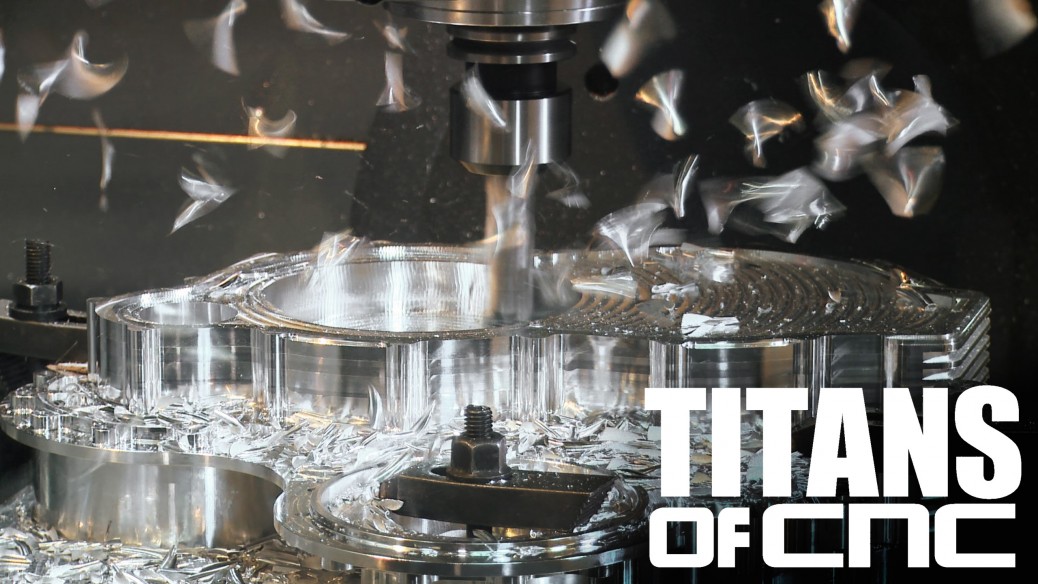
Adaptive clearing sets the stage for elite efficiency—but CNC artistry seals the deal
Pushing CNC machine speeds to the limit delivers huge benefits for any shop. Faster speeds cut your customer’s product costs and help the shop finish more jobs with better margins. Win-win.
But cranking up tool speed is not as straightforward as it sounds. In Titan Gilroy’s HSM shop, where speeds consistently outstrip conventional expectations, the first piece of advice newcomers get is to step back and slow down.
“There is an art to high-speed CNC machining,” Titan says. “You can’t just push a tool faster no matter what. You have to understand all the variables.” Two of the most important are rigidity in the work piece and the rigidity of the tool in the spindle.
“Vibration can be an instant stumbling block, causing good machinists to pull back instead of push forward,” Titan says. “The cure for vibration is pressure. But you can’t increase the pressure without sufficient rigidity.”
Tool selection, and the speeds and feeds at which they run best, is another key to success in HSM. Advanced work-holding techniques help other variables, including rigidity, fall into place.
“For short-run aerospace parts where rigidity is everything, I use a TE-CO six-inch vice or a Royal Products Quick Grip Collet Chuck for a mill,” Titan says. “When dealing with high-production runs, I dig into my tool chest and pull out the Mitee-Bite clamps.”
Vision is another fundamental that must be mastered before achieving top speed. When elite machinists look at complicated parts, they automatically understand the relationships between all of the surfaces, pockets, corners, slots and crevices in its geometry.
“You have to be able to look at something complex and make it simple,” Titan says. “If you’re not there yet, technology can help. Adaptive clearing is a perfect example. It’s like a miracle.”
Adaptive clearing, is a capability within CAM software that aims to improve speed and extend cutter life. Essentially, it replaces traditional roughing passes, which take a light depth of cut to maintain high feed rates, with deeper cuts that maintain a constant radial load. Light step-overs and larger step-downs use the full flute of the cutter, reducing run time and eliminating load spikes that break tools.
In other words, the software doesn’t clear level by level regardless of the part’s design. It “sees” the ideal 3D cutter-path and adapts accordingly.
“With a few clicks, you can set the parameters for the part and have the tools clear out a huge amount of material from all levels in seconds,” Titan says. “Before, you had to go through each pocket on each level, one by one. With adaptive clearing, the software understands the entire part and creates cutter-paths that are simply brilliant. They make 3D as easy as 2D.”
Transitions are also very important in CNC machining. When engaging material at a high feed rate, you need to lead in from an angle slowly, increasing pressure as you go.
“If you are on a beach and wade into the water, the transition is gentle,” Titan says. “On the other hand, if you jump off the dock into the water you create a dramatic impact. You want that gentle transition. Approaching the material correctly maintains tool life and is another key to HSM.”
As you gain experience and confidence with adaptive clearing, machinists can start experimenting with different tools, using variations of flutes and coatings to improve the process even more.
If all of this sounds like a lot to consider before you start feeding more inches per minute, you’re right. And that’s the point.
“When you pursue the art of high speed machining, you have to be able to think about many variables all at the same time,” Titan says. “That’s the sign of an elite programmer’s mind. The good thing is technologies like adaptive clearing make it easier, so you can simplify your approach while you gain experience.”
Visit Titan’s web page here: Titans of CNC
For more information on Adaptive Roughing, visit Autodesk’s Titan Page