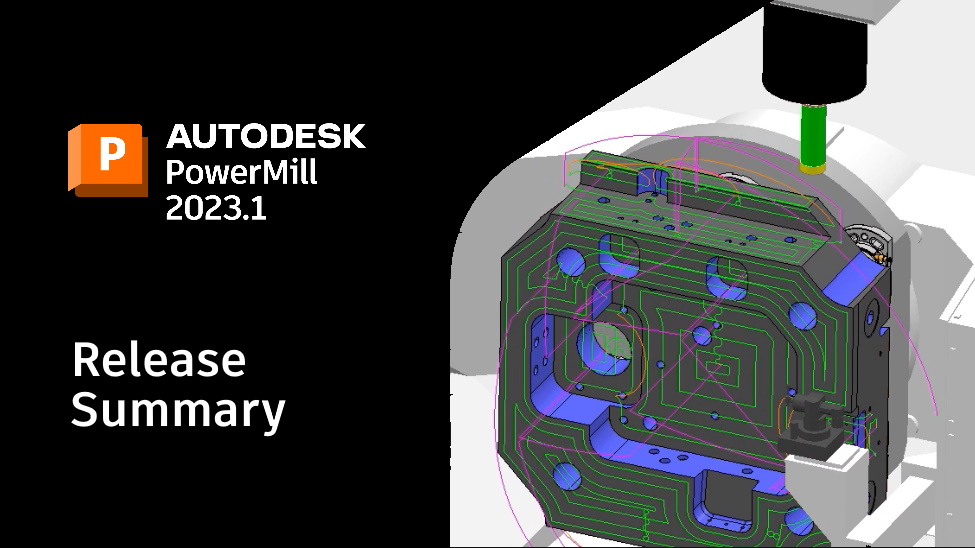
Automation has been a hot topic in CAM software for years. Success lies in replacing manual tasks with automated workflows that allow best practices to be defined, shared, and re-used across parts and teams. Thankfully, the latest update to Fusion 360 with PowerMill (version 2023.1) includes two completely new machining strategies with automation top of mind, allowing some of the most common CAM programming workflows to be streamlined.
PowerMill 2023.1 – Customer Release: Dec 5, 2022
In this article, we will cover the major release highlights as well as provide links to watch more detailed tutorial videos (for those of you wanting to see the improvements in action).
NEW: Inclined Flat Finishing
Kicking off with flat surfaces. No matter whether you’re making a simple aerospace bracket or a super complex mold tool, the chances are you’ll be machining a mix of curved and planar faces. In most cases, the flat regions are typically best machined using the end of a flat-bottomed tool – like an end mill or tip radiused tool – as this allows the use of larger stepovers for shorter cycle times.
Programming flat faces is simple when all the faces are aligned the same way – but it gets way more involved if there are many flat faces, all at different angles. Programming all these faces can quickly become an arduous task and will likely involve the creation of multiple workplanes and toolpaths for each flat.
Thankfully, PowerMill 2023.1 includes a solution – called “Inclined Flat Finishing”. As the name suggests, this completely new toolpath automates the machining of these angled planar surfaces by finding all flat faces within a user-defined range, then machining them with a single, 5-axis toolpath. As you’d expect, a range of advanced options allows fine control over the exact style and extent of machining.
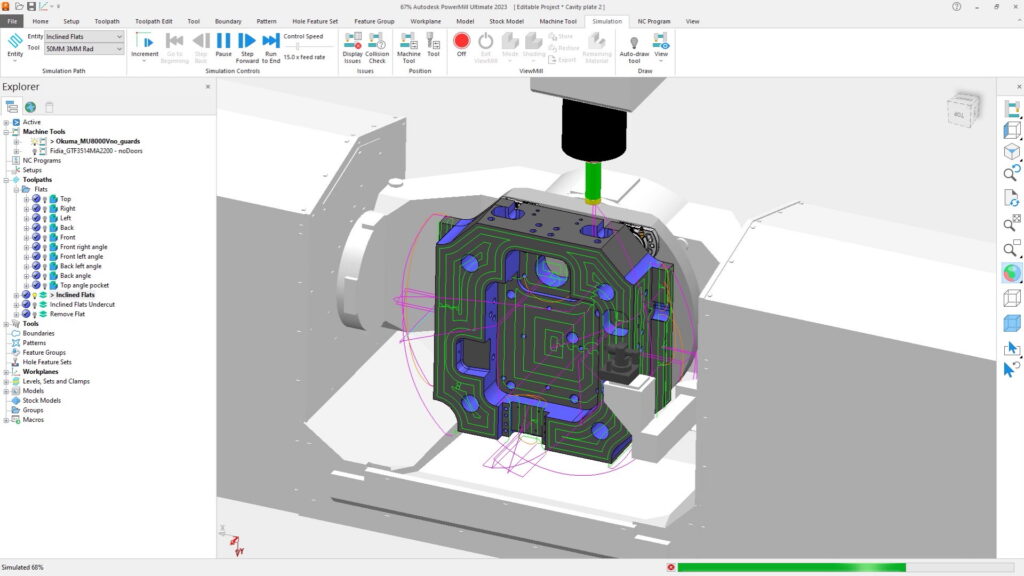
As you’ll see from this tutorial video, the potential savings in terms of CAM programming times could be huge, as well as greatly reducing the potential for human error. And for those using 3+2 machines that can’t move all 5 axes simultaneously, check out this forum post to access a handy plug-in that uses the same underlying code to create separate 3+2 toolpaths to machine all inclined flats on your machines.
NEW: Rest Finishing
Our next update relates to rest machining (this being the ability to find stock left unmachined by previous operations and remove it). Rest machining isn’t new to PowerMill, in fact, there are several options already available.
- Pencil Finishing
- Description: This strategy produces toolpath passes that follow the shape of the corner being machined resulting in visually pleasing surface finishes. Users can choose to create single or multiple passes with the latter being best suited for the removal of larger amounts of material.
- Known limitations: This toolpath can sometimes fail to identify unmachined stock in certain cases (for example at the ends of fillets where the radius fades to nothing, or where multiple fillets intersect each other). This can mean the CAM programmer needs to create additional toolpaths or rely on manual polishing after machining.
- Corner Finishing
- Description: This toolpath uses a similar material detection process as Pencil Finishing but provides additional options to machine steep and shallow areas using different approaches. Users can choose to machine shallow regions with “along” toolpath motion, and steep areas with “across” motion to manage stock engagement and avoid tool breakages.
- Known limitations: Much like Pencil Finishing, this toolpath can also fail to identify unmachined stock in certain cases (such as the ends of fillets or intersecting fillets).
- Rest Boundaries
- Description: Rest boundaries can accurately detect unmachined stock based on previous machining operations or cutting tool sizes. The process generates one or more 3D outlines that can be used to constrain toolpaths to machine within specific regions. Rest boundaries are more accurate than both Pencil and Corner Finishing and do not suffer from the same accuracy issues mentioned previously.
- Known limitations: While rest boundaries can accurately detect unmachined stock, there is no single toolpath that can be used to efficiently remove the material once it has been found. Instead, the CAM programmer will need to spend additional time determining the best strategies to use for each of the regions defined within the boundary.
While there are three basic strategies in PowerMill, it’s not always obvious which one to use for any given part or project. Thankfully, PowerMill 2023.1 includes a completely new Rest Finishing strategy that combines the best aspects of pencil finishing, corner finishing, and rest boundaries – to accurately find unmachined stock and remove it safely and effectively.
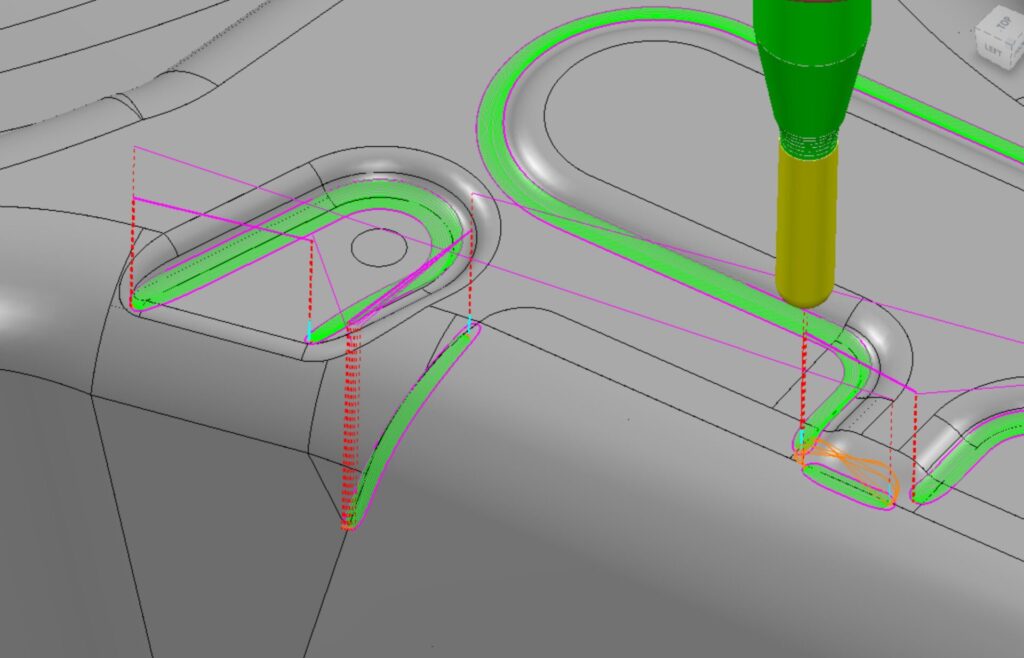
The new Rest Finishing strategy identifies rest areas from a reference tool in the same way that PowerMill rest boundaries would, then machines these areas using a steep and shallow type of toolpath, with a range of options, including the ability to use 5-axis machine motion with automatic collision avoidance.
To learn more about the new Rest Finishing strategy, watch this tutorial video.
ENHANCED: More consistent collision avoidance
First released in PowerMill 2019, automatic collision avoidance employs 5-axis machine motion to avoid collisions and near-misses that might involve the cutting tool assembly and target CAD model. In the years since this was first released, we’ve focused on reliability to ensure 5-axis machine motion is smooth and predictable.
These improvements continue in PowerMill 2023.1 with more consistent toolaxis tilting on neighboring toolpath passes, as well as improved consistency of tilting when machining symmetrical parts. By orienting the cutting tool to the workpiece in a more consistent way, cutting forces are also maintained which should result in better levels of surface finishes. It can also help reduce the likelihood of defects appearing due to small inaccuracies that may exist in the setup of your CNC machine. Ultimately, this should help improve part quality and reduce the need for manual polishing.
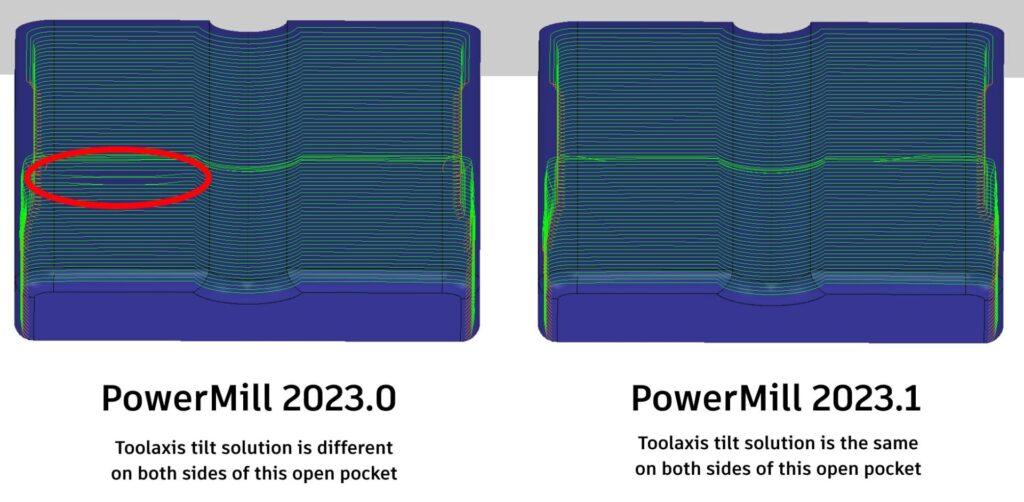
To learn more about the changes to collision avoidance, watch this tutorial video.
ENHANCED: Setup connection moves
Also added in PowerMill 2019, Setups help simplify CAM programming by allowing CAD models, fixtures, datums, and other common settings to be defined and managed within a single entity in PowerMill – called a “Setup”. In subsequent releases, Setups have been enhanced to provide more capability – and this continues in the 2023.1 release with the ability to define and control connection moves.
Safe areas, clearance heights, as well as start and end points, can all now be defined and applied to toolpaths within a setup. If these settings are changed, any toolpaths contained within the setup will automatically be updated too – although it’s worth noting a tick box option allows individual toolpaths to be changed if needed.
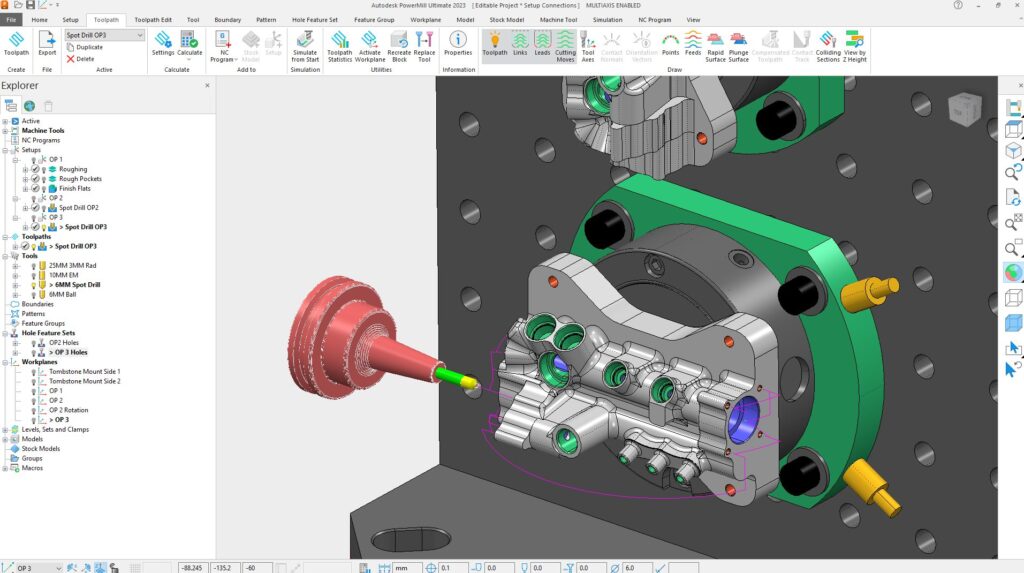
Another small but significant improvement to Setups changes behavior whenever a toolpath is dragged into or out of a setup. Now, if this happens, the toolpath will be invalidated. This is to provide additional safety, as it’s likely the settings relating to clamps and stock will be different and will require the toolpath to be recalculated.
To learn more about Setup connection moves, watch this tutorial video.
ENHANCED: Performance matters, now and always
Continuing a theme that has been running for the last few releases, the PowerMill development team has worked to identify areas of the code where performance could be improved. In this specific release, multiple speed-ups have been made that impact:
- Faster calculation times for flat toolpaths that explicitly process (for example “machine down to”, or “ignore” flat surfaces). This includes “Flat Finishing” and “Area Clearance” toolpaths.
- Post-processing of NC programs that contain hundreds of toolpaths should be faster in PowerMill 2023.1 than in previous releases. In one customer account, the time taken to post-process a single NC program containing 1,641 toolpaths has reduced from 8hrs to 23mins – a saving of more than 90%. We’re continuing to work in this area of PowerMill’s code and hope to provide further speed improvements in future releases.
- Faster browser, meaning the time taken to drag large numbers of entities from one place to another should be much faster. In one test, the time taken to drag 168 toolpaths in the browser was reduced from 2mins to 8 seconds (a saving of more than 90%).
- Faster saving of projects with many workplanes. In one test, the time taken to save a project containing around 10k workplaces was reduced from 15mins to 6mins, a saving of 60%.
It’s worth noting that the exact amount of time saved will vary based on the types of parts being machined, the strategy being used, and the specification of your PC.
Additional, notable enhancements
While we have just covered our favorite updates in the 2023.1 release there are others that deserve a mention.
- Reduce the likelihood of whisper cuts appearing in flat toolpaths
- Boundaries belonging to toolpaths within Setups now correctly respect clamp settings.
- Improved performance of the toolpath strategy dialog.
- Enhanced user experience when accessing a remote path that is blocked.
- Remote paths inside MTD files are no longer blocked if “Restrict remote paths” is switched off.
Want to learn more?
So, there it is. The top improvements in Fusion 360 with PowerMill (version 2023.1) with a list of honorable mentions. There are more improvements, and you can read about them all in the official release notes at https://help.autodesk.com/view/PWRM/2023/ENU/?contextId=PWRM_RELEASE_NOTES.
If you want to take a deeper dive into this release, why not watch this short release highlights presentation.
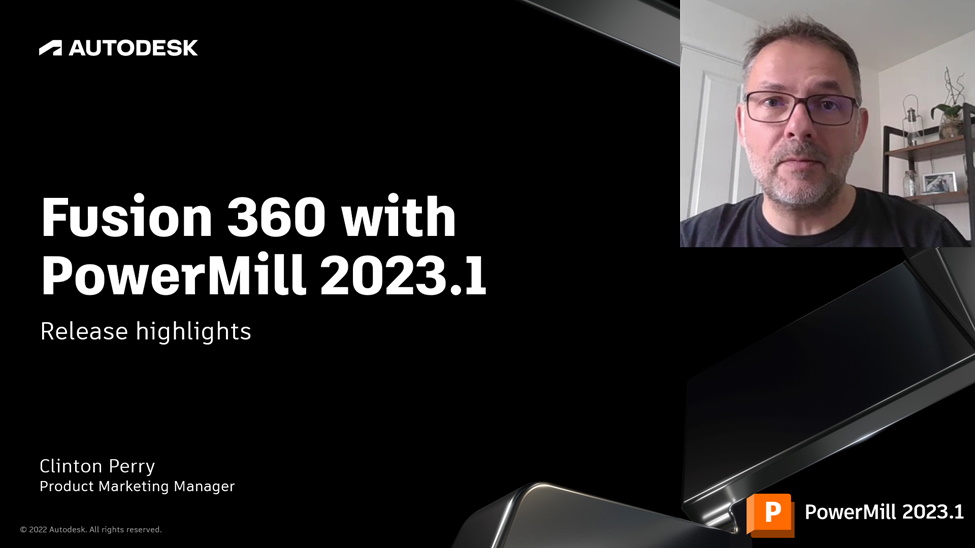
Ready to start using PowerMill 2023.1?
ARE YOU AN EXISTING CUSTOMER?
Eligible customers with an active subscription or maintenance agreement will be able to download the latest release starting Dec 5, 2022. Download using the Autodesk Desktop App or by logging into your Autodesk Account.
WANT TO TRY FUSION 360 WITH POWERMILL FREE FOR 30 DAYS?
New to PowerMill and want to see how it can help you solve your toughest CNC machining challenges? Try for yourself, completey free for 30-days by visiting www.autodesk.com/products/powermil/free-trial.
WANT TO SPEAK WITH AN EXPERT?
Visit our Services Marketplace to contact an approved Autodesk technical sales representative in your local area to discuss your business needs.