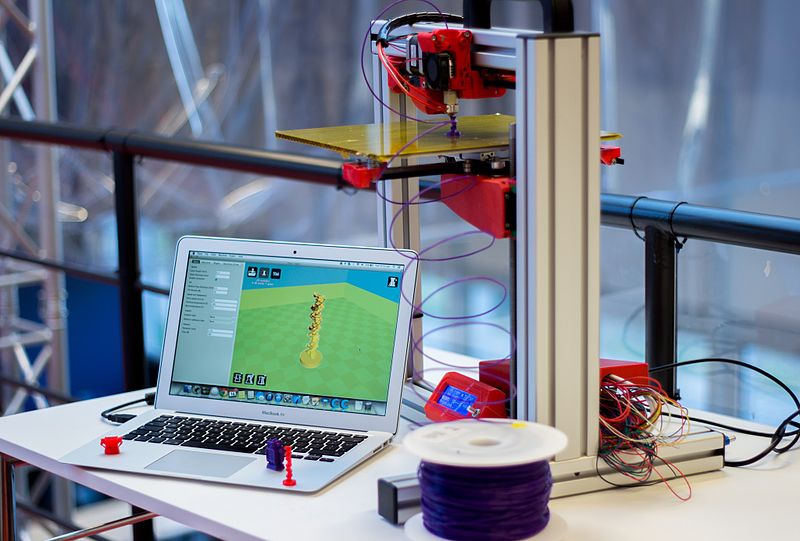
Additive Manufacturing along with its subset 3D printing have been the talk of engineering and pop culture for some time now. We are at a point where it is safe to say that additive manufacturing is here to stay, but what does the future hold for this innovative technology?
The shrinking entry costs for the additive manufacturing industry have allowed college students, hobbyists, and small engineering firms to experiment with their design to physical manufacturing skills. Relatively affordable 3D printers are a fairly new thing. Just 5 years ago, your entry price into the 3D printing realm was well over 1000 dollars. Now, it can be as low as $200.
3D printing isn’t all that the additive manufacturing world holds, but it certainly is the prime aspect of the industry held at the forefront of media coverage. In 2016, 3D printing surpassed $5.1 billion as an industry whole, according to Wohler’s Report. Just last year, there were 278,000 desktop 3D printers sold to consumers, an incredible number if you compare it to the number of other desktop manufacturing machines sold.
When looking at 3D printing, it holds a unique aspect that other manufacturing techniques don’t: it’s mesmerizing but relatively easy to the average person. For much of modern history, we can look to other manufacturing techniques like CNC milling, lathing, woodworking, etc. These are all very essential manufacturing processes, but their cost of entry has historically been high, not to mention the relatively long time it takes users to build up skills in these areas.
For 3D printing, and I’ve seen it firsthand, it is a technology that is captivating enough that the everyday man, child, woman, or family wants to get involved. Not only that, but the interfaces are simple enough that these inexperienced demographics can and do get involved. 3D printing could inspire another generation of makers, but only time will tell for that prediction.
So, we understand that recreational or hobbyist 3D printing is going to continue to rise, but what about the engineering and industrial uses of AM technologies?
The additive manufacturing industry grew by $1 billion just last year, 25.9% compared to 2015, according to Forbes. While the consumer market is growing, Forbes suggests that much of this growth is due to how AM is revolutionizing start up’s manufacturing and design capabilities. For small run production, 3D manufacturing can be accomplished at a lower cost per part than other manufacturing techniques. However, 3D printing isn’t just a competitor to injection molding, it is also a significant driver for its growth. Many companies are using 3D printing to create quick molds for injection applications to keep from having to iterate with more expensive metal designs.
There’s another study that gives us some insight into the growth of the industry as well. Researchers from Michigan Technological University, according to Audiotech, studied the cost of 20 top household items. They compared the average cost of buying such items to 3D printing those items. They found that it would cost anywhere from $312 to $1,944 to buy the items, but only $18 if you printed them. It would also be possible to print all 20 items within a weekend, further driving the cost savings with AM home.
Growth of the industry will likely continue further into the hobbyist and commercial sector, but the largest growth facilitators will be the grander uses for the technology in more industrial applications. For additive, the future is being laid out layer by layer, and it doesn’t look like it is stopping anytime soon.
Image: [1]