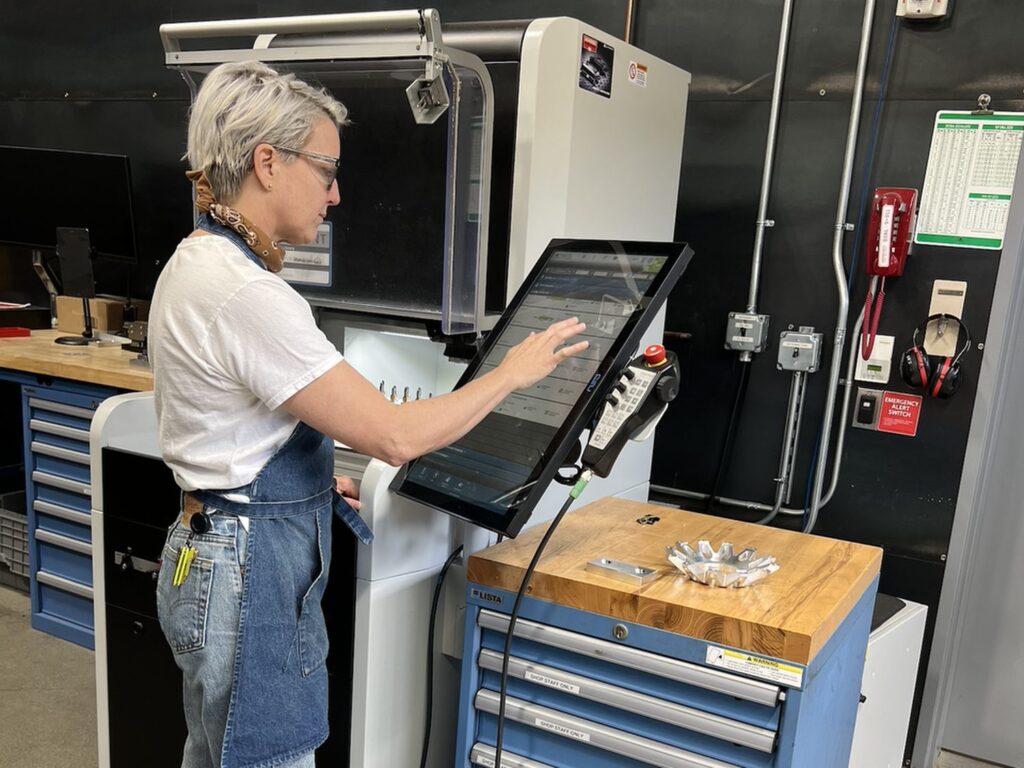
Autodesk Research has a mission to explore new possibilities and the technologies that enable them while also de-risking opportunities and unlocking the potential for our business and customers, all in support of Autodesk’s larger mission.
As part of Autodesk Research, I’m the manager of the Autodesk Technology Center Workshop in San Francisco. In my role, I oversee a group of subject-matter experts across various technical disciplines, such as additive manufacturing or robotics, and I collaborate with the North American Technology Center teams in Boston and Toronto. Fostering an environment where our team members are well-versed on all our equipment, maximizing their contribution to Autodesk, and nurturing cutting-edge research is a high priority for me.
Driving innovation and collaboration
We are using Autodesk software every day – it’s essential to the success of our operation. We maintain a close feedback loop with the Fusion 360 and
Product Development & Manufacturing Solutions (PDMS) teams, as well as the machine manufacturers, to help enhance our software. Practical experiments validate digital workflows, revealing deeper insights and the intricacies of these powerful machines. We cultivate strategic thinking and knowledge about our equipment that provides valuable feedback and improves our tools.
It’s important to empower the company’s researchers and residents to use our shops safely and effectively; to make well-informed decisions regarding materials, machines, and software. Our Technical Environments team is dedicated to nurturing this growth. We’ve created a safe and well-equipped workshop with a highly trained, knowledgeable team who maintain the equipment and collaborate with the researchers.
Transforming workspaces and driving cutting-edge projects
I’ve been able to work on many exciting projects over the course of my nine-plus years at Autodesk. In the past 18 months, I led two projects, tackling some complex technical challenges. Most recently, I collaborated with the team researching adaptive product assembly to create more flexible robotic automation for manufacturing by converting a mailroom into an advanced robotic workspace. The research team is activating this new space and exploring innovations along with members of my team.
Last year, I worked on a large project that involved the complete overhaul of our CNC, project assembly, and wood shops. We removed legacy equipment that no longer aligned with our research priorities. Bringing in new equipment, in turn, built new relationships with machine manufacturers. In our updated workshop, we can demonstrate to small and mid-sized manufacturers how they can effectively integrate equipment and data-enabled workflows into their own shops. This ambitious project created opportunities with several leading equipment manufacturers.
A supportive culture of learning
Autodesk is such a unique place to work. I value Autodesk’s Culture Code and appreciate how the company strives to create an environment where employees feel seen and respected. During the COVID pandemic, our leadership was proactive, empathetic, and considered employees’ well-being. They helped managers lead and serve their teams during those unusual circumstances. There are so many resources for managers to professionally develop themselves and their teams. I appreciate that Autodesk takes a holistic approach as a company for managers and employees alike.
If you’re interested in a role like mine, my advice would be to ask questions. Find the courage to ask questions about fields you’re unfamiliar with, and increase your knowledge through classes, reading, and hands-on work. I believe this is a great driver for personal and professional development. By working with experts, enlisting the help of mentors, or becoming a mentor yourself, you can also create energy and inspiration. You need this to pursue new things you’re interested in trying. Expertise takes time. It requires curiosity and patience. The path can be circuitous.
Learn more about Autodesk Research here.