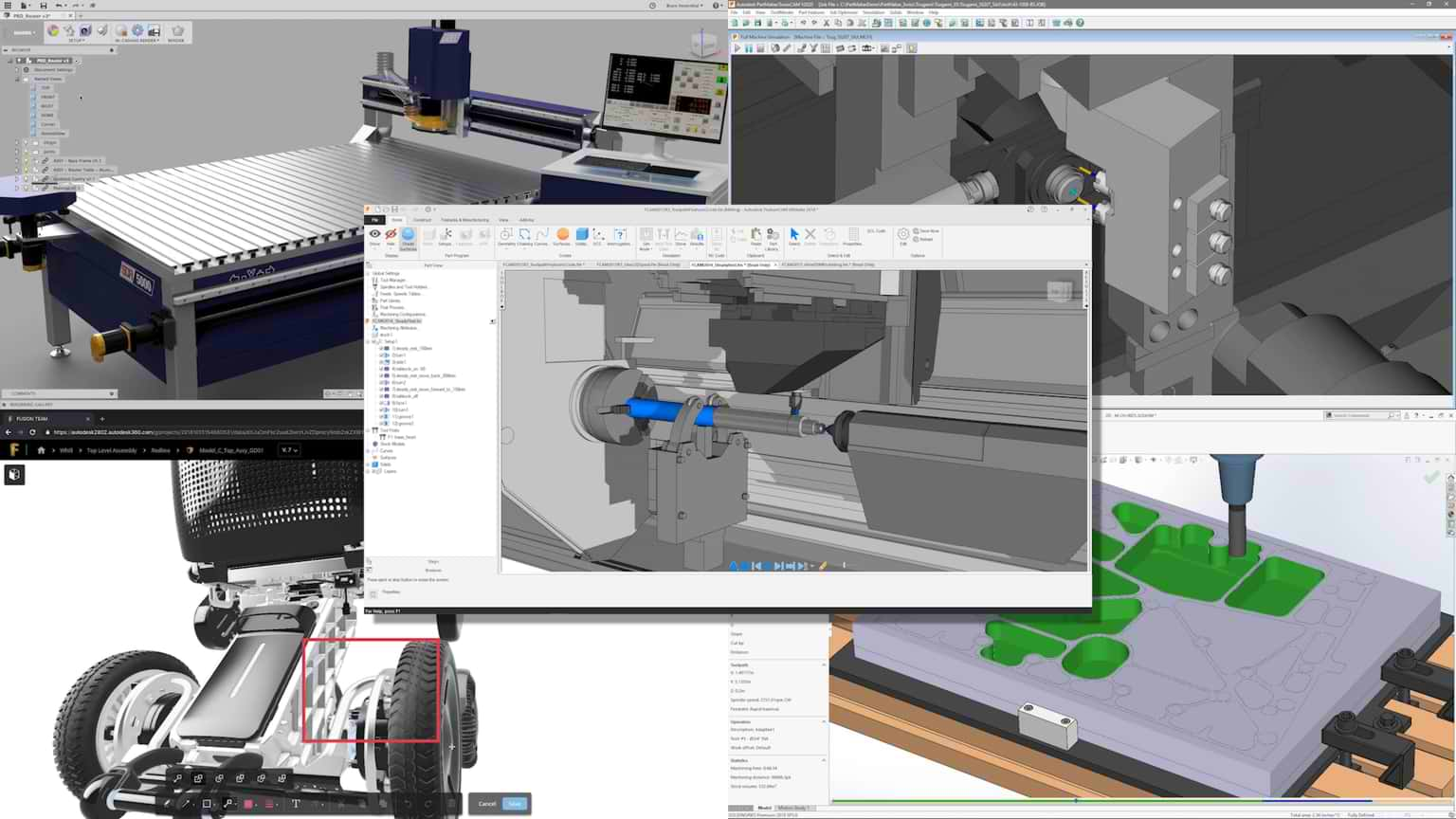
Delivering products on time is always the top priority. But many of the variables that affect lead time are out of your hands. That makes it really important for manufacturers to find every possible way to minimize lead time through the factors that are under your direct control.
Reducing part programming time can deliver a huge payoff in this respect. That is why Autodesk developed Fusion 360 with FeatureCAM® software. The FeatureCAM 2021 release is an all-in-one solution that combines:
- FeatureCAM Ultimate for CAM automation
- Fusion 360 for cloud-based product innovation
- PartMaker for precision control of Swiss-type lathes
- Fusion Team for communication and collaboration
- HSMWorks for embedded CAM in SOLIDWORKS®
Together, these offerings give you a single, fully integrated product development platform, a modernized collaboration environment, and multiple ways to reduce programming times while increasing consistency.
Shorten the time between design and NC code
Fusion 360 with FeatureCAM uses CAM automation to reduce programming times and produce consistent results for a wide range of CNC machines. Comprehensive machine support means you can use a single, familiar interface for all your CNC applications and get more productivity out of 3- to 5-axis mills, lathes, turn-mill centers, Swiss lathes, and wire EDMs. This also makes it easier to standardize best practices throughout the shop and promote repeatability among all operators.
Here are five ways Fusion 360 with FeatureCAM helps you minimize programming time.
1. Feature recognition. Feature recognition helps you quickly identify and create machinable features from the solid model, including holes, bosses, and pockets. This is done automatically by scanning the model and generating a list of identified features. The software simultaneously captures all the data required to start machining, which reduces repetitive tasks.
2. Creating fixtures. Knowing how a part will be held is critical for successful programming. Import an assembly model or create a model from scratch within Fusion 360, then create relationships between model elements through joints and motions, and finally generate an accurate assembly and export it back to FeatureCAM Ultimate for automatic feature recognition.
3. Accurate tool holders. In the same way, you can use Fusion 360 to create accurate tooling models and then bring them back into FeatureCAM as tool holders. This helps you quickly create more accurate machine simulations and provide a better representation of the machining environment. It’s especially important for high-value parts or long production runs.
4. Easier collaboration. Fusion Team lets you review, comment and markup designs in the cloud, allowing manufacturing teams to give information to design teams about changes required for successful manufacturing. Design modifications can then be made and sent back to the manufacturer for final digital verification and simulation before being sent to the machine for production. In other words, you get more consistent results and fewer iterations.
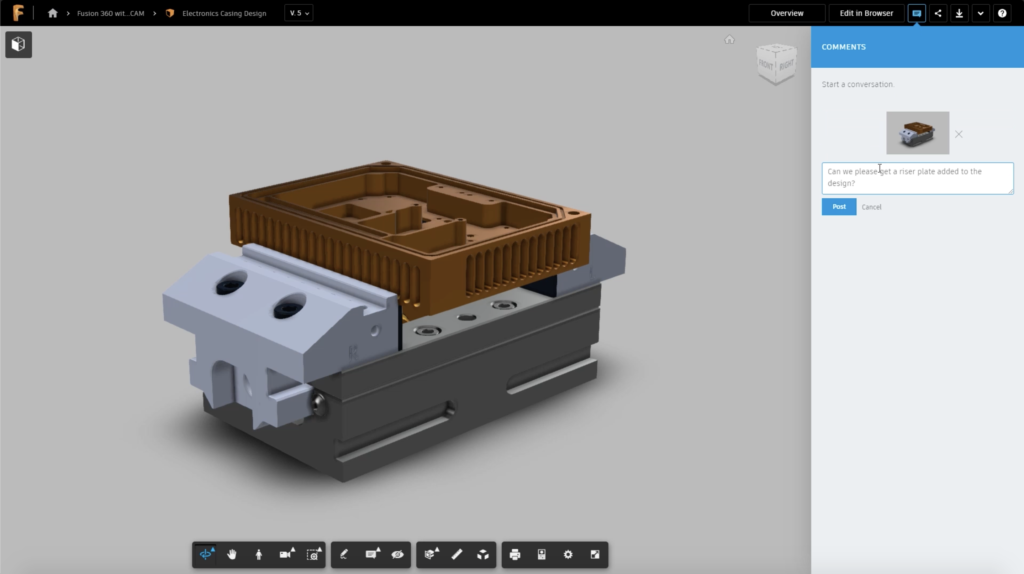
5. Simulation. Simulation tools to visualize programming within the machining envelope help ensure parts can be made safely and efficiently—before they go to the machine. Toolpaths can be viewed individually or fully. And a dynamic 3D model of the machining processes highlights deviations between the programmed part and the nominal design. It also helps you spot potential collisions that could raise costs or cause downtime, all of which saves programming (and reprogramming) time.
Keep in mind, reducing programming time is just one way Fusion 360 with FeatureCAM can help in your shop. To learn more about Fusion 360 with FeatureCAM go to https://www.autodesk.com/products/featurecam/overview
