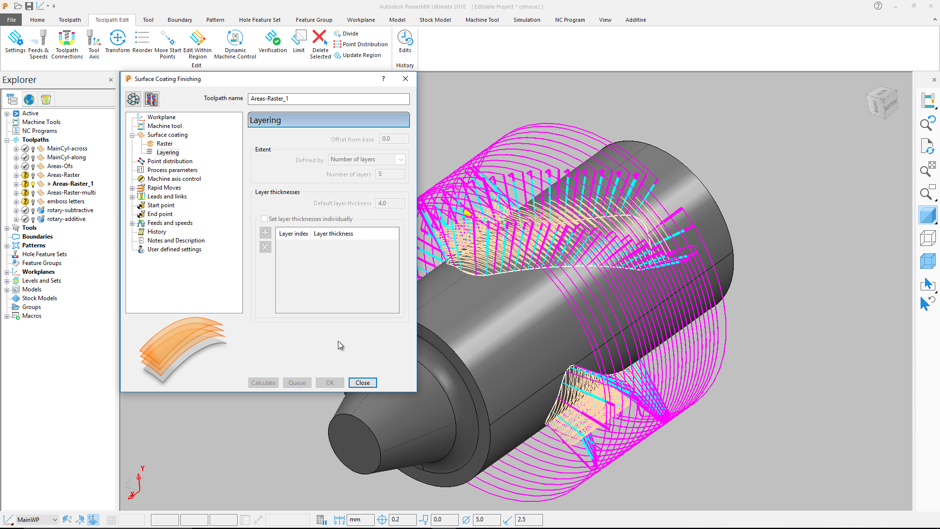
Article by Charles Jones, PowerMill Additive, Product Manager.
PowerMill 2019, the latest version of Autodesk’s expert CNC milling software, includes a whole new suite of solutions for high rate Additive Manufacturing.
Additive Manufacturing (AM) technology is still in its infancy, relative to established techniques such as milling, anyway. Like any infant, it is progressing at a dramatic rate. The image of AM as the 3D printing that goes on in a box in a corner is already out of date. Mainstream manufacturers like DMG Mori and Mazak are offering hybrid machines; equipment with both deposition (AM) and reductive (milling) capabilities. Autodesk PowerMill 2019 is designed to meet the growing demand for hybrid manufacturing.
PowerMill has been an expert CAM product for subtractive machining for decades and over the years it has developed into an advanced CAM solution, incorporating capabilities for 3-5 axis machinery as well as modules for robotics, all integrated within the same platform.
PowerMill 2019 is the first time that users will have access to the additive functionality as well.
Higher rate AM
PowerMill Additive is a collection of features and functionality that are aimed at higher-level AM.
PowerMill Additive is not about powder bed, or fiber deposition, or select laser sintering, it’s more about what is referred to as direct energy deposition (DED); wire-fed or powder-blown deposition of metal, at a much higher rate than powder bed or laser sintering, delivered on a CNC or robot platform.
Hybrid manufacturing aims to save money and minimize waste. It has attraction in the use of exotic materials in areas such as aerospace, for example. The typical ‘buy to fly’ ratio of milled billets of titanium is 9 or 9.5 to 1; this means that up to 95% of very expensive material goes to waste. AM uses far less material in arriving at the same part. It isn’t 1:1 but it’s a great deal better than current ratios, and makes these exotic materials more commercially attractive.
All in one
AM and reductive manufacturing used to be carried out on different machines, with all the wasted effort, additional floorspace, inconvenience and capital investment implied. The new wave of hybrid machines can do both. Two discrete processes are still involved but they are carried out on a single machine or platform. Once the AM part of the process has been completed, the operator removes the head and replaces it with a milling head.
These processes are designed to use as little material as possible. The machine will print a near-net shape; the reductive head will then undertake post-processing to get the finished components seen from more traditional processes. It sounds deceptively simple and it will, indeed, make life easier for machining operations.
Manufacturers will have access to the full range of Autodesk machine kinematics and simulation software that can see machine collisions and access limits, for both CNC and industrial robots. PowerMill has the capability to support up to 22-axis robots, which is well ahead of the current state of play.
Money-saving simulation
PowerMill 2019 also has access to NetFabb strategies for additive manufacturing and design, which has a very advanced simulation utility. It undertakes physics-based simulation of heat deposition, enabling the operator to see before the button is pressed and the commitment is made to expensive operations. It can help to reduce the number of iterations in prototype development, streamline workflows, reduce build errors and so provide benefits in time and cost, and bringing products to market faster. This functionality is also coupled with the ability to export tool paths to SUN for physics-based heat sim.
The complete package takes another step towards more unified workflows. The final step is unification and links to Fusion production, the real-time factory planning and monitoring software. As the CNC code is created, the jobs can be pushed out onto the shop-floor.
Parts can be built from scratch, or features added such as bosses, protrusions, rims and so on, to existing surfaces and bases. Functions such as rastering and center line each have their own controls. PowerMill provides very high levels of control across multiple elements and process parameters. These include power, material flow rate, feed rate and dealing with awkward local features.
Use case: The world’s first certified marine propeller
Autodesk has been involved with the production of the world’s first high rate 3D printed ship propeller, which was made by the Port of Rotterdam’s RAMLAB. This project is intended to help improve the efficiency of support to maritime services.
Making parts on demand traditionally has an incredibly long lead time, which means that huge warehouses full of components are required, most of which will never be used. That is clearly wasteful in space, personnel, and materials. High rate AM and post-process milling, carried out on hybrid machines with Autodesk PowerMill will not only enable more efficient use of material and less waste, it will help to free up capital in terms of inventory, as well as enabling suppliers to meet actual demand rather than having to plan for every eventuality in on-demand manufacturing.
Free trial
Autodesk is offering a free, 30-day trial of PowerMill Ultimate 2019. Those wishing to see how PowerMill can help transform their manufacturing processes can download the free trial, by visiting www.autodesk.com/powermill-free-trial
Learn more
To learn more about PowerMill visit www.autodesk.com/powermill
Are you a FeatureCAM user?
To learn more about FeatureCAM 2019 visit http://manufacturinglounge.com/autodesk-featurecam-2019-whats-new
Add comment
Connect with: Log in
There are no comments