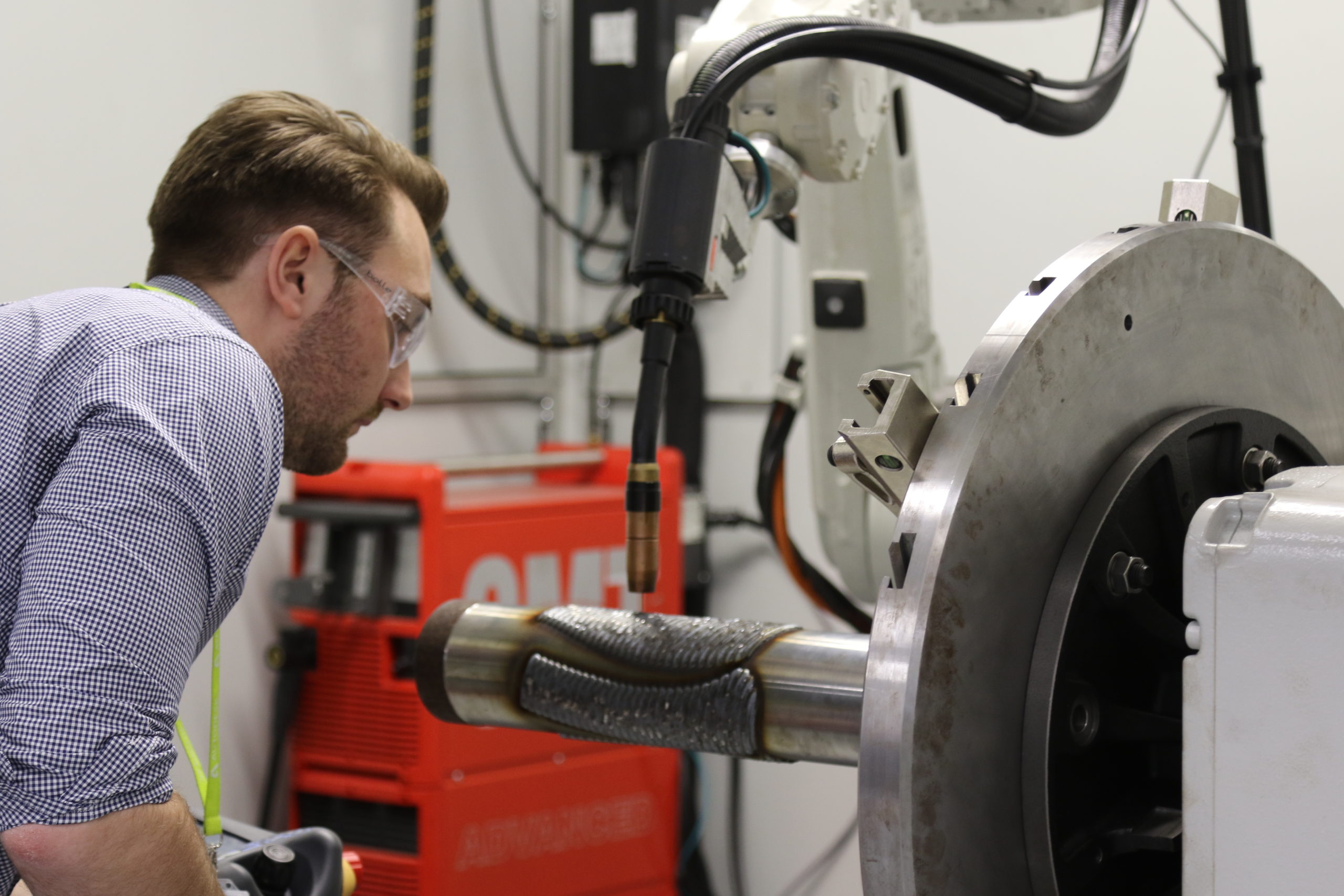
Hybrid technology exists somewhere between pure additive manufacturing, like 3D printing, and pure subtractive manufacture, like CNC machining. It combines both technologies, which are at the extreme opposite ends of the manufacturing spectrum, into a single machine system.
Autodesk supply CAM software aimed at optimizing your hybrid technology process and maximizing your equipment utilization. Known as Netfabb, it helps to streamline your additive workflow and quickly progress from a 3D CAD model to a successfully printed part.
What is hybrid technology?
A part is made by either adding material onto an existing substrate or removing material from a substrate. Adding material is inherently more efficient than subtracting material and in most cases offers greater design freedom.
Hybrid systems use laser cladding to precisely deposit granules of metal onto the substrate. They then liquefy and weld using a precise, high-energy laser. Upon cooling, a unified solid part is created. Once the part has cooled, a CNC machining process follows to refine the product and create features in line with the CAD design.
What is Netfabb?
Netfabb is an all-encompassing software package that incorporates features to help you take your part from design to manufacturing. It enables efficient build preparation alongside tools aimed at optimizing designs for additive manufacturing. It also has the capability to simulate metal additive processes and plan CNC post-processing.
Software features can be grouped into three main categories which we will discuss further:
- Build preparation
- Design optimization for additive manufacturing
- Metal process simulation and hybrid manufacturing
Build preparation
Netfabb allows users to either model complete parts in 3D, or import files created in most commonly used CAD software. After importing, files are converted to STL (stereolithography) format, with users able to adjust mesh resolution, which in turn affects the smoothness of the part. Errors that occur during conversion can be analyzed and automatically repaired.
Not all parts are designed with additive manufacturing in mind. Netfabb allows users to modify designs by adjusting part wall thickness and adding or removing features. Part orientation and nesting can also be adjusted to minimize waste during multi-part manufacturing.
Successfully producing a part using additive manufacturing is heavily dependent on the build support structure. Netfabb offers 37 settings to create an effective support structure. It automatically identifies critical areas of the part and generates a support structure. Support structures can be a tree-and-branch type, or a lattice type.
Design optimization for additive manufacturing
Generative design means lightweight parts with internal lattice structures can easily be created. The lattice structure reduces overall part weight whilst ensuring that the part performance characteristics remain specific to your application and specifications.
Netfabb can create parts with forms that are optimized for stiffness and weight. The user will define the performance parameters and constraints within which the part will fit, and Netfabb will generate an appropriate shape. Simulations can then be performed to verify the performance of the optimized part.
Metal process simulation and hybrid manufacturing
Thermal and mechanical responses of the workpiece can be simulated in order to understand its reaction and reduce build failures. Interaction between parts and potential distortion of the build plate (if creating parts from scratch) or workpiece can also be simulated.
Part geometry is automatically adjusted for distortion identified during the simulation process, ensuring that the final part has the desired shape. Thermo-mechanical simulation can also be applied to large geometries to identify any potential distortion during additive manufacturing.
After the additive manufacturing process is complete your near net shape part can be exported to PowerMill to generate CNC machining tool paths for post-processing.
Netfabb options for your business
Autodesk offers various Netfabb options to optimize your hybrid technology. Each option offers different product features. Your business service offering, staff experience and equipment capabilities will likely determine which software option you choose. The options and their applications are:
- Standard – quickly prepare models for 3D printing and additive manufacturing
- Premium – create near net parts for CNC machining and create build supports
- Ultimate – optimize designs for additive manufacturing using advanced tools
Hybrid technology and your business
Complex, low volume parts can be produced in a single machine environment, reducing lead times and material waste. Multi-metal parts can be created by cladding a different metal on top of another. Damaged metal parts can be clad, measured and machined in one machine.
Combining Autodesk with hybrid technology creates a myriad of opportunities to expand and grow your business.