
Executive summary
- Implementing Autodesk Forma has helped the team at Continental Automotive to quickly create feasibility studies to streamline the planning of its factory sites and speed up the decision-making process.
- When planning sites to meet business needs, main priorities include avoiding risk of disrupting operations and anticipating future growth.
- Using the North Star masterplan to simulate a hypothetical development, scenarios are easily created in Forma and tested with a big picture view of the site to see if it meets the company’s needs. This complex process interweaves business requirements – particularly flexibility for expansion –alongside production demands, safety and security, sustainability goals, and employee wellbeing.
- Using Forma as a visual communication tool has improved clarity and collaboration during the process, both with internal and external stakeholders, helping save time and costs.
- All in all, it has been a time saver, helping the team reduce the time needed for planning sites from one week to one day.
Orchestrating the demands for the development of factories is an art in itself. Business targets, stakeholder management, legislation, time constraints, technical requirements, environmental goals – all challenges shared by most construction projects with one main difference: the risk of disrupting operations. That’s where new, user-friendly data-driven tools are helping manufacturing companies manage the complexity of their developments and meet their targets more efficiently. The need to future-proof the company’s factories led Daniel Zambori, Senior Project and Quality Manager Building Solutions at Continental Automotive, to adopting Autodesk Forma to reimagine the workflow for planning and developing its sites.
Continental Automotive is the electronics research, development and manufacturing group sector of Continental. Most cars on the roads contain Continental Automotive products such as brake-by-wire brake systems, cameras, radar sensors and lidars, high-performance computers, 5G telematics units, eHorizon, and autonomous driving solutions, just to name a few.
The company has a portfolio of approximately 55 locations, which is constantly evolving. “At Continental Automotive, our aim is to develop productive and adequate work environments. We focus on four key ambitions: sustainability, asset value, people orientation, and effective operations,” says Zambori who is based at the Frankfurt Automotive Headquarters in Germany.
“Using Forma enables us to create scenarios and feasibility studies very quickly to streamline the planning process.”
Daniel Zambori, Senior Project and Quality Manager Building Solutions at Continental Automotive
New sites to meet business demands
There’s a need to both find new sites and adapt existing ones to meet business requirements. “We are always looking to evolve our business according to automotive industry dynamics and develop worldwide. We currently operate in all major automotive markets, i.e., Europe, North America, and Asia,” says Zambori. Macro factors like infrastructure, transport routes, workforce, terrain, and climate determine the location of sites, and thereafter the exploration of their opportunities. This is an intensive process – for Zambori, one particular year involved 37 feasibility studies.
Alongside accommodating functional requirements, every site must be carefully planned to allow for growth and change. “We call this expandability: what is possible for the future? How can we expand in a way that makes most sense for our activities and ensures business continuity?” Zambori explains. The main risk to avoid in all cases is to disrupt operations, and hence business, creating added complexity to each project.
An accurate blueprint to anticipate growth
To map a clear plan that factors in all needs and foreseeable issues, the solution lies in what Zambori calls the ‘North Star’ concept. Created in Forma, it resembles a masterplan for a hypothetical development in phases. In the software, he can easily model the site in 3D with surrounding context, and analyze area metrics and orientation. “A great advantage with Forma is that we can pick up any land plot in any country, get basic info about it, and immediately start planning. We can visualize existing neighbors and roads, then start creating volumes and assigning them functions.”
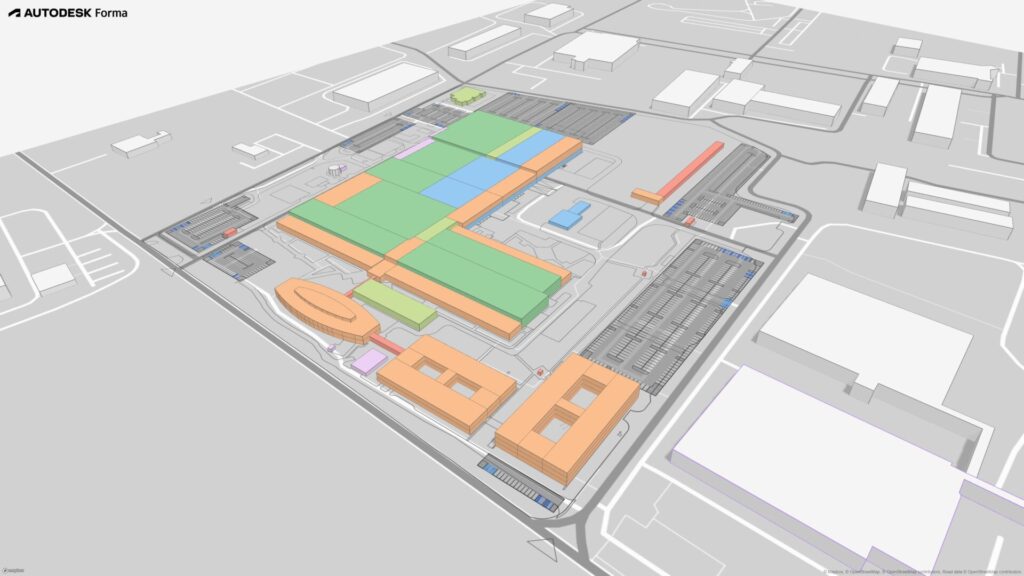
Scenarios are quickly created and tested in Forma to simulate how to best maintain flexibility over time. Evolving the workflow from mainly 2D to a 3D bird’s eye view of the project from day one has been a big step in the development process. “We recognised that in this early stage, we needed to focus less on the details which can change significantly,” explains Zambori. “With a big picture view of the site in Forma, we have a better understanding of whether a development will fit our needs. It’s very valuable to show decision-makers from the outset to create clarity to know where we are and where we want to go. At the same time, using Forma helps us optimize our developments as we are continuously improving our standard.”
“With a big picture view of the site in Forma, we have a better understanding of whether a development will fit our needs.”
Daniel Zambori
Quicker turnover
Planning ahead is vital for ensuring business continuity, as well as avoiding potential rework, budget blowouts, and delays in the face of tight deadlines. “We are always pressed for time when developing a site because it’s a complex process and we need to align with business needs. Our strategy is to front-load our projects by making feasibility checks from the start to know the possibilities of each location. Now we can do this faster thanks to Forma.”
Things move fast once a location is confirmed. “When checking feasibility, we must be able to quickly answer the question: what could we build there? Creating different scenarios in Forma, we can easily raise questions: are there enough offices? Is there too much parking? Are spaces getting enough daylight? Are the production areas and the warehouse properly expandable?” Importantly it’s about ensuring safety and security, and creating efficient flows for people, materials, and finished goods. Take, for example, how people move around the site: where do employees change into production clothing? How do they get to the employee restaurant for lunch? How can certain areas be fenced off for safety while visually creating a welcoming work environment?
“We can quickly create a feasibility report to present to decision makers and local authorities and show what can be done. This helps us make decisions faster, negotiate quickly, and already start planning our production.” All in all, it has been a big time saver.
“By using Forma to plan and develop our sites, we are now able to reduce one week of work into one day.”
Daniel Zambori

Planning with sustainability in mind
A wider perspective is also a must for reducing environmental impact. Guided by the UN Sustainable Development Goals, Continental Automotive aims for its new factories to achieve LEED Gold certification, which has already been secured for all major new developments, for example, in Lithuania, Hungary, Mexico, United States, Germany, and China. “What’s important is to not block the site for future expansion to avoid building something that needs to be demolished later, which creates business interruption and material waste,” says Zambori. “In Forma we explore, for instance, scenarios on how to connect various development stages or create transitional zones between an existing and new construction to avoid double or temporary measures like extra facades, oversized structures, and shifting functions.”
Energy-wise, the ambition is to both reduce energy consumption and generate renewable energy onsite – the target is minimum 10% – to supplement the already 100% green electricity currently used. “We are researching the potential for sites to generate their own solar energy, either on open space, roofs, or over car parking,” Zambori tells. “Using Forma’s solar energy analysis, we can plan and visualize the space needed for solar panels on the site and see areas with the best yield and areas to avoid. It needs proper planning so that we, for example, avoid creating a field of solar panels which must be demolished later to make space for expansion.”
Visual clarity improves dialogue with stakeholders
Like all construction projects, planning is a collaborative effort between different internal and external specialists. For Zambori, the main benefit since implementing Forma has been improving dialogue with stakeholders and getting them onboard. “There’s so much thinking that goes behind the planning and development of our factories,” he says. “Using Forma is the most efficient way for us to show colleagues how a new site works. It’s visual and so easy for everyone to read the 3D model and, therefore, understand the overall approach. The fact that we can quickly zoom in, see different perspectives, and review the numbers of various scenarios together has been hugely impactful. And we can easily export the information from Forma to include in our reports and presentations. This enables us to have more informed conversations and speed up the decision-making process.” External discussions are also happening in parallel, for example, with architects and consultants. Zambori: ”Using Forma, we have more clarity about the project when briefing them, which helps us find proper partners faster and streamlines the time and cost for those partners.”

Clarity extends to collaborating in a more cloud-based way which aligns with the business’s digital strategy. The projects and data can be easily accessed from one cloud-based hub and viewer access for any site can be shared with stakeholders .“Instead of working with different files and everyone making their own changes, we all see the same model that’s always up to date and is a single source of truth – this keeps everyone on the same page,” he continues.
Discovering new technologies is part and parcel of working in the dynamic automotive industry; having Forma as a new data-driven tool has been a huge boost for optimizing company’s development process to help keep the business on track. Zambori: “Looking forward, I’m excited to continue using a tool that’s continuously evolving according to users’ needs and feedback.” Besides designing successful factories, Zambori notes that there are other unexpected upsides to his work: “It’s rewarding to see how positively people react when we use Forma together in a meeting. It not only makes work more fun, but it really helps them to understand and embrace our vision for a project.”
All images courtesy of Continental Automotive.