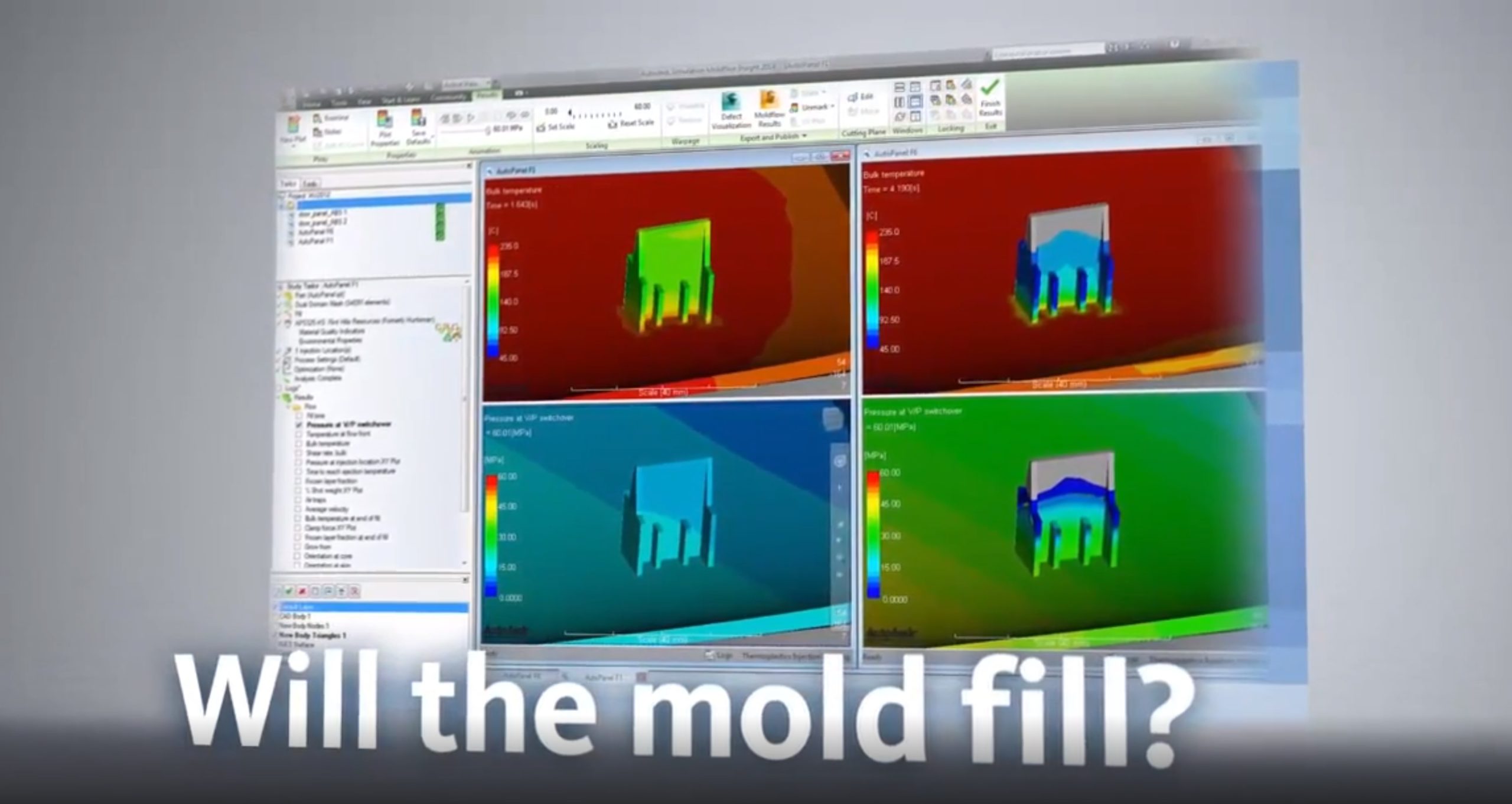
Note: This story was originally published at https://www.moldmakingtechnology.com/
The mind of a mold builder never ceases to amaze me. Their creativity, ingenuity, and intelligence makes them impeccable problem solvers, which is why I thought you might be interested in getting inside the mind of a fellow problem solver to learn how he came up with a very popular simulation software.
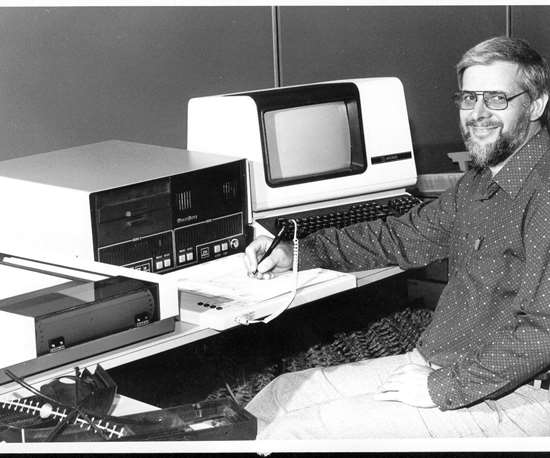
Fig 1. Colin Austin is an award-winning researcher, engineer, and the inventor of Autodesk Moldflow® software
Ever wonder where technology comes from? A lot of it comes from the minds of men like Colin Austin. Colin is an award-winning researcher, engineer, and the inventor of Autodesk Moldflow® software. He was born in Australia, began his career in R&D with Johns Hydraulics and then worked as a lecturer for the Royal Melbourne Institute of Technology (RMIT) before developing Moldflow. To celebrate the 40th anniversary of this software, Colin shares his journey of invention in this quick Q&A.
Q: What was your invention inspiration? What problem were you trying to solve?
A: I was working at Johns Hydraulics making injection molding machines. It was a very different world at that time. We knew that if you could make precise calculations, you could make more efficient designs and save vast amounts of money. Why use 20 mm if you only need 16 mm? But making calculations took too long, and they were not that precise or reliable, so most engineers didn’t do them. Then at the Royal Melbourne Institute of Technology, we got our first real computer. It used punch cards, which was a nightmare. After hours, however, I could work on a terminal. And when I started to make these calculations in real-time, I realized it was going to change the world. That was the birth of Moldflow.
Q: Do you remember the first lines of code you wrote?
A: Well, I couldn’t sit down today and recode them! But I can remember the process very clearly. I started with the formula for calculating cooling times. That was the first line of code. Then I started doing flow calculations, which were very interesting. I’m an obsessive sort of person. I mortgaged my house to buy my microcomputer and started coding all the time. It was a DTC that had 64KB of memory, 32KB of which was taken up with BASIC.
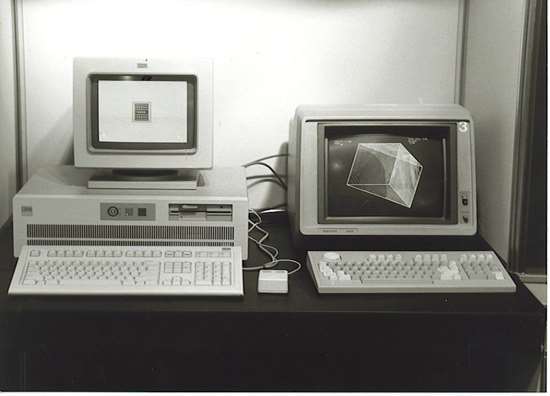
Fig 2. Early computing power was limited by comparison with today’s cloud-based super computers
Q: How did you turn this code into what became Moldflow?
A: The first piece of serious code was a classic finite difference scheme, where you work out the heat going in and the shear stresses and then integrate over the section. If you ever saw the old code, you would find something called “F-factors.” F stood for fudge! I would run the finite difference scheme, then play with the “fudge factors” until I got a reasonable correlation. Eventually, I got to work accurately. Then I came up with the idea of developing dimensionless quantities for flow and heat transfer and translated them into code. Essentially, that was the first version of Moldflow.
Q: How was this software different from traditional design practices?
A: There was not much in the way of design practice, just empirical evidence. If you’re making a mold, you will use 3/8″ runners. That was just the rule of thumb. Sometimes it worked and sometimes it didn’t. Moldflow revolutionized the way our industry thought about how to design a mold. It’s not that it gave you an answer. It gave you the ability to simulate experiments, so you could make ten molds and see which one worked best.
Q: What was the response from the first prospective customers?
A: They thought I was a nutter! Much of what Moldflow demonstrated was counterintuitive. For example, if your mold isn’t filling, the classic solution is making a bigger runner system, which is logical. But Moldflow said to do the opposite: make it smaller to develop frictional heat, so the material hits the mold at a higher temperature. That was a very difficult message to sell. At one seminar the audience wasn’t exactly booing, but they were fidgeting and asking nasty questions. And then an engineer from Kenner stood up and testified that yes, in fact, using smaller runners had helped the company solve a particularly difficult problem with one of their toys from “Star Wars.”
Q: What was it like selling in those days?
A: I bought my airline tickets on a credit card and went around the world racking up an unbelievable bill. I went to Europe and the United States and was a laughingstock. Then I went to Japan, and it saved my life. I spoke with a team at Toshiba who asked me to analyze one of their molds. I worked it out and thought it was a pretty good demo. The next morning we met again, and they said Moldflow was “very good.” I was confused. I said: the numbers are very good? No. They had been up all night running their machine, verifying my results! Toshiba became a Moldflow customer, and so did some other Japanese companies, and eventually, I paid off my credit card bill.
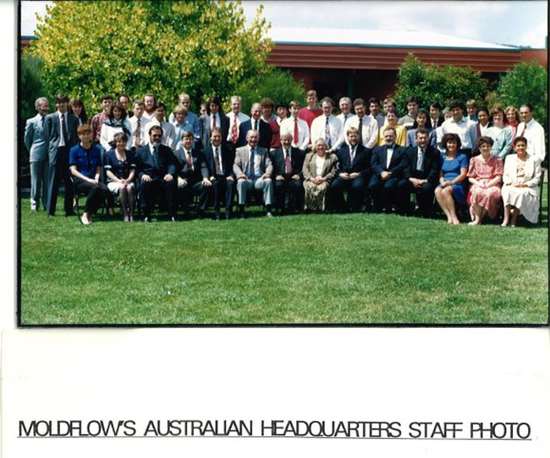
Fig 3. The original Moldflow team pictured in front of the Australian HQ
Q: How did the software change over time?
A: The major change was the development of finite elements. The early versions were layflat, which was the only way to describe part geometry to the computer. It was cumbersome and required the mold designer to have an instinctive understanding of how the plastic would flow. With finite elements, just about anyone could see how the flow would happen. That was a huge leap forward. Instead of 10 people in the world who could understand it, there were 10,000.
Q: Eventually you built an in-house molding lab. Why was material testing so important?
A: You have to test the material to get the data for high shear rates and high temperatures. It’s essential. We developed instrumentation to measure the viscosity.
Q: What are you working on today and why is it important to you?
A: One of the biggest problems in the world is our health. I’m nearly 80. When I was a kid, the major health issues were infectious diseases. Medical science has made stunning improvements in this arena. But they have failed to combat non-infectious diseases like diabetes, heart disease, stroke, and dementia. I believe our guts are like a supercomputer with trillions of bacteria communicating with swarm intelligence, and that the failure of this system causes many of these diseases. I’m working out how to grow food that will repair the system, reinforce our gut biology, and fight diabetes and other diseases. So they still think I’m a nutter!