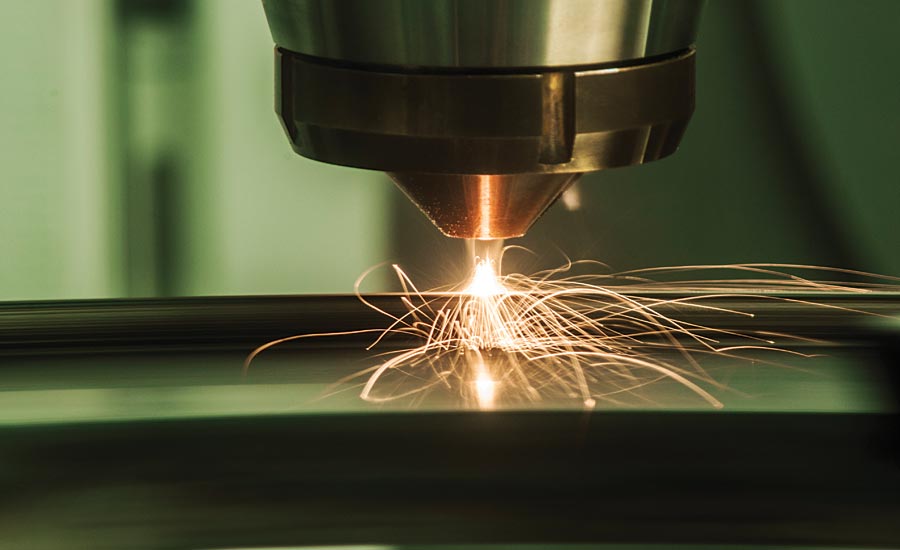
In 2017, over 4.1 billion passengers were carried by the world’s airlines and 10.2 million people work directly in the aviation industry worldwide. To meet the crucial climate targets that have been set, the industry must improve fleet efficiency. The manufacturing industry plays a crucial role in helping achieve targets, finding ways to build complex and robust parts, faster, cheaper and at reduced weights.
Additive Manufacturing (AM) is increasingly being used to build complex parts, waste less material and reduce the weight of parts. There are several types of AM as defined by ISO*. The two most commonly used for producing metal components in the aerospace industry are Power-Bed Fusion (PFB) and Directed Energy Deposition (DED). PFB is a powder-based AM practice where metal particles are fused together by the application of heat or electron beam to build a complicated and customized part.
Due to the technology’s higher rate, DED methods are typically used for manufacturing larger components that will subsequently be machined to achieve the final shape component.
BeAM is a global leader in the Directed Energy Deposition (DED) technology, who make AM machines for the aerospace, defense, and energy sectors.
Formed in 2012 in Strasbourg, with subsidiaries in Cincinnati and Singapore, BeAM is a French manufacturer of industrial metal additive manufacturing machines, which use the DED technology.
BeAM recently joined forces with AddUp, a leader in the design, production, and marketing of metal 3D printing machines and production lines, based in Clermont-Ferrand, a joint venture between Fives and Michelin.
Together BeAM and AddUp are uniquely positioned in the AM market to offer their customers a comprehensive range of metal additive manufacturing solutions, including, training, consulting, 3D printing systems and the making of parts for proof of concept (POC). The acquisition also strengthens AddUp’s role as a leading player in the French metal 3D printing ecosystem with more than 100 engineers working on the development of new solutions.
BeAM’s machines enable the additive manufacturing of highly complex metal parts, and having perfected its innovative repair of critical parts process, BeAM has registered its technology at the highest qualification level for the repair of aeronautical parts in turbines.
Every small improvement in aircraft design and build can have a large impact on fuel efficiency and ultimately the environment. Today’s aircraft use roughly 80% less fuel per passenger-mile than the first jets of the 1950s, a testimony to the tremendous impact of aerospace engineering and emerging technologies.
Using PowerMill Additive, BeAM are able to make complex parts that are closer to the finished size and shape, requiring a minimal amount of finishing processes such as machining.
For example, BeAM manufactured this 5.2kg gas turbine engine exhaust nozzle, additively manufactured on their Magic 800 from Inconel 625. The part was built to near net shape in 9 hours bringing with it the benefits of shorter lead times, lower costs and less material wastage when compared to traditional methods of machining-cast-forging-welding-etc.
Making parts faster will certainly help enable new design freedom to deliver greater fuel efficiencies and reduce the environmental impact.
The demand for more complex and robust parts, made faster, cheaper and at reduced weights requires a corresponding flexibility of process, meaning it is becoming more common to reconfigure production facilities, smart technologies, and upskill workforces. BeAM has a long-standing relationship with Autodesk and trusts its PowerMill Additive software as their solution of choice.
Click here for more information about PowerMill.