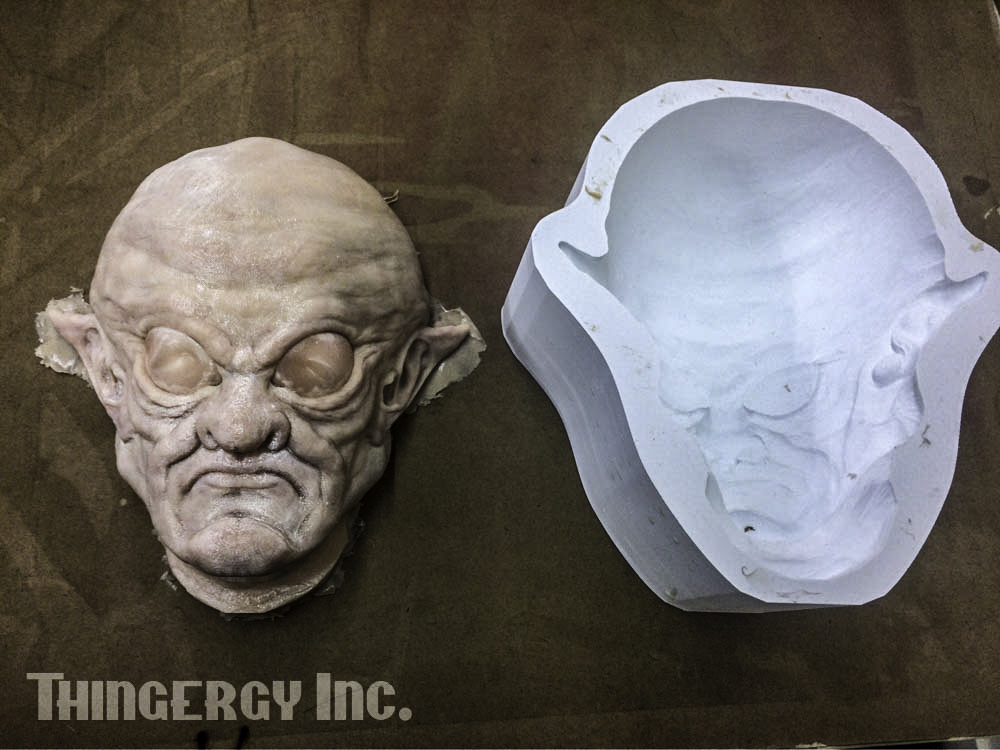
Frank Ippolito is a sculptor, creature creator, all-around maker, and founder of Thingergy Inc. “We make things,” he explains. “Anything from custom costumes and prosthetic makeup, all the way to full blown production sets for film, TV, and theme parks. We have built trophies, props for magicians, puppets, gorillas, robots, dragons, and even ten-foot tall statues of rappers.”
Ippolito is steeped in an industry that has long been innovative, but much of the work used to be done by hand. Thingergy still does a lot of work by hand. “Being able to create something traditionally is still important, but we need talented people who can operate and learn the software also. The transition from traditional techniques to more modern ones has done a lot for the company,” Ippolito says.
That’s why his company uses Fusion 360. Ippolito’s team uses the software to model 3D designs and generate CAM toolpaths for their CNC machines. “We use a router and plasma cutter on the CNC Router Parts table, and our newest addition is the Tormach PCNC 1100. It’s a beast!”
By embracing modern manufacturing and fabrication techniques, Thingergy is able to produce prototypes quicker, replicate products faster, and use less resources than many of the traditional methods. “It’s sometimes a lot easier to change something that is digital, and crank out another version, than it is to do so in an ‘old school’ way. It will always be ‘the right tool for the right job,’ but utilizing the repetition and precision of our army of metal-and-plastic-modifying-robots (3D printers and CNCs) has made things more efficient.”
Ippolito embraces new technology to help keep his shop on the cutting edge and stay efficient in their creative endeavors. Because they are working in the film and TV industries, Thingergy often has tight turn-around times, bringing a new meaning to the idea of time-to-market.
“One of the best applications we used Fusion 360 for was one of our latest and tightest turn around projects, a ten-foot tall, 3D-printed statue of the rapper YG. After we 3D scanned him, we imported the mesh into Fusion 360 to create a super-accurate armature measurement for our welder, so we could form a metal structure for the statue.”
Ippolito has dabbled in everything from CAD and CAM to VR sculpting, and he believes that melding the worlds of old and new will help his company work better. “Utilizing new technology hasn’t hindered our shops work…. Yet,” he explains. “We can now bring something to life and share it in an incredibly short turnaround time. There will always be a place for traditional techniques – and they bleed into our use of technology every day – but the ability to be very technical and precise is a big advantage when using things like CAD, or just 3D modeling in general.”
Add comment
Connect with: Log in
There are no comments