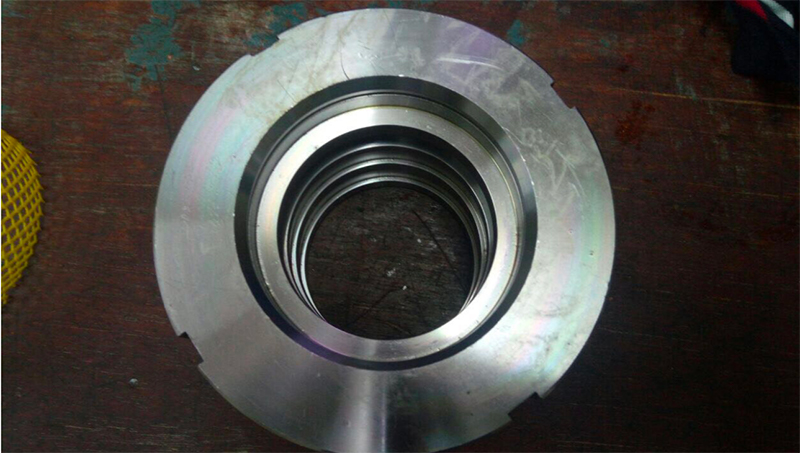
Managed by a diligent team of skilled engineers and staff, Vaasan Engineering Works understands quality is a key factor in earning the trust of their customers. With this in mind, they chose to invest in some of the best technologies around, including Autodesk FeatureCAM software.
Located in the bustling Ambattur Industrial Estate in Chennai, Vaasan Engineering Works is a well-established name in the CNC machined components manufacturing and exports industry. Founded in 1990, the company manufactures a wide range of hydraulic, automotive and general engineering components.
Managing Director, Mr L. Venugopal says, “We are a well-resourced unit with an in-house facility for all operations. As a company, we also have our focus on developing new products every year for our existing customers, improving the work processes and practices followed in our organisation.
“Before we invested in Autodesk FeatureCAM, we use to carry out manual programming, which took up our time and effort. By switching, we managed to save a lot of time, cost and work effort. Performing trial runs also left us with high amounts of material waste.”
What is FeatureCAM?
FeatureCAM is a CNC programming software that uses manufacturing knowledge to intelligently make decisions, produce results and remove repetitive processes. It includes feature recognition and automation tools to reduce programming time. It also helps visualise safe tool paths with simulation. It automates your workflow from design to NC code, reduces programming time and increases consistency for a range of CNC applications.
How does it work?
The first step is receiving the 2D drawing, then planning how to hold the component, decide on the fixture and then the final CAD model is defined for machining process.
Creating a customised tool library based on the availability of cutting tools in the workshop, all the required data including shank, holder & practical-machining parameters are saved in the FeatureCAM tool database which makes it easy and quicker for Vaasan Engineering Works to select and create the accurate tool paths. The tool-library is continuously updated based on new cutting tool additions in the workshop.
Mr L. Venugopal explains, “once the tool paths are created, we simulate the entire machining process in FeatureCAM’s graphical virtual machining environment. This is a mandatory process before generating NC codes. While the process of simulation is going on, all fixtures, parts or cutting tools are checked for collisions. In the case of any collisions, FeatureCAM immediately pauses the machining simulation and also provides the information on errors for correction to achieve safe tool paths.”
After successful simulation, tool paths are converted to NC programs with a single click. For 2D and 2.5D machining, the FeatureCAM software provides NC output with various cycles by default, which reduce the length of NC programs and make it easier for the machine to understand and perform machining activities effectively.
Mr L. Venugopal continued, “FeatureCAM is highly automated and user-friendly. By using it, we can now avoid on-machine trial and error methodology and send the error-free, accurate NC programs directly to our machines to start production.
“We are committed to helping our customers, and we are continuously trying to improve the quality and delivery of our products. Being a customer centric organisation, our ultimate aim is to provide the utmost client satisfaction.”