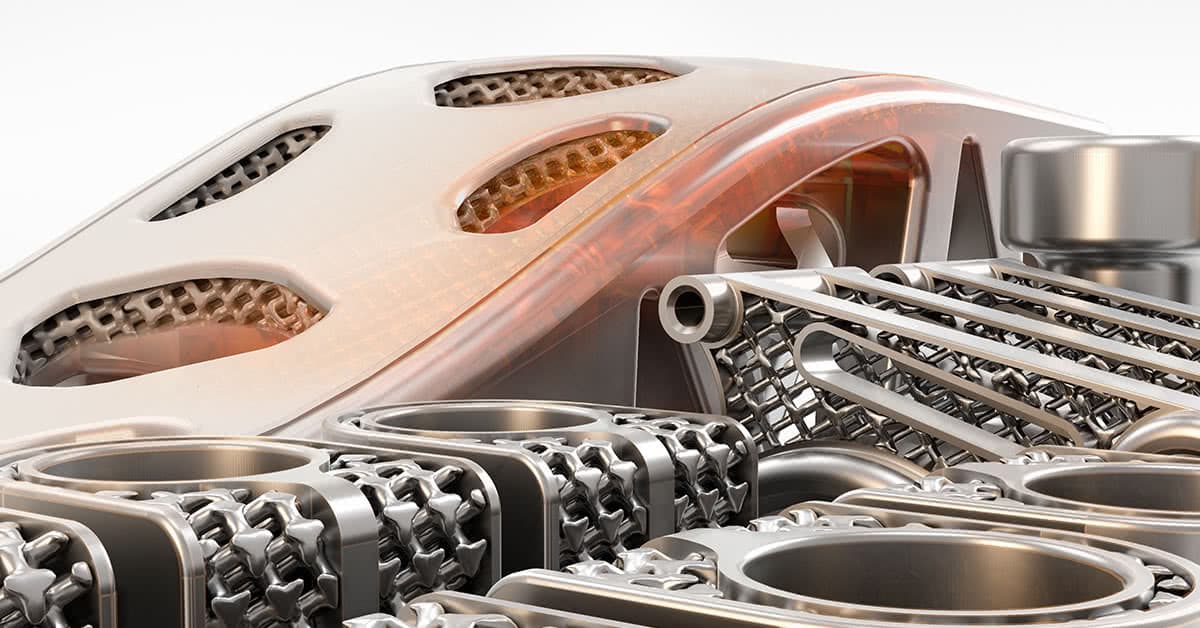
Introduction
The Autodesk Netfabb Simulation Development team is pleased to announce the release of experimentally validated Stainless Steel 316L material properties and a generic PRM. These will be included in the forthcoming 2023.0 version of Netfabb Simulation, but may be downloaded and imported into earlier versions of the software from here. The multi-year validation effort was made possible by numerous industrial and research institute partners including:
- Oak Ridge National Laboratory
- Youngstown State University
- CIMP3D
- OneClick Metal
- Grundfos
- Baker Hughes
The Challenge
Before the development team executed its first test print, the validation of 316L was anticipated to be one of the more difficult materials yet attempted. This stems from three known areas of uncertainty regarding this common steel:
- Laser Absorptivity: Unlike the relatively narrow ranges of laser absorptivity for popular additive metals like Ti-6Al-4V and AlSi10Mg, 316L has shown been experimentally to absorb 25-75% of the impinging heat depending upon the processing conditions1. This is a key simulation input.
- Variable Composition: While other common materials, particularly Nickel Super Alloys, have fairly fixed phase compositions, steels exhibit a wide range of post-forming phases depending upon the rate of cooling experienced2. Variation in phase composition can result in variation in material properties.
- Solid State Phase Transformation: During the validation of Ti-6Al-4V it was found that accounting for the crystallographic strains produced during the solid state phase transformation were vital to modeling the alloy’s additive manufacture with accuracy3. 316L may undergo two solid state phase transformations at differing temperatures2. Depending on the exact composition of the 316L used there can be significant variation in those transformation temperatures2. Due to the uncertainty of phase composition in point 2, this can result a non-homogenous crystallographic transformation, or more simply put, an unknown percentage of 316L will relax an unknown amount of plastic strain at potentially two unknown temperatures.
Methodology
The initial attempts to validate 316L using 3D scans of Powder Bed Fusion manufactured parts failed to result in a single set of properties and laser absorptivity which obtained accurate results across a range of energy densities and build volumes. This motivated in situ Directed Energy Deposition experiments at Oakridge National Laboratory (ORNL)
DED in Situ Validation Experiments
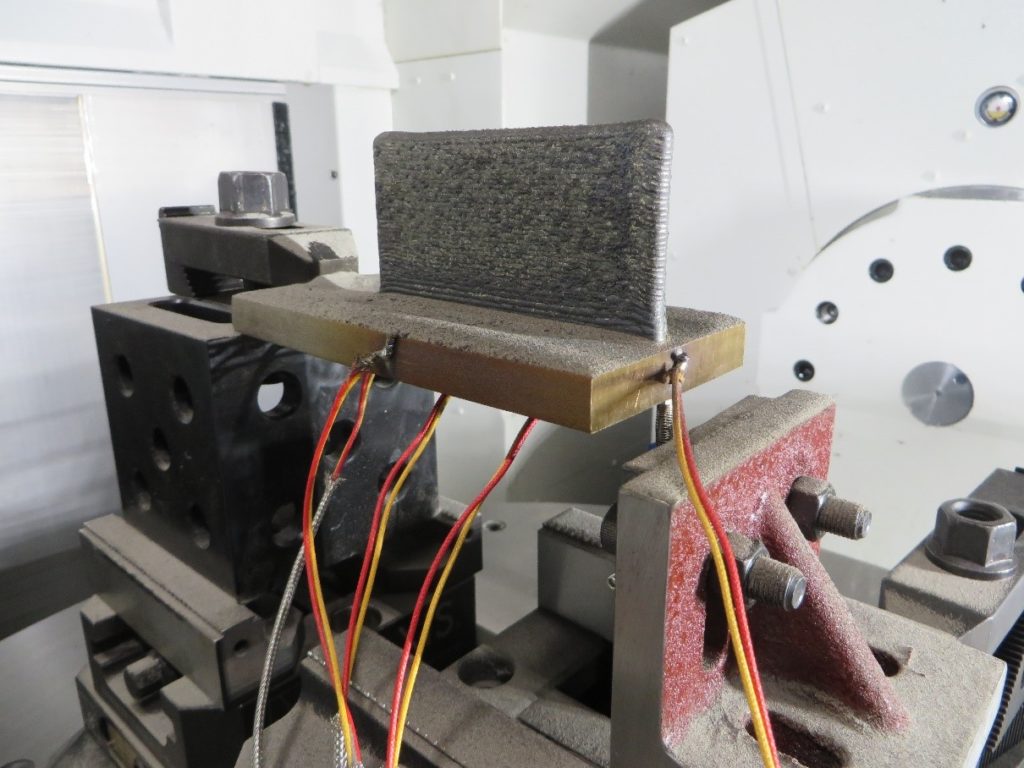
To capture the thermal and mechanical behavior of 316L during additive manufacture, a test rig was created at ORNL following established best practices4. A 316L substrate was fixed on one end, allowing the other to freely deform. Thermocouples were tack-welded onto 5 locations along the base and sides of the substrate. A contact displacement sensor was attached to the free end of the substrate to capture the cyclical distortion. A 100 mm long, 3 bead wide, and 50 mm tall wall was constructed using continuous deposition.
There were three key findings from this work:
1. The thermal absorptivity of 316 L during Additive Manufacture is approximately 36%: Simulation of the first two lines of deposition allows us to examine the thermal behavior before complications due to boundary conditions and extreme thermal non-linearities occur, making it relatively simple to calibrate the absorptivity.
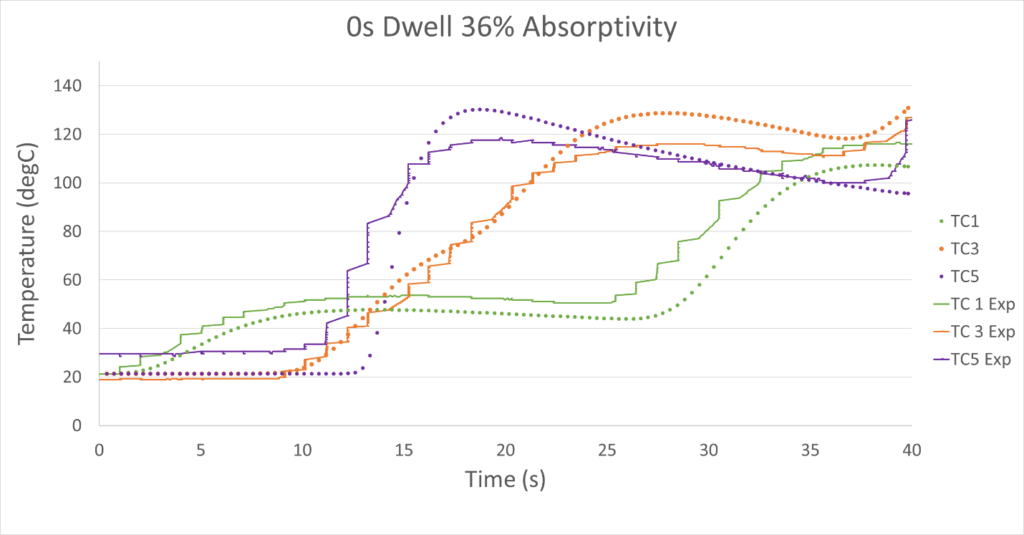
2.Validation of the thermal properties and boundary conditions: The plots of temperatures from the thermocouple readings and thermal simulation show excellent agreement.
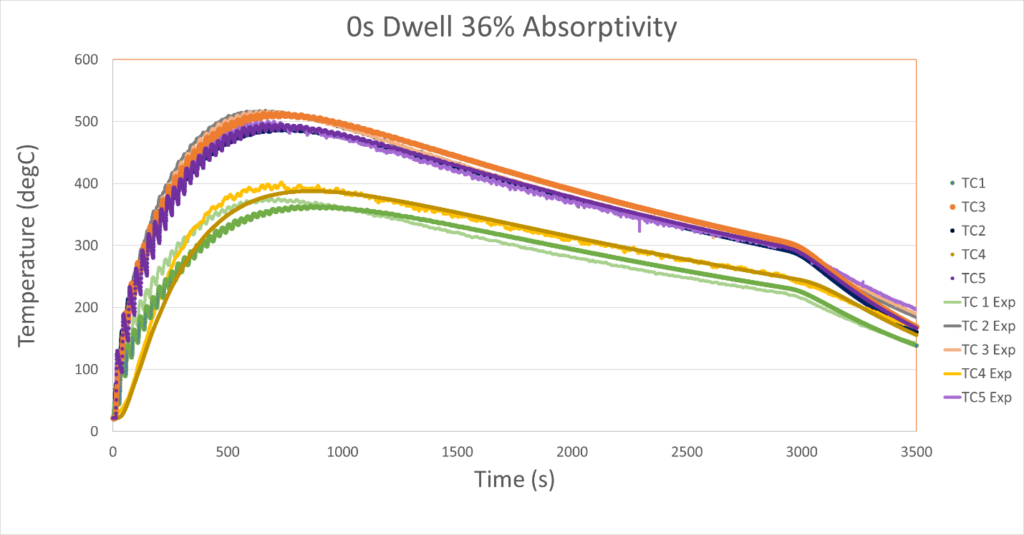
3.The displacement behavior shows the basic material model used was not adequate to accurately simulate 316L: Comparing the simulated displacement of the cantilever substrate with the in situ measurements show a large disparity. The simulation is accurate for the initial portion of the build, then the model begins to overpredict distortion. This was quite similar to the stress relaxation effect observed in Ti-6Al-4V3.
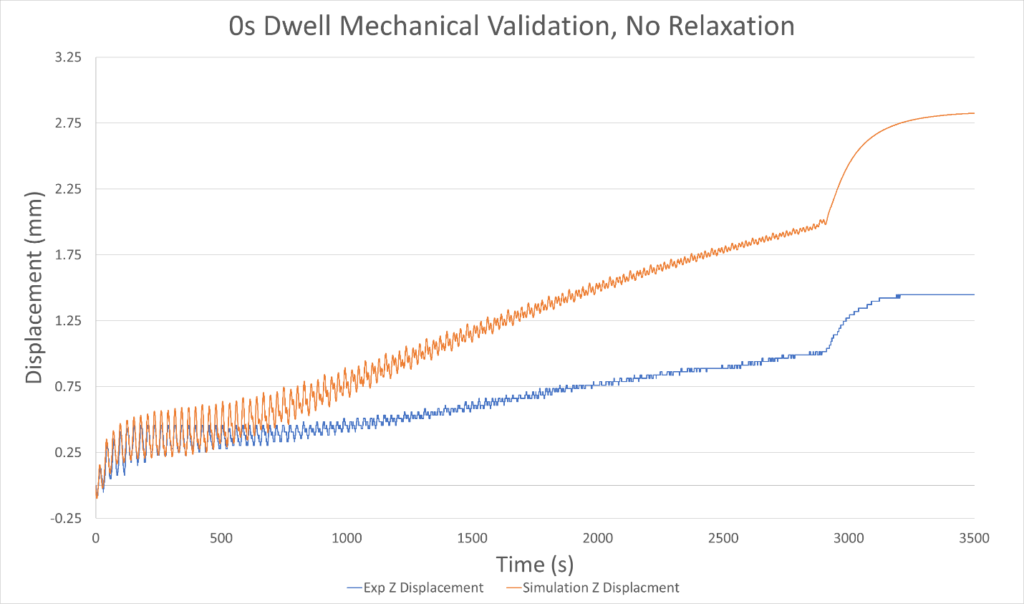
A series of simulations showed good accuracy over the entire distortion history using a stress relaxation temperature of 640 ⁰C:
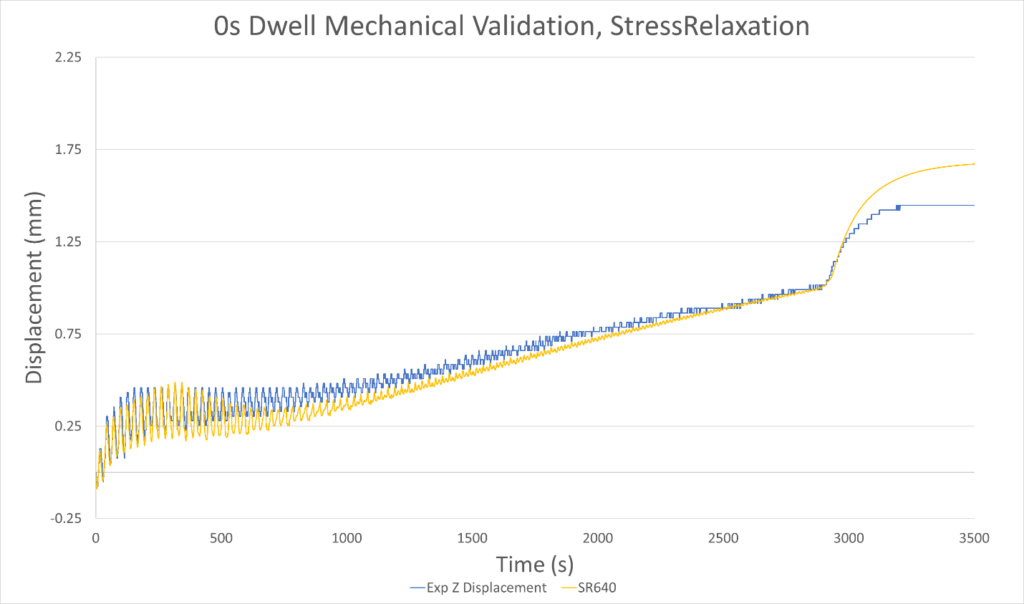
Laser Powder Bed Fusion Validation
With a better understanding of the laser absorptivity and material behavior of 316L, these findings were applied to part scale simulations across a range of geometries and energy densities.
Youngstown State University Square Canonical
The Square Canonical shape was designed by GE Global Research to validate additive simulation tools. With thin exterior walls met by a very thick section growing from the interior, this roughly 1 inch (25 mm) cube geometry can exhibit visible distortion. The YSU Canonical peak distortion is -0.25 mm while the simulation predicted -0.16, yielding an acceptable accuracy of -36% error.
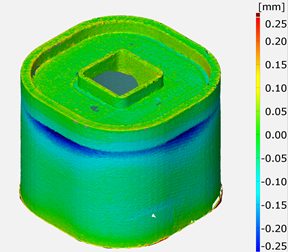
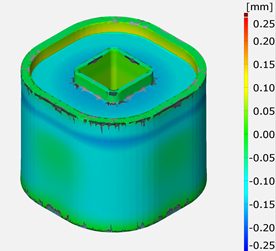
CIMP3D Hollow Airfoil
The Hollow Airfoil is another small part which can experience dramatic distortion during production. Here the printed 316L Airfoil showed -0.89 mm while the simulation predicts a peak of 1.21 mm, an error of +36%.
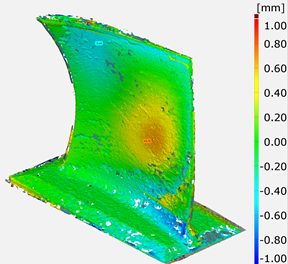
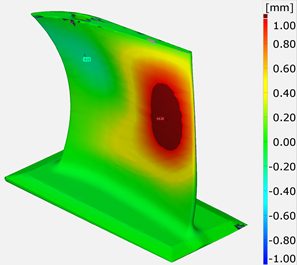
OneClick Impeller
Initial simulations using the OneClick system indicated the laser absorptivity obtained from the DED work was far too low. A calibration study against the canonical part resulted in an absorptivity value of 52% for 316L in the OneClick machines. The Impeller, a larger part 65 mm across, distorted a maximum of -0.80 mm while the simulation gave a peak distortion value of -0.79 mm, an error of just 1.3%.
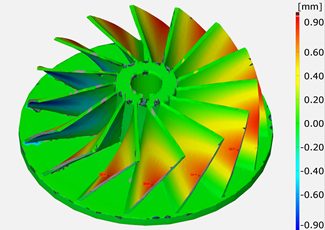
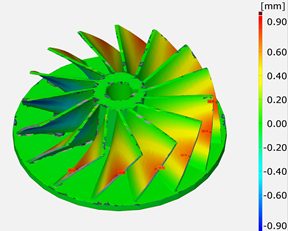
Conclusion
By attaining in situ measurements of the thermo-mechanical behavior of 316L Stainless Steel via DED experimental measurements, the Autodesk Netfabb Simulation development team was able to create a set of material properties that apply to a wide range of energy densities and geometries. A generic PRM is now available for generalized powder bed fusion simulation. Custom PRMs can be generated from the resulting material data set based upon users’ exact processing parameters. Due to the variability of 316L laser absorptivity, users may want to conduct their own absorptivity studies to fine tune their simulations.
References
- Trapp, Johannes, et al. “In situ absorptivity measurements of metallic powders during laser powder-bed fusion additive manufacturing.” Applied Materials Today 9 (2017): 341-349.
- Krauss, George. Steels: processing, structure, and performance. Asm International, 2015.
- Denlinger, Erik R., et al. “Effect of inter-layer dwell time on distortion and residual stress in additive manufacturing of titanium and nickel alloys.” Journal of Materials Processing Technology 215 (2015): 123-131.
- Gouge, Michael, and Pan Michaleris. “An introduction to additive manufacturing processes and their modeling challenges.” Thermo-mechanical modeling of additive manufacturing. Butterworth-Heinemann, 2018. 3-18.