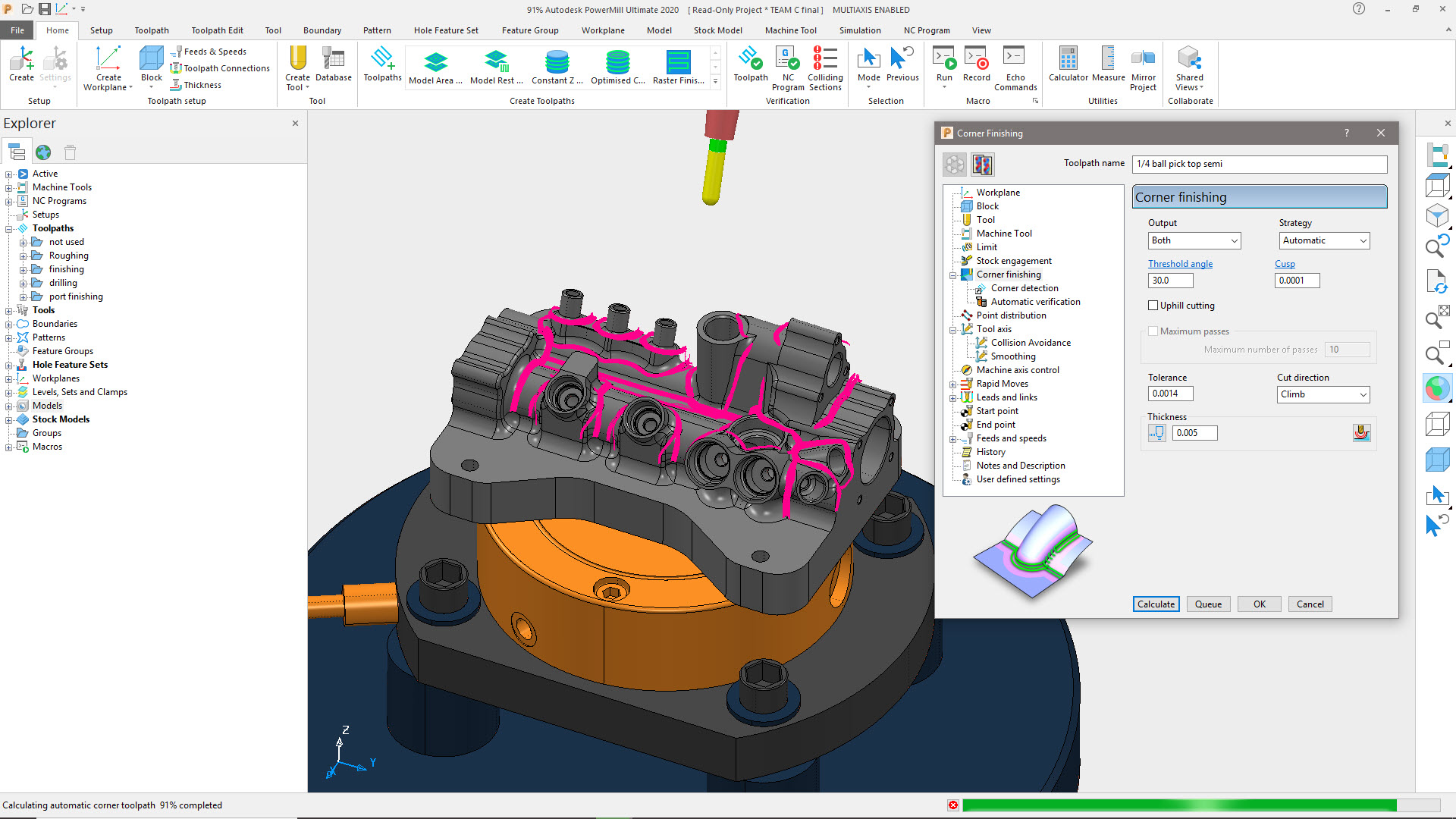
Article by Clinton Perry, PowerMill Product Marketing Manager
Ever since PowerMill was first released, back in 1995, it has focused on delivering fast and reliable CAM programming tools to meet the needs of industries including aerospace, automotive, medical, mold & die, industrial machinery and more. The release of PowerMill 2020 in May 2019 represented a significant shift in development in recent years – with the bulk of the development focus being on improving the usability, reliability, and speed of PowerMill for its core userbase.
PowerMill 2020.1 – hits the streets
This continuing focus on delighting PowerMill users sees the release of the latest update, 2020.1. Eligible customers will begin to see the new update appearing in their Autodesk accounts, starting October 10th 2019. The 2020.1 update includes some impressive highlights, including:
- Improved model filleting
- New model export options
- Faster automatic collision avoidance
- Faster corner finishing
- And more…
Let’s take a deeper dive into these changes.
Model filleting – even more opportunities to protect tools (and save money)
First introduced in PowerMill 2020.0, model filleting automatically adds fillets to the internal corners of 3D CAD models as part of the toolpath calculation. An additional “manufacturing model” is produced and used to help prevent the cutting tool from entering sharp internal corners, where excess stock could result in shock loading that could damage the cutting tool, workpiece, and/or machine. The 2020.0 release of model filleting intentionally limited the command to work with a small number of 3-axis finishing toolpath types. With the release of 2020.1, this limitation has been removed, meaning all 3-axis finishing toolpath types can benefit.
To learn more about model filleting in PowerMill 2020.1, watch this VIDEO.
New model export options for enhanced collaboration
To get the very best out of any CAM software tool, there’s generally a need to produce 2D and/or 3D CAD model data. This additional geometry can be used to control the extents of machining, to add fixtures and workholding, to prevent toolpaths from accessing areas where the design may be evolving, or to precisely control the motion of 5-axis CNC machine tools. This ability to transfer CAD model data into and out of a CAM system is essential. With the release of PowerMill 2020.1, the model export options have been enhanced to provide a greater range of file types. In addition to the existing file types (.DGK, .DMT), models can now be exported using neutral files (.IGES, .STEP, .ACIIS SAT, Wavefront OBJ, and PDF) and native formats (Rhino, Additive Manufacturing, and Fusion Modeling data). This makes it easier for CAD and CAM team members to share data and collaborate on projects.
To learn more about model export options in PowerMill 2020.1, watch this VIDEO.
Faster/safer automatic collision avoidance
The PowerMill development team has spent a considerable amount of time and effort improving the user experience when programming 5-axis parts. While PowerMill offers fantastic levels of control for 5-axis machining, this range of options can be a little daunting for those that are new to, or infrequent users of 5-axis programming. It was with this in mind that PowerMill 2019 introduced the concept of Automatic Collision Avoidance when calculating toolpaths. Regardless of the tooplath type being produced, or the shape of the model being machined, the automatic tool tilting option was a safe “go-to” choice. If selected, any collisions or near misses involving the tool would be identified and avoided by simply tilting the tool away in a safe, controlled, and predictable fashion.
Using real customer data, the PowerMill team has continued to focus on improving the speed and reliability of the automatic collision avoidance, so that more collisions are identified and removed than may have been found by previous versions. In one customer example, the time taken to calculate a safe, collision-free toolpath was reduced from 9hrs 30mins (with PowerMill 2020.0) to 2hrs 36mins (2020.1) a reduction of more than 73%.
Faster corner finishing
Those of you that reviewed our previous blog entry about PowerMill 2020.0 will have noticed the major focus on speed, speed, and more speed!
This has continued with the release of 2020.1. As well as the previously mentioned automatic collision avoidance, there have been substantial speed-ups for toolpaths including; area clearance, rest finishing, and corner finishing.
The graphic below compares the calculation times of corner finishing toolpaths in PowerMill 2020.1 and 2019.2 – using three customer-supplied test parts. We can see that one example, test 1, shows calculation times 53% faster in 2020.1 than 2019.2. In fact, our tests suggest the biggest time savings can be had on the most challenging parts where calculation times may have been problematic in the past.
So what else does 2020.1 offer?
The complete list of improvements is available on the PowerMill online help site. Choose to review the official release notes, or take a deep dive into the list of fixed issues and learn about.
- More robust cutter compensation
- Clearer NC program status icons
- Enhanced raster toolpaths with optimized parallel pass
- Multiple GUI improvements
Alternatively, download the official flyer documents to summarize the improvements to PowerMill 2020.1 and remind yourself about the major speed-ups included in PowerMill 2020.0.
Where can you get hold of PowerMill 2020.1?
Eligible customers with an active subscription or maintenance agreement can download the latest release using the Autodesk Desktop App or by logging into their Autodesk Account. If you’re new to PowerMill you can learn more by visiting www.autodesk.com/powermill.
Free evaluation
Want to evaluate PowerMill and see how it can help you solve your toughest CNC machining challenges? Contact our team of manufacturing specialists at www.autodesk.com/powermill-evaluation to learn more.