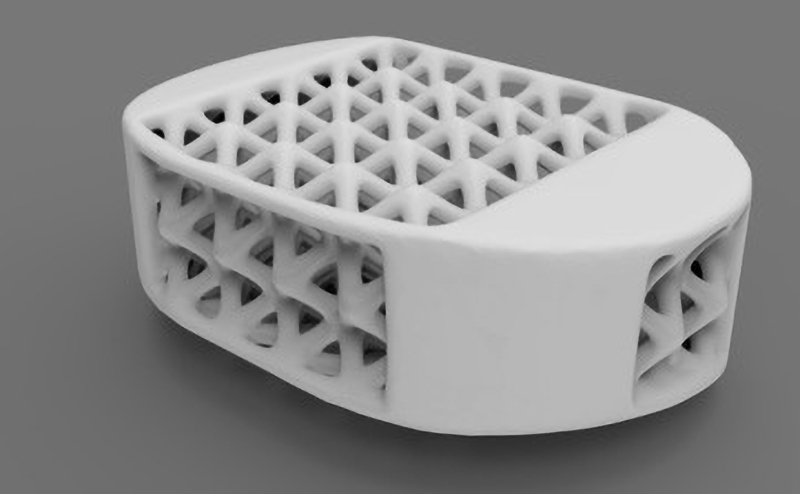
Meotec GmbH is a medical technology company based in Aachen, Germany, focusing on magnesium implant technology. Meotec also gained expertise in surface treatments of metal implant materials. To generate porous oxide ceramic layers on these implants, Meotec optimized a surface modification technique using plasma electrolytic oxidation (PEO). Applied to magnesium alloy components, it forms the basis for innovative implants that are gradually resorbed by the human body and replaced by endogenous tissue. Due to the oxide ceramic surface, the degradation process of the biomaterial is controllable, and the probability of negative tissue responses is minimized. Meotec is one of the first companies worldwide that provides safe magnesium-based implants including all its benefits for the healing process.
Challenge
In a new research project dealing with implants for spinal surgery, Meotec developed a fully-resorbable magnesium-based interbody fusion cage. The innovative idea of the cage is based on the degradation and tissue growth stimulating behaviour of magnesium. It guarantees the mechanical stability during the spinal fusion process and promotes formation of new bone due to its strut structure. After completion of the fusion process, the implant is fully absorbed by the human body leaving no residues within the spine area. In order to produce such bone substitute implants, several technologies, such as turning or milling, are commonly used. If a structure is too complex (e.g., porous or strut structures), additive manufacturing becomes the technique of choice.
Porous structures show several advantages regarding implant-ingrowth, associated interlocking effects as well as the formation of new tissue. Additionally, the porosity directly benefits the mechanical properties of the implant. When choosing optimized geometrical parameters, an additively manufactured implant can reach a bone-like behaviour. To date, only a few companies in the world are working with magnesium alloys in additive manufacturing, due to the very complex safety precautions this highly reactive material requires. Meotec is a pioneer in pushing 3D-printed magnesium parts to the market and offering manufacturing as a service in this field. However, additive manufacturing requires precise digital planning prior to printing.
Solution
The unique interior-structured design of the cage was realized with the help of Autodesk® Netfabb®. Netfabb® has great advantages in design of lattices and structures with hollow spaces. In order to realize a certain structure, multiple ways to reach the final design are always offered by the assistance function of the software. For example, it can be optimized for mechanical properties automatically or build exactly to your geometrical conception with different tools by hand. Emerging questions concerning the program utilities were easily answered by specialists of Autodesk® and in video tutorials all Netfabb® basics were explained. A helpful tool for the implant design was the Lattice Commander where a basic unit cell structure can be adjusted individually, and completely new strut-based parts can be built up.
“With Netfabb we have the opportunity to additively manufacture complex scaffold structures made of the critical material Magnesium by being able to tailor all necessary input parameters for a successful job” Max Müther, production manager says.
Outlook
Meotec will soon push the new device into the market to allow the treatment of patients that may otherwise suffer from adverse long-term effects caused by durable implants. Thomas Derra, research and development engineer from Meotec, expects degradable magnesium implants to gain significant importance on the future global market. Additive manufacturing and its associated software such as Netfabb® will support this trend with almost endless design options.