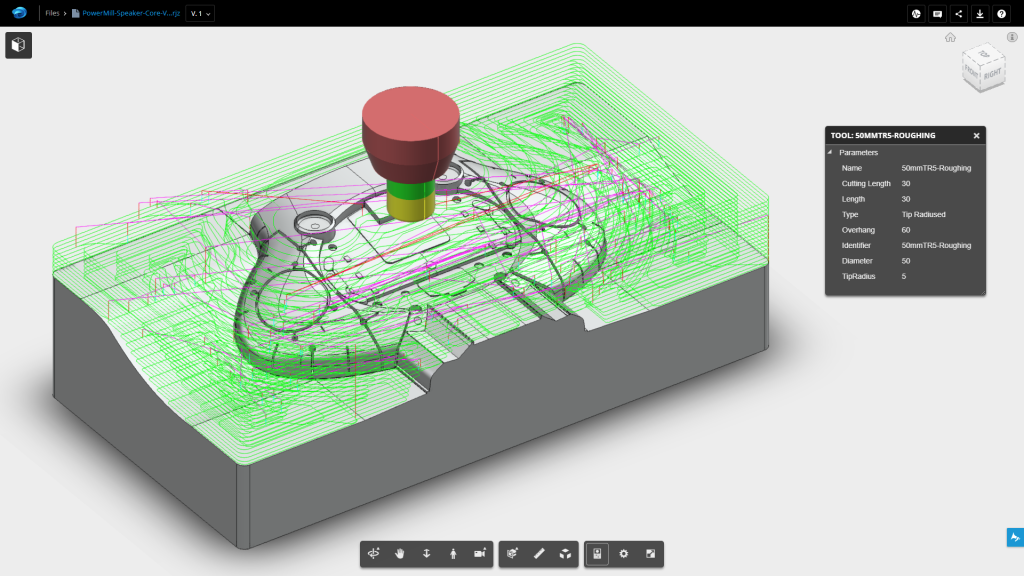
There’s no doubt that automation and robotics have made a huge difference to the world of manufacturing. Robotics make the whole process more efficient, less prone to error and can be used around the clock with little supervision. New technology such as Autodesk PowerMill Robot is going to open up the possibility of using robotics to more and more manufacturers, both large and small.
This article will take a look at some of the many advantages of using robots in manufacturing and how things are likely to evolve in the future.
A brief history of robotics in manufacturing
Numerically controlled machines were first pioneered in the 1950s, with George Devol inventing the first industrial robot that could automatically move objects a distance of 12 feet. From these humble beginnings, the 1960s saw companies such as General Motors taking an interest in and developing robotics in their plants.
In 1969, researchers at Stanford University created the first 6-axis articulated, all-electric industrial robot, which paved the way for an expansion in manufacturing automation throughout the 1970s and 1980s. Gradually, assembly lines have transformed from being manned by predominantly human workers to robots and machines with fewer human operators.
The last decade has seen the beginnings of the 4th industrial revolution, which has led to advances in robotics, including more collaborative and integrated robotic assembly and machine vision that has led to the automation of tasks such as welding.
The benefits of using robots in manufacturing
The main advantages of using robots are:
- Long-term cost savings – initial high cost is recouped by reduced staffing costs and overheads.
- Increased production quality – robots are more likely to build within tolerance and less prone to assembly error than humans, especially with repetitive, menial tasks. Sensors can be built in to the robots to ensure that parameters such as torque tolerances are reached.
- More efficient production – 24-hour working, sometimes in unlit factories. Robots are also faster and more precise than human workers.
- Improved safety – activities such as welding or handling heavy or toxic materials can be carried out by machines rather than risking injury to people.
Autodesk PowerMill Robot – robotic programming and simulation
Autodesk PowerMill Robot makes it easy for manufacturing businesses to programme robots, plan and optimize robotic actions, and create virtual simulations of automated manufacturing processes. The software platform is flexible, user-friendly and affordable.
The main benefits of using Autodesk PowerMill Robot are that it helps to conceptualize automated processes, provides validation for mechanical designs and helps to avoid expensive errors and bottlenecks in the system. It also helps to lower the cost of making changes to the product, as the simulation will highlight design or production issues. The whole process is less time-consuming than a hands-on equivalent, as process sequencing and system validation are automated.
At the moment, PowerMill Robot is ideal for manufacturing processes such as machining resin or foam, shaping wood and stone, trimming, finishing, deburring, grinding, laser or plasma cutting, and laser cladding. It features the ability to program tool path links and simulate tool changing, making it ideal for multiple machining tasks. The output is automatically translated into the robot’s native coding language.
As well as sophisticated programming and simulation features, the Autodesk PowerMill Robot is also capable of analysis and reporting of data such as axis limits and range. This data makes it easier to optimize the performance of the machines and to adapt the system to make it more efficient.
Once programmed, configured and optimized, you can save your preferred robotic system and automatically export it for use. Autodesk’s fully integrated system covers everything you need in one place.
The future of robots in manufacturing
Increased integration and collaboration are likely to be the main areas of innovation over the next few years. Autodesk PowerMill Robot is already pushing things in that direction, with fully integrated programming, simulation and analysis features that link directly to the robotic system.
The Internet of Things (IoT) and Artificial Intelligence (AI) such as machine learning will probably feature heavily in manufacturing, too. As sophisticated sensors and guidance systems are developed, robots will be able to adapt and self-correct their behavior, again creating more efficiencies and savings in the process.