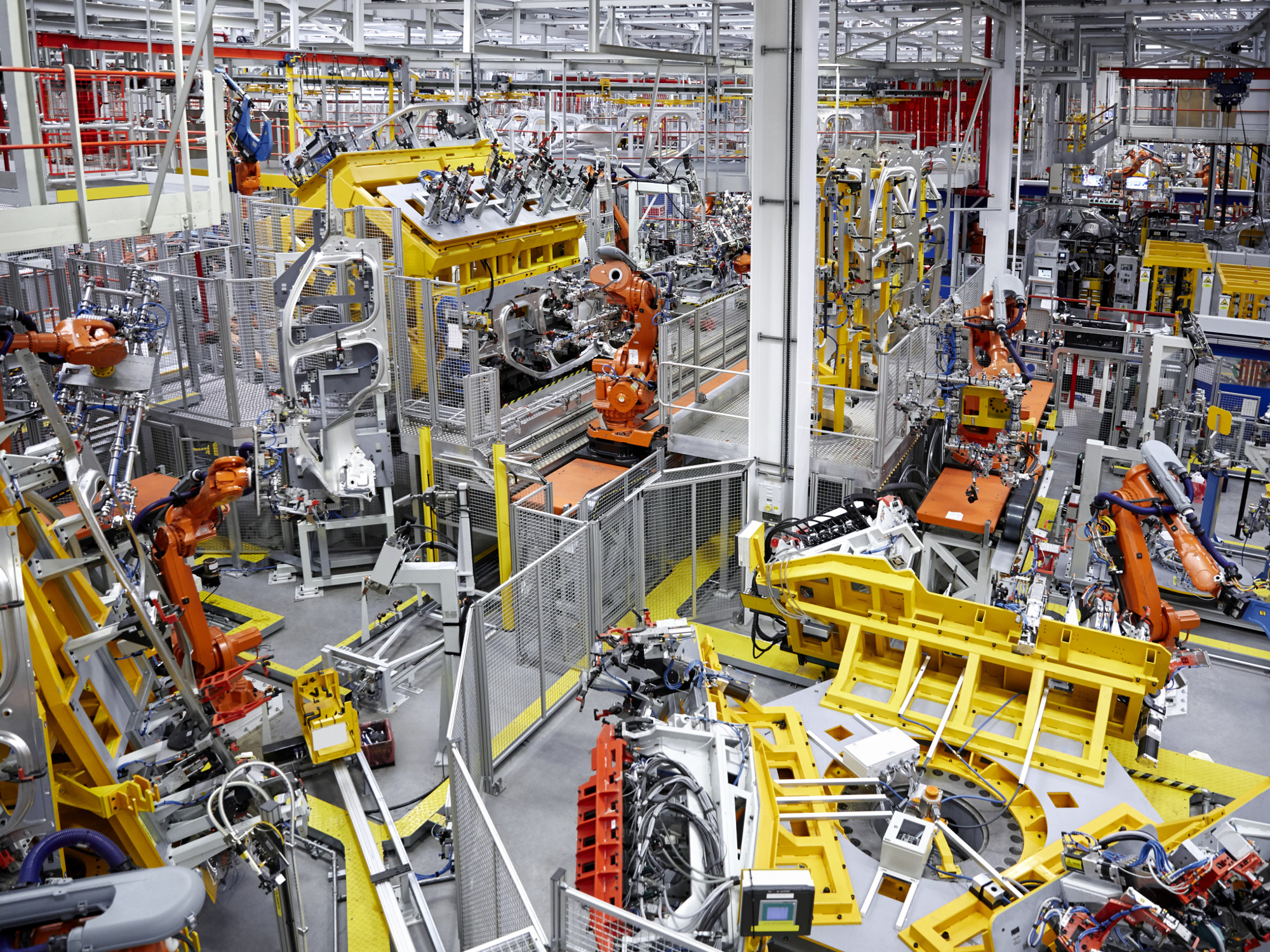
Are you ready to save your factory millions of dollars annually in change management costs? Keep reading.
Smart factory owners, operation managers and manufacturing executives constantly look for better ways to meet project budgets, deadlines, target production rate/volume, and lead time while achieving and maintaining product quality after factory changes.
Facility and plant managers must always keep their eye on the ball. On the shop floor, people, equipment and raw-materials are all moving parts that must seamlessly mesh to enable the fast and affordable production of high-quality products. With so many parts and components, machines and processes can often break down, and solving them can be challenging.
It has been repeatedly shown that the top factories know how to control their change management projects and are significantly faster at implementing moderate and major changes. The key is relying on formal change management processes and procedures that grant visibility into the full project scope to forecast potential pitfalls, so they can implement risk mitigation before problems happen.
A recent study by TechClarity found that top factories are 53% more likely to have a formal impact analysis process to predict the outcome of projects during the planning phase, allowing them to better understand the full scope and impact of their efforts and foresee possible risks. Top factories are also 54% more likely to simulate material flow, helping them predict and optimize outcomes and prevent late surprises.
Here’s a chart of the top 8 best practices and processes that support change in the factory:
Some of the key takeaways from the study is that factories are 75% more likely to use Six Sigma for change, which is consistent with their adoption of formal change processes. Factories are also 59% more likely to use different procedures depending on project complexity, and are more disciplined when and where it is most needed; yet at the same time, they exercise flexibility in managing minor changes.
One of the key software differentiators is the use of design visualization for training — a quickly emerging industry best practice. Another significant organizational finding is that top factories are 48% more likely to have a change control board (CCB) to evaluate and coordinate change holistically across functions and departments.
Adopting these best practices leads to superior operational capabilities, which in turn support cost efficient change management in the factory. Of course, this is all supported by modern factory software capabilities highlighted in the following chart:
The first category of software used by the successful factory elite is simulation tools to predict and optimize the impact and scope of proposed changes during the planning stage to avoid late surprises and optimize designs while options are still flexible. Top factories are significantly more likely (46%, 56% and 60% respectively) to simulate equipment, material flow, and ergonomics/operator impacts related to change. “Manufacturers need to ensure the changes that they make are right before committing to expensive and disruptive plant modifications,” the report states.
The second category of software used by top factory executives to achieve success is digital platforms that support communication, collaboration, and information visibility. Top factories are 59% more likely to use online collaboration capabilities.
What do all these percentages mean and ultimately add up to? Factories rely on two software categories: software that enables cross-functional coordination of change at the enterprise level as well as simulation tools to get changes right in a digital environment before committing to physical change. Simulation software leads to real world success and collaboration software empowers teams that share their knowledge. The idea is to experiment with designs in the digital world to keep hypothetical factory problems from becoming real.
Or — to quote Walt Disney — “If you can visualize it, if you can dream it, there’s some way to do it”. That idea applies to factory design success as well.
To learn more about how modern factory design visualization and optimization software solutions can reduce the cost of change management, click here to watch a short 3D video that takes you inside the workings of a modern virtual plant.