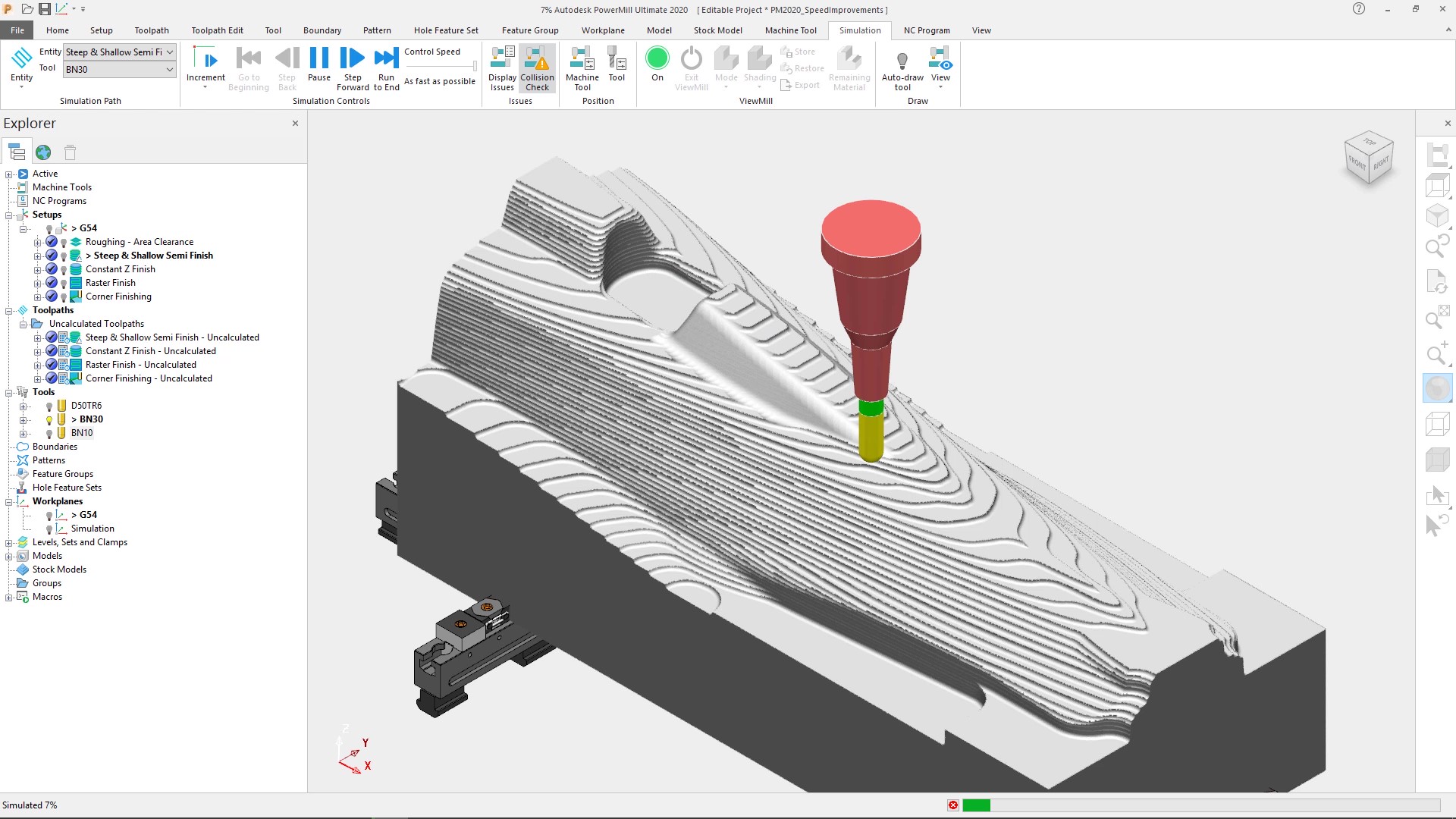
Article by Clinton Perry, PowerMill Product Marketing Manager
PowerMill is Autodesk’s CAM solution for high-speed and five-axis machining. It offers a comprehensive range of strategies and powerful editing tools to ensure efficient, safe and accurate machining, especially for companies that are using sophisticated CNC machine tools to produce complex shapes in challenging materials. PowerMill is used in a wide range of industries but is particularly successful in mold, tool and die, complex aerospace and automotive applications.
The release of PowerMill 2020 represents a significant shift in development in recent years – with a clear focus on usability, reliability, and speed.
Which is more important – speed or quality?
The previous releases of PowerMill have seen significant improvements in terms of robustness and safety. Technology such as collision avoidance using automatic tool-axis tilting makes it easier for CAM programmers to create safe NC code that can be run on their CNC machines. Autodesk’s pursuit of safe, collision-free toolpaths has resulted in the introduction of additional safety checks within the core PowerMill algorithm. These safety checks are a good thing – but they do carry a processing overhead which can have an impact on overall calculation time.
In direct response to feedback from customers and internal users, the Autodesk PowerMill team re-focused its development muscle on outright performance (speed).
Algorithm profiling
The first step involved profiling the performance of a number of PowerMill’s most commonly used commands. The chart below shows the profiling of one such command – namely the Constant Z finishing toolpath – across eleven customer example toolpaths. By profiling the major steps contained within the Constant Z algorithm, the development team was able to identify sections of the code where the greatest potential time savings could be achieved.
The PowerMill team also used this as an opportunity to upgrade the core algorithms to make better use of multi-threading capabilities seen in modern PC architecture. The net result is substantial time savings when calculating toolpaths including; Area Clearance, Constant Z, Raster, 3D Offset, and Corner Finishing.
How much faster are we talking here?
During an intense BETA test program, the PowerMill development team analyzed calculation times across a large selection of internal and external test parts. Let’s take a look and see what they found.
Speed Results – Test 1 – Lay-up Mold
The first test case is a composite lay-up mold from the motorsport industry. The chart below shows the typical calculation times for a selection of toolpath types – with a direct comparison between PowerMill 2019.2 and PowerMill 2020. Tests were carried out using a Lenovo P71 laptop with quad-core Xeon 3.1Ghz chips running 64Gb of RAM and a Nvidia Quadro P4000 graphics card with 8Gb of GPU memory. The timings show that PowerMill 2020 is between 16% and 67% faster than PowerMill 2019.2 at calculating the 4 most commonly used toolpath types.
Speed Results – Test 2 – Core Insert
The next test case relates to a medium sized, but highly intricate, double impression core block for a child’s toy car. The chart below shows the calculation times for a range of toolpaths. As before, PowerMill 2020 is considerably faster than 2019.2. For this example, the total time taken to calculate all toolpaths was 24% faster in PowerMill 2020.
How does PowerMill 2020 compare with older releases?
While it’s clear that PowerMill 2020 is faster than PowerMill 2019, it’s worth taking a moment to compare performance with older versions – such as PowerMill 2016. But why 2016, we hear you say? Well, in customer discussions, the 2016 release is often mentioned as being the benchmark release (in other words, the fastest). So how does 2020 compare with the 2016 release?
2020 versus 2016
Let’s start by considering the toy car core block shown previously. If we repeat our tests using PowerMill 2016, we can see the following.
Look closely at the calculation times for PowerMill 2019 and 2016. We can see that some toolpaths (specifically Constant Z, Raster, Corner Finishing) are actually slightly slower in 2019.2 (remember all those additional safety checks). Other toolpaths (such as 3D Offset) are faster in 2019 than 2016 on this example.
When we compare PowerMill 2020 with 2016, the difference is striking with time savings ranging from 9% to 58%. The total time to calculate all toolpaths in PowerMill 2020 is 42% faster than 2016, and 24% faster than 2019.
Simulation and Verification
The speed-up work doesn’t end at toolpath calculation. Simulating toolpaths (using ViewMill to visualize the removal of stock from a virtual block of material) has also been overhauled and is now up to 33% faster in many cases. As the simulation code is used behind the scenes as part of NC program verification, this also benefits from substantial time savings.
To learn more about the multiple speed improvements in PowerMill 2020, watch this VIDEO.
Multi-threaded leads and links
Part of the time savings seen above are caused by a significant change to the way PowerMill calculates leads and links (the connections that join cutting moves together). One of the big strengths of PowerMill is its ability to allow leads and links to be calculated independently to the toolpath. This means the lead and links can be edited without having to recalculate the entire toolpath – a huge time saving and allowing programmers the ability to experiment and optimize toolpaths before going anywhere near the CNC machine. With PowerMill 2020, the leads and links algorithm has been overhauled to make better use of multi-threading capabilities. In our tests, we regularly saw calculation times 59% faster in 2020 than using PowerMill 2019.
You can learn more about leads and links by watching this VIDEO.
So what else does PowerMill 2020 offer?
Uphill Corner Finishing
If all those wonderful speed-ups weren’t enough, PowerMill 2020 also includes a number of improvements that impact overall usability. The first is the addition of an “uphill cutting” option in PowerMill’s Corner Finishing strategy. PowerMill has had the ability to create corner picking toolpaths for a number of years. These strategies can differentiate between steep and shallow sections of the corner being cut and machine the regions using different approaches. When considering the steep regions, PowerMill has historically created toolpaths that cut the material in a bi-directional fashion – cutting up and down the corner.
The new “uphill cutting” option changes this and produces toolpaths where the cutting is in the uphill direction only. This changes the cutting forces experienced by the tool resulting in a reduction in the likelihood of chatter, cutter push off, tool breakage or damage to the workpiece.
You can learn more about uphill corner finishing by watching this VIDEO.
Model Filleting
The final enhancement we’ll talk about here is one that originated from Autodesk’s HSM product. For many years, PowerMill users have had the option to fit arcs into the internal corners on toolpaths such as Constant Z and Raster. The introduction of these arcs minimizes the risk of cutting tools engaging into heavy amounts of stock that can cause shock loading and breakages. Unfortunately, the arc-fitting option was only available for toolpaths that were planar and not 3D scanning toolpaths. With the release of PowerMill 2020, code originally developed for HSM has been plumbed into PowerMill allowing more toolpaths to have sharp internal corners replaced with smooth, rounded motion.
The new model filleting option is currently limited to working with “Optimized Constant Z” and “Steep and Shallow” finishing toolpath types and works by creating an additional CAD as part of the toolpath calculation. This additional model adds “fillets” into corners based on a user-defined radius (based on tool diameter units). The additional model is cached as part of the toolpath calculation, meaning it can be reapplied to multiple toolpaths, and is only reprocessed if the user decides to change the fillet radius.
Adding fillets to the model in this way greatly reduces the likelihood of tool breakages, helps prevent parts from being damaged, and also means NC programs can be run at the programmed feed rate (and not slowed down to accommodate the risk of heavy cuts in internal corners) resulting in faster machining cycle times.
To learn more about the new model filleting option, watch this VIDEO.
Where can you find PowerMill 2020?
Eligible customers with an active subscription or maintenance agreement can download the latest release using the Autodesk Desktop App or by logging into their Autodesk Account. If you’re new to PowerMill you can learn more by visiting www.autodesk.com/powermill.
Free evaluation
Want to evaluate PowerMill and see how it can help you solve your toughest CNC machining challenges? Contact our team of manufacturing specialists at www.autodesk.com/products/powermill to learn more.