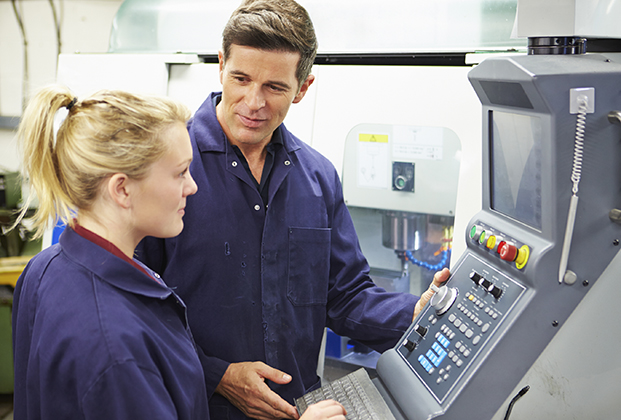
Autodesk provides a comprehensive suite of integrated CAM (Computer Aided Manufacturing) software packages aimed at making CNC (Computer Numerical Control) machining as easy and efficient as possible. The software is designed for every phase of the manufacturing process. It allows you to manage projects, design solutions, refine designs for machining, and inspect the final product.
Machine shops annually spend thousands of hours programming complicated G-codes, tying up expensive labor. Integrating various software programs into your business can reduce programming time, creating opportunities to save money.
CAM software for superior CNC machining
Autodesk CAM software is suited to 2-, 3-, and 5-axis CNC machining centers, multi-tasking centers, and wire EDMs. Software packages can be combined to help you efficiently manage your business.
Irrespective of the size of your business, the following software packages, individually or in any combination, can benefit your organization:
- PowerMill – expert high-speed and 5-axis machining software
- FeatureCAM – automated CAM for faster manufacturing
- Fusion Production – smart manufacturing using the cloud
- AutodeskHSM – integrated CAM for Inventor
PowerMill
PowerMill is suited to high-speed machining, extracting maximum performance from your 3-axis and 5-axis CNC machines. It is able to work with solid, surface, STL, and wire mesh source files created in any CAD (computer aided design) software.
Tool paths can be optimized by trimming and reorganizing the program. Programmers can create machining templates for repetitive, mundane operations, reducing programming time. Excellent surface finishes can be achieved through modifying the cutting sequence, changing entry and exit points, the type of cutting tool used, and changing the cutting direction.
Switching to PowerMill allowed Precision Mold & Machining of Warren, Michigan to improve their bottom line by up to 15%. PowerMill made programming easier and more efficient, optimizing their machine utilization.
FeatureCAM
FeatureCAM reduces programming time by automating workflow from design to NC-code. Feature recognition identifies machining features and their machining operations directly from your CAD model. This eliminates the need to program simple features.
More experienced programmers can incorporate their knowledge in FeatureCAM to not only share it with less experienced programmers, but also standardize processes. This reduces the risk of less experienced programmers making costly mistakes.
Pre-machining simulation identifies potential collision points between the cutting tool and the workpiece. During simulation, FeatureCAM is able to automatically modify the tool path and change the cutting tool to avoid a collision. In multi-axis machines the workpiece can also be tilted to avoid a collision.
Frontier Technologies of Long Beach, California managed to reduce their CNC machining time by up to 50% with the use of FeatureCAM’s feature-recognition ability. FeatureCAM allows the company to perform multiple operations on its 5-axis CNC machine instead of individual operations on multiple machines.
Fusion Production
Fusion Production connects people, machines, and data in a single, cloud-based tool. Managing your CNC machining business is made easier through real-time monitoring of production schedules, job tracking and machine utilization.
Digital work instructions can be created and communicated electronically to the shop floor, reducing paper clutter. They can be viewed on desktop or mobile devices on the shop floor. The works instruction tasks are sequenced in line with the machining sequence, and includes cycle times and detailed setup sheets.
Fusion Production also allows real-time monitoring of production capacity per machine. It provides visibility into the jobs currently in production, on which machines they are running, and which jobs are scheduled next. Not only does this provide insight into equipment utilization, it also assists Sales and Marketing when quoting on new business. It eliminates the risk of overselling capacity on some machines, whilst having excess capacity on others.
AutodeskHSM
AutodeskHSM fully integrates into Autodesk Inventor to allow streamlined workflows that dramatically reduce programming time. Model associativity means that design changes made to your model in CAD is automatically reflected in the CAM cutting program.
Built-in simulation and detection identifies potential tool and workpiece collisions. This allows you to make adjustments to the CNC machining program before cutting starts. This feature gives you the peace of mind to let your machines work unattended.
AutodeskHSM includes “Adaptive Clearing”, a feature that enables both-ways roughing. Roughing cuts are made in both directions, eliminating wasteful cutter repositioning. Fewer repositioning moves improve efficiency, creating more capacity for you to take on more business.
The future of CAM and CNC machining
CAD-CAM integration may see a merging of certain industry roles with the gap between engineers and machinists reducing significantly.
With CAD starting to feature generative design, the hope is that CAM will become more intuitive. As CAD-CAM becomes more intuitive, more complex designs will become possible. What was once thought to be too complex, or even impossible, will become a reality.