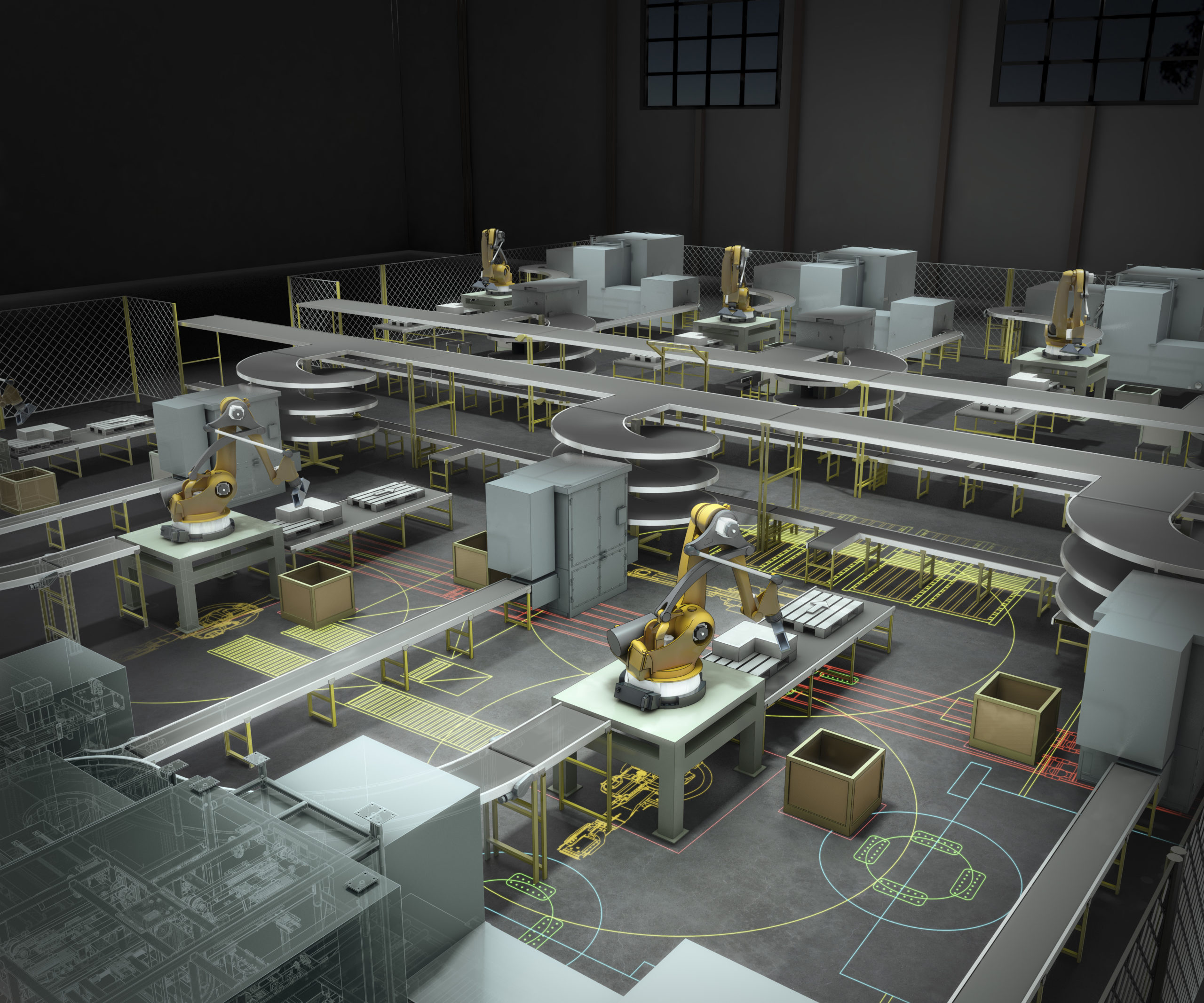
Change is not always easy. When it comes to factory operations, even a simple change can introduce all sorts of risks and uncertainty. Most companies experience project-oriented issues, such as missed due dates, overtime, and cost overruns. Factory changes can also negatively impact quality, reduce production efficiency, and other create other problems that may themselves require a change.
So what do the top factories do to overcome the high costs of factory change? They employ processes and modern software tools that help them:
- Better understand the full scope and impact of change in advance to avoid late surprises
- Communicate, collaborate, and share information to work as a team more effectively
- Adhere to more formal change management processes
One of the two main themes that came up in a recent study by TechClarity was the need for software to enhance cross-departmental, cross-functional coordination of change at the enterprise level, and top performers were 2.5 times as likely to have factory software to simulate equipment, material flow, and ergonomics/operator simulation. Simulation, visualization and optimization tools are highly differentiating, helping manufacturers determine the impact of change and enabling them get changes right in a digital environment before committing to physical changes.
See this graph below on the top five software solutions supporting factory change:
The study concluded that top factories are adaptable factories and make changes more predictably, which helps them more effectively meet their targets for budgets, due dates, and resulting production volumes. To become a top factory, the study recommended the following:
- Implement and adhere to formal change management processes
- Follow known best practices such as change control boards, cross-functional change teams, and formal impact analysis
- Leverage processes and tools to improve communication, collaboration, and information sharing including enterprise tools such as BIM and PLM as well as project management
- Adopt processes and software to simulate material flow, operators, and equipment to understand the full scope and impact of changes, optimize resulting performance, identify issues early, reduce risk, and get changes right the first time
- Consider adopting reality capture technology, such as laser scanning and overlaying intended changes on top of an accurate “as-is” model
With Autodesk Factory Design Utilities, the industry’s only factory design visualization and optimization software, factory owners can literally visualize factory success before a factory is even built or reimagined. To quote Walt Disney: “If you can visualize it, if you can dream it, there’s some way to do it”. That idea applies to factory design success as well.
Integrated within Autodesk’s Product Design & Manufacturing Collection, factories have an all-in-one solution that ensures superior data management and collaboration, and supports workflows across complementary simulation applications, allowing you to:
- Create electrical schematics inside AutoCAD Electrical and establish an electromechanical link with Inventor for routing and harness design
- Use AutoCAD or AutoCAD Mechanical for 2D conceptual design, and use that data to generate 3D models in Inventor that will update if the design is changed
- Use ReCap Pro to process point cloud data capturing the as-is state of your factory and integrate that into the model in Inventor or Navisworks
- Perform large scale design review with Navisworks, including collision detection for factory layouts
By using Factory Design Utilities, global OEMs and factories everywhere can create a complete 3D digital model of their facility to address the following factory challenges:
- Building new greenfield factories
- Major retrofits of existing factories or lines
- Moving existing factories
- Quality improvement (including LEAN, xKD, 6 Sigma)
- Significant new product launch (new platform or vehicle, model upgrade)
- Transitioning the manufacturing labor model (outsourcing, off/next-shoring)
- Increasing automation
- Creating a manufacturing Center of Excellence
- And identifying and eliminating potential factory failures and operation risks of all kinds
Modern factory design visualization tools are key to real world manufacturing success; and it’s a lot less risky experimenting with simulation models in the virtual realm than the real physical world.
To learn more, click here to watch a video and go inside a virtual factory developed using Factory Utilities.