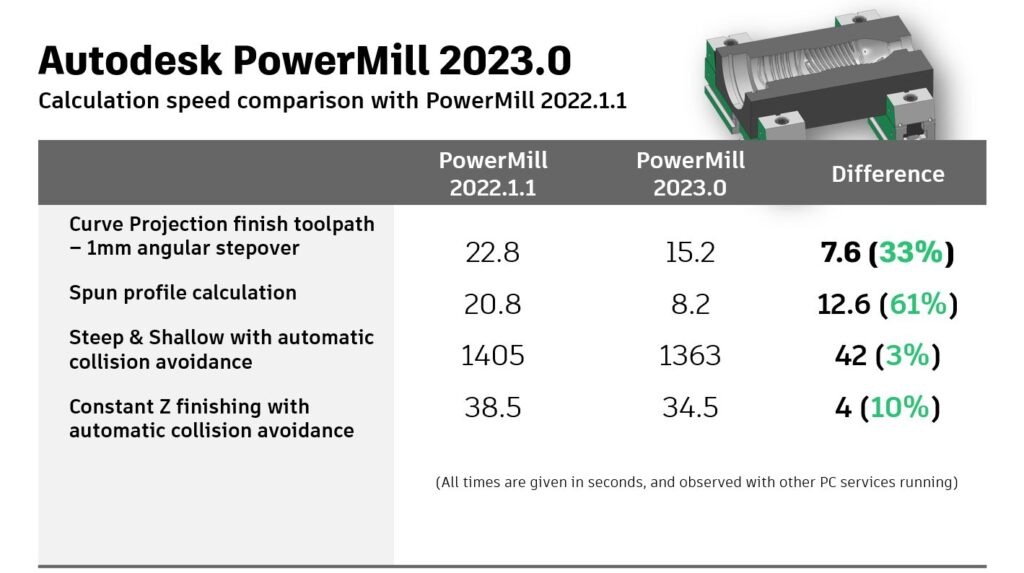
Steep and Shallow improvements
Not all geometry is created equal, different areas may benefit from being machined in different ways affecting the quality of the surface finish. Along with this, how and where we enter an area to be machined can have a direct effect on the tool wear. A new option to Optimize Open Pockets in the Steep and Shallow machining strategy is now available when using a 3D offset type for shallow regions. This gives greater flexibility to how these areas are automatically machined.
You may not be aware that Steep and Shallow is a hybrid toolpath combining two machining strategies into one toolpath. Part geometry is automatically isolated into steep and shallow regions using a configurable threshold angle. PowerMill applies the most appropriate machining strategy to each of these different regions then combines them into one toolpath, reorders the segments into a safe machining sequence, and then applies gouge-checked linking moves. For many applications, Steep and Shallow can provide a “done in one” toolpath capable of machining the entire part quickly, efficiently, and to a high level of surface finish.
When using the 3D offset type in the shallow areas, a closed offset shape is produced based on the surrounding steep region. This new option to optimize open regions looks further at the geometry and if possible, generates open offsets aiming to enter and exit the material from the outside in. These open passes tend to have fewer changes in direction, reducing the likelihood of dwell marks being left on the part, which can degrade the surface finish. The new option can additionally minimize the likelihood of full-width cuts appearing, which leads to better tool life and lower consumable costs.
To learn more about how to use this new feature, watch this tutorial video
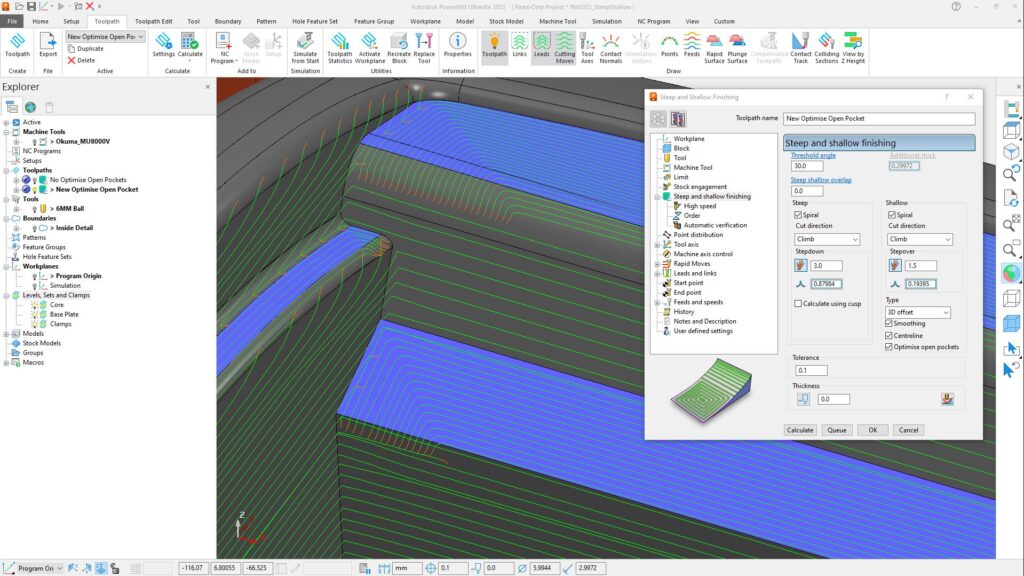
Enhanced machining setups
A lot of parts need more than one operation to be completely manufactured. This requires the creation multiple machining setups which can increase the complexity of CAM programming, resulting in longer programming times and increased risk of human error. While machining setups are not new to PowerMill, this latest release sees some major enhancements that improve overall usability; more intuitive workplane behavior, and new/improved default settings that can be configured for each separate setup.
The first enhancement to workplane behavior makes working with setups more predictable as workplanes are automatically activated and displayed when required, reducing the number of settings that need to be managed and helping to prevent mistakes from occurring. An example here can be seen when producing a NC program based on a setup. PowerMill 2023 now automatically copies the setup workplane into the NC Program output dialog, ensuring the two settings match, and reducing the possibility that NC code is output using an incorrect datum.
The second enhancement sees the addition of two new settings which can be applied to individual setups, these being the machine tool and location of the part relative to the machine. This makes jumping between machines and simulating toolpaths much easier as when a setup is activated the corresponding machine is automatically activated as well.
Last, but definitely not least, is the addition of default thickness settings. Just like setups, the use of thickness settings is not a completely new feature, but PowerMill 2023 now allows individual thickness parameters to be defined for each individual setup increasing flexibility further. If a setup is active and a toolpath is created, the new toolpath will inherit the thickness settings defined for the setup – again reducing the number of parameters that need to be managed by the CAM programmer, creating a simpler and safer workflow.
To learn more about how to use these new features, watch this tutorial video
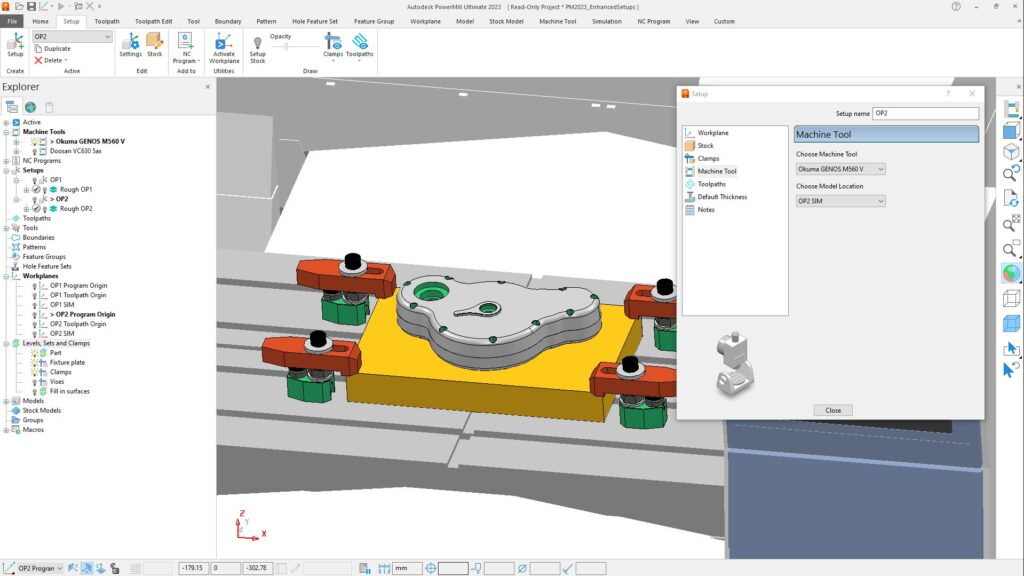
Safer leads and links (automatic toolpath trimming)
There are times, when programming parts, where the tool just does not have enough room to lead in or out of the material as needed. In these cases, we are left experimenting with different lead options or using toolpath editing to trim away toolpath segments to create the additional room to allow the tool lead in/out moves. As time clicks by and we start pulling out our hair, we dream of a check box that would just make everything good again. Well, that dream is now a reality with the introduction of a new Trim Segments option in the toolpath leads and links form.
These enhancements really come into their own in a number of common scenarios. Firstly, when creating a toolpath that machines one region but needs to avoid machining neighboring geometry. Secondly, when machining parts with undercuts and where the tool needs to safely enter into and exit from the stock without colliding with the overhanging geometry. Prior to this release of PowerMill, the toolpath segment would be calculated to the point where the tool finishes machining the chosen area and is almost touching the neighboring model. Crucially PowerMill wouldn’t create the necessary space to add a lead to the segment end without it gouging the part. As all toolpaths in PowerMill are gouge checked, the only option would be to apply a vertical plunge move-in to, and a vertical retraction out of the stock. In some materials this may be acceptable, in others it may be a catastrophe.
When applied to a toolpath, the new Trim Segments option allows PowerMill to automatically use a systematic process of evaluating other lead and link options, then trims the toolpath segment ends to create the additional space to apply safe leads to the toolpath, saving you the time and effort.
To learn more about how to use this new feature, watch this tutorial video
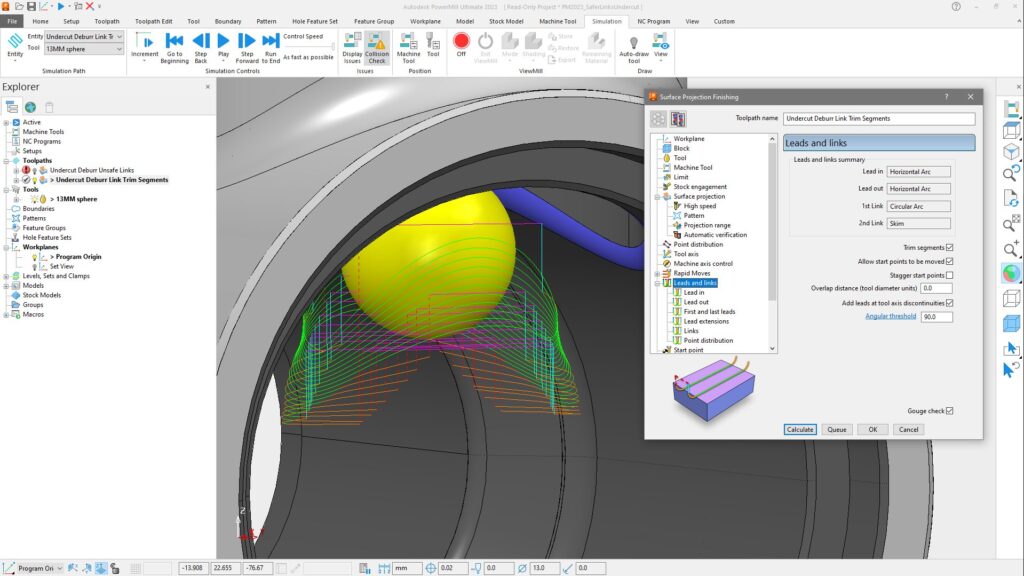
Additional, notable enhancements
While we have just covered our favorite 4 new updates in the 2023 release there are quite a few others that deserve a mention.
- Improved consistency of toolaxis tilting when using automatic collision avoidance
- Typed in commands for automatic selection of inclined planar faces for 3+2 machining
- Improved accuracy of new rest finishing strategy (preview in PowerMill 2022.1)
- Additive toolpaths can now be appended with same layer-bands grouped together
- Writing hole features to XML now includes “Depth_type” and “Level” properties
- Improved Flex licensing to avoid charging users for periods of inactivity
- Spiral Offset Slice Area Clearance now machines open flat areas “outside-in”
- New parameter functions to reset toolpath safety status
- Better quality Corner Finishing toolpaths
- Improved Spun Profile accuracy
- New in-product Autodesk branding
Want to learn more?
So, there it is. The top improvements in Fusion 360 with PowerMill (version 2023) with a list of honorable mentions. There are more improvements, and you can read about them all in the official release notes at https://help.autodesk.com/view/PWRM/2023/ENU/
If you want to take a deeper dive into this release, why not watch this 32min release highlights presentation.
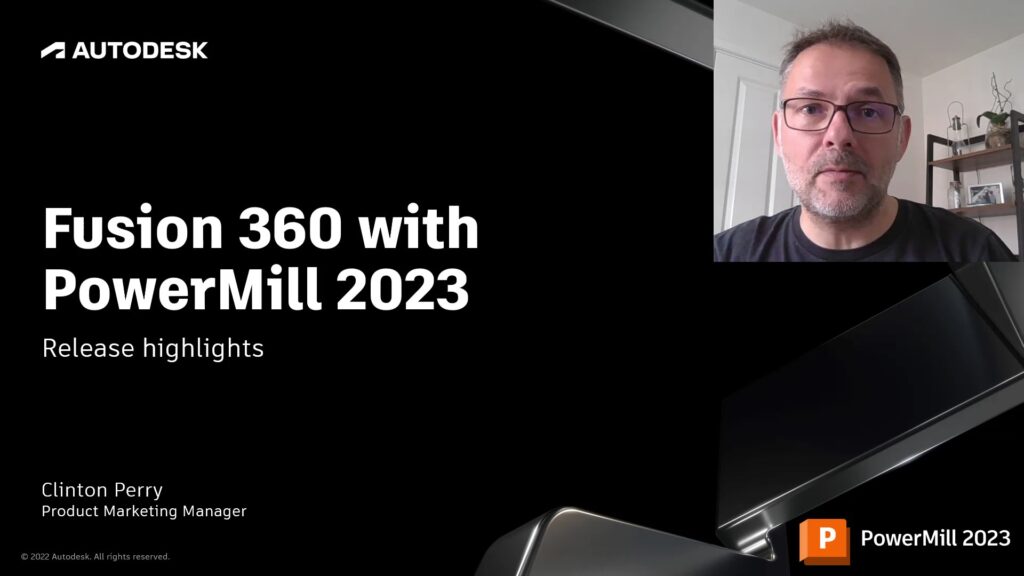
Ready to download this latest version (2023)?
Fusion 360 with PowerMill 2023 will be released to customers starting May 11, 2022.
Eligible customers with an active subscription or maintenance agreement will be able to download the latest release starting May 11, 2022. Customers can download using the Autodesk Desktop App or by logging into their Autodesk Account. Alternatively, visit our Services Marketplace to contact your local Autodesk team and discuss your specific business needs.
NEW TO FUSION 360 WITH POWERMILL? WHY NOT TRY A FREE EVALUATION.
New to PowerMill and want to see how it can help you solve your toughest CNC machining challenges? Contact our team of manufacturing specialists at www.autodesk.com/powermill-evaluation to learn more. Submit your contact details and our team will contact you to discuss how Autodesk can help your business to be more successful.
Add comment
Connect with: Log in
There are no comments