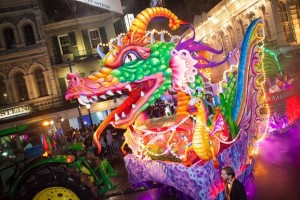
Anything is possible when it comes to ‘making’ Mardi-Gras, for this is one of the greatest celebrations in the party calendar. Mardi-Gras is undoubtedly one of the busiest times of the year for Kern Studios, a family-owned business who have ‘made’ over 450 parade floats this year alone. During the Carnival Season, no less than 70 parades in very different shapes and sizes take place. Deeply immersed in the unique Mardi-Gras culture, Kern Studios’ designs and builds 70% of all the floats on parade in New Orleans. But how do they create the magic?
Although many people think that Mardi-Gras consists of one big parade on a single day, Mardi-Gras itself (also known as Strove Tuesday) is actually the very last day of the whole Carnival season beginning January 6th.
In the early beginnings, Mardi-Gras floats were horse drawn wagon and carts, which began to appear in and around the mid-1800s. Over the years, horses were replaced with trucks and wagons with trailers, as bigger and bigger wagons were needed to accommodate the elaborate designs and their crews.
Today, communities express their pride and accomplishments, through floats with elaborate themed designs costing thousands of dollars and hundreds of man-hours to produce. In 2000, it was estimated that more than one billion dollars in spending was tied to Mardi-Gras.
In 2016, Kern Studios adopted a digital fabrication strategy for Mardi-Gras and purchased a KUKA KR 90 Robotic Milling Machine integrated and installed by Robotic Solutions Inc. to support their large scale sculpting process.
Also known as ‘Pixie’, the industrial robot cell has become a valuable addition to the creative process at Kern Studios, boasting a 6-axis arm and 60ft rotary table.
Although many assumed ‘Pixie’ had come to replace jobs, this couldn’t be further from the truth explains CEO of Kern Studios, Barry Kern –
“Robots can do many things, but it is neither creative nor aware of aesthetics. So there will always be a need for real-life artists, designer and programmers. As a matter of fact, adding this tool to our production process has not only expanded our production capacity, but has also created more positions in our company for programming, 3D modeling, and 3D scanning”.
During the day, CAD designers work using 3D plans to create toolpaths in Autodesk PowerMill for Pixie’s arm. Then they do a run-through simulation of those paths, watching out for incorrect collisions that could cause Pixie to damage the model. With every external axis and added permutation, Kern Studios trust the software to prevent collisions and produce the most efficient toolpath, especially on large parts that can be expensive and take a lot of time to create.
It’s overnight where the ‘magic’ begins; as employees’ clock out, they leave behind a block of foam, sometimes the size of a car. When they return in the morning, the foam has been carved perfectly into a full sized float, whether it be dragon or a clown.
Kern Studios, remain to be world leaders in float creation, and have been a part of Mardi-Gras history since 1932. Now with the adoption of digital technology, Kern Studios, will continue to deliver bigger and better on the magic showcased each year – ‘anything is possible’ when it comes to making Mardi-Gras.
For more information: search Autodesk/Make
Reference.
Kern Studios. Makers of Mardi-Gras.
Robotic Solutions Inc. Specializing in robotic milling and robot cell integration.
Autodesk. Build software that helps people make anything.
Image Credits.
www.kernstudios.com/custom-floats
Resource.