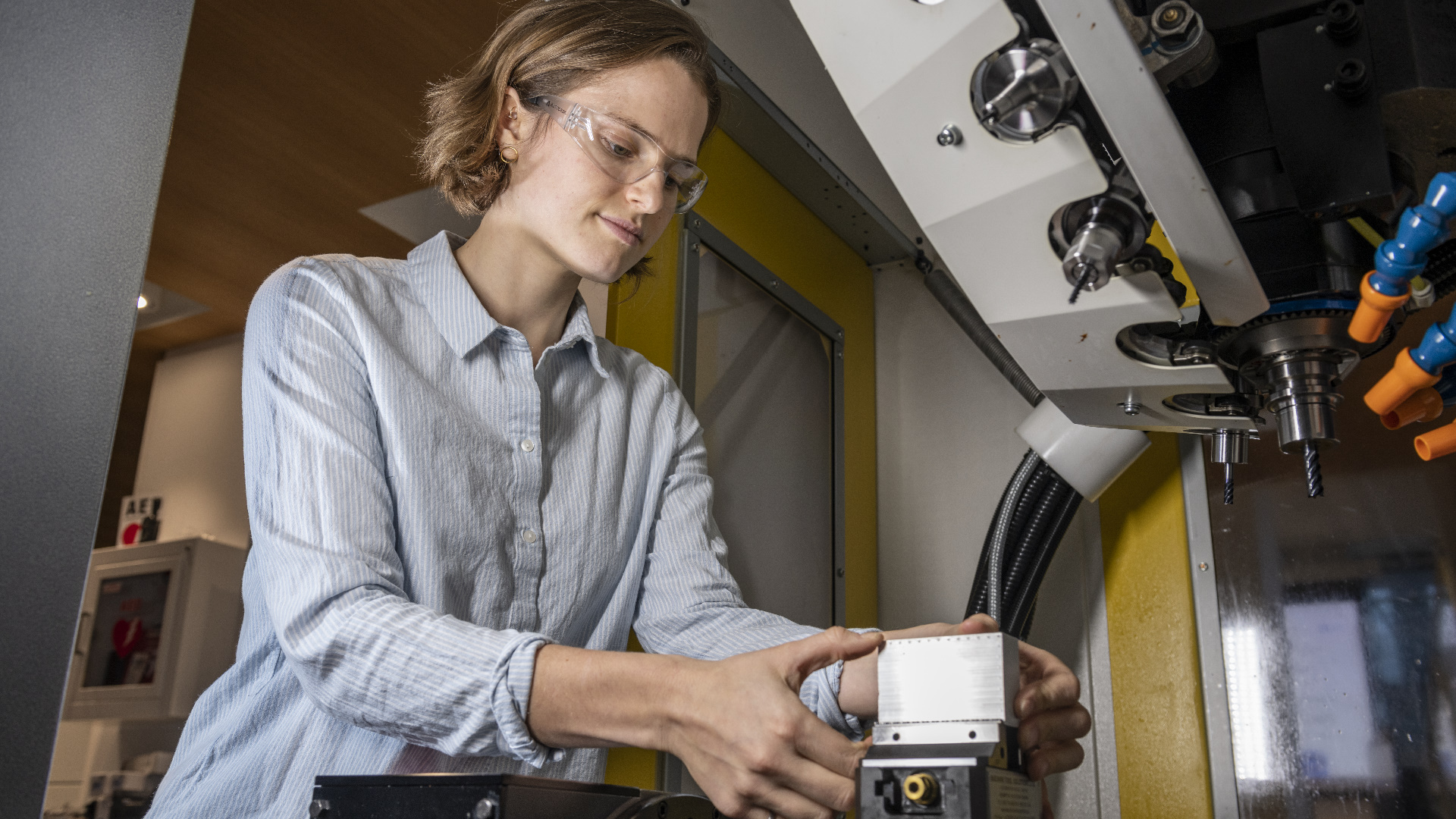
A dental manufacturer creates dental restorations and has recently partnered with Autodesk’s Global Consulting Delivery team to change the way they manufacturer these devices.
The manufacturer receives hundreds of orders each day from dentists for abutments. Each one is unique in design and must be made from the right material with the correct interface to the implant used for the patient.
Previously the process of manufacture had a lot of manual steps. Firstly, the orders had to be downloaded from the ERP system. A programmer was then responsible for opening the abutment design model and preparing it for manufacture. Once prepared, the design was transferred to the CAM system for toolpath calculation and NC output.
On the shop floor, each machine operator ran 2 machines each. A busy workload of ensuring that the correct blank material was loaded into the machine, selecting the correct NC program to run, and ensuring tooling was changed at the correct times often resulted in a lot of wasted machine idle time as the operators moved from one machine to the other with production stopped completely during break periods.
The manufacturer and Autodesk (in association with other partners) updated this system to be completely automated. The ERP system now exports orders as they arrive and passes them to the Autodesk Manufacturing Automation Utility (a tool used by Autodesk’s Global Consulting Delivery team for automating machine tool operations). This tool interacts with Fusion 360 with PowerMill to prepare the CAD, calculate toolpaths, and output milling NC code as well as Fusion 360 with PowerInspect to create probe paths and probing NC all individual to each part.
A shop floor automation system interacts with two robots and four multi-axis milling machines for automated part loading. The Manufacturing Automation Utility holds an inventory of blank material available to be machined and matches it up with the calculated orders. The Utility commands the robot to select a particular blank and load it into the machine before automatically loading and executing the correct NC file for the job. Having completed milling, the part is automatically inspected to ensure the part has been machined correctly. Any failures are handled by automatically switching to backup tooling and re-machining. Successfully machined parts are unloaded into an unload tray and the order number is programmed into an RFID chip embedded in the part’s holder to aid part identification.
The first time anyone from the manufacturer handles the order in any way is when the part is unloaded from the machining cell and manually checked before being shipped.
Since moving to the automated solution, the manufacturer has eliminated manual errors in programming and part loading by enabling the system to verify the material being used to machine each part. They have been able to reduce the number of machines all whilst increasing their throughput! They achieved this by reducing the idle time to almost zero through robotic part handling and Autodesk’s consultants reduced their machining times through improved part programming. The improved toolpath strategies and on-machine part inspection have all but eliminated hand finishing of parts. All these improvements mean the manufacturer can ensure they meet their target of sending out orders as soon as possible after receiving them.
For more information on how Autodesk’s Global Consulting Delivery team can help you with your manufacturing problems contact your Autodesk Account Team.