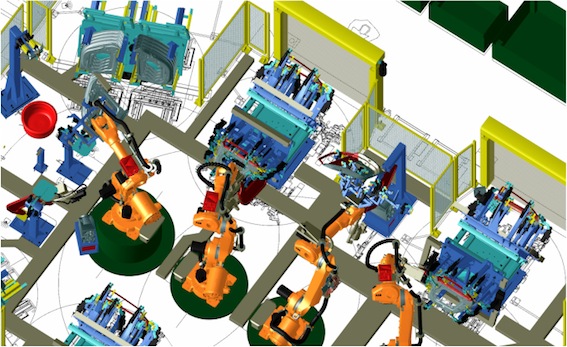
As the manufacturing industry sets about the fourth industrial revolution, you need look no further than smart factories to see a physical representation of this concept. These factories present a new way of manufacturing in which everything is connected. Machine learning and AI (artificial intelligence) systems work together with man and machine to efficiently manage multiple facets of business operations and manufacturing activities. This article aims to introduce the reader to some of the key components of a smart factory and how AI and machine learning integrate into them.
AI in smart factories
The term ‘big data’ has been thrown at nearly everything in recent times. But what exactly is it? To put it simply, big data is a large collection of data gathered in various ways. This data on its own is quite useless to the average person as they cannot turn it into actionable information. Big data needs a software system that can sift through millions of data entries and present the information in summarized formats to a human operator. Better yet, remove the human factor and allow decisions to be made automatically based on this data. This is where AI and machine learning fit into the picture. They can analyze these reams of data and make intelligent decisions based on the inputted information.
Inventory management
A simple way to understand the benefits of a smart factory lie within the sphere of inventory management. Smart factories will track all components and raw materials in the workshop or storage area and automatically maintain inventory levels at an efficient level. This means that as soon as a certain component reaches a critical stock level it will automatically be ordered with little to no oversight. This is just one example of the benefits of a smart factory.
Going one step further, company activities can be planned by making use of information generated from gathered data. This is essentially automation on a business-operations level. Not only does a smart factory leverage automation on the factory floor, but it does the same for operational activities. This is the true benefit of a smart factory – everything is monitored – from how many bolts are in stock to how many units are being produced of a specific product. Coupled with machine learning and AI, factory processes and simple operational activities can not only be automated but the factory can make decisions on how or where to assign resources for optimal results. The speed with which these systems learn and analyze data makes them highly effective – snap decisions can be made in nanoseconds without the input of a human.
Robotic manufacturing
As robotic systems become more advanced you can be forgiven for thinking that the factories of the future will have no humans involved… just raw materials rolling in one side of a factory and products rolling out the other side. It has however been discovered that human-machine cooperation results in higher productivity than each on their own. This realization has driven the development of robotic systems that can work alongside humans without fear of injuries. Robotic systems can be taught to do a specific task by observing a human and then not only mimicking the action but also using machine learning to improve on the efficiency of the action.
Design of new products
Another facet where smart factories differ from traditional facilities is the time between concept and product. Design engineers have immensely powerful software systems that can assist in the design process. These software systems use machine learning to optimize designs based on a few simple input parameters from the engineer. In a short while the engineer will be presented with hundreds if not thousands of component configurations that meet the set criteria. The engineer can then choose the best design, make a few changes and submit the design directly to a CAM (Computer Aided Manufacturing) system that will generate the tool paths to manufacture that component. The g-code can then be sent directly to the factory and the system can decide which machine will be best suited to handle that job. This ensures minimal steps between design and manufacture.
Final thoughts
Autodesk offers multiple software systems that can be utilized by companies wanting to make the jump into the world of smart factories. Anything from robot programming to quality control and CAM systems. Furthermore, these systems can be interlinked into the overall structure of a smart factory, providing unprecedented levels of automation and interconnectivity.
With Autodesk PowerMill you can simulate and program your robots, with generative design you can automate the design process, and with PowerInspect you can automate your quality control procedures.
Add comment
Connect with: Log in
There are no comments