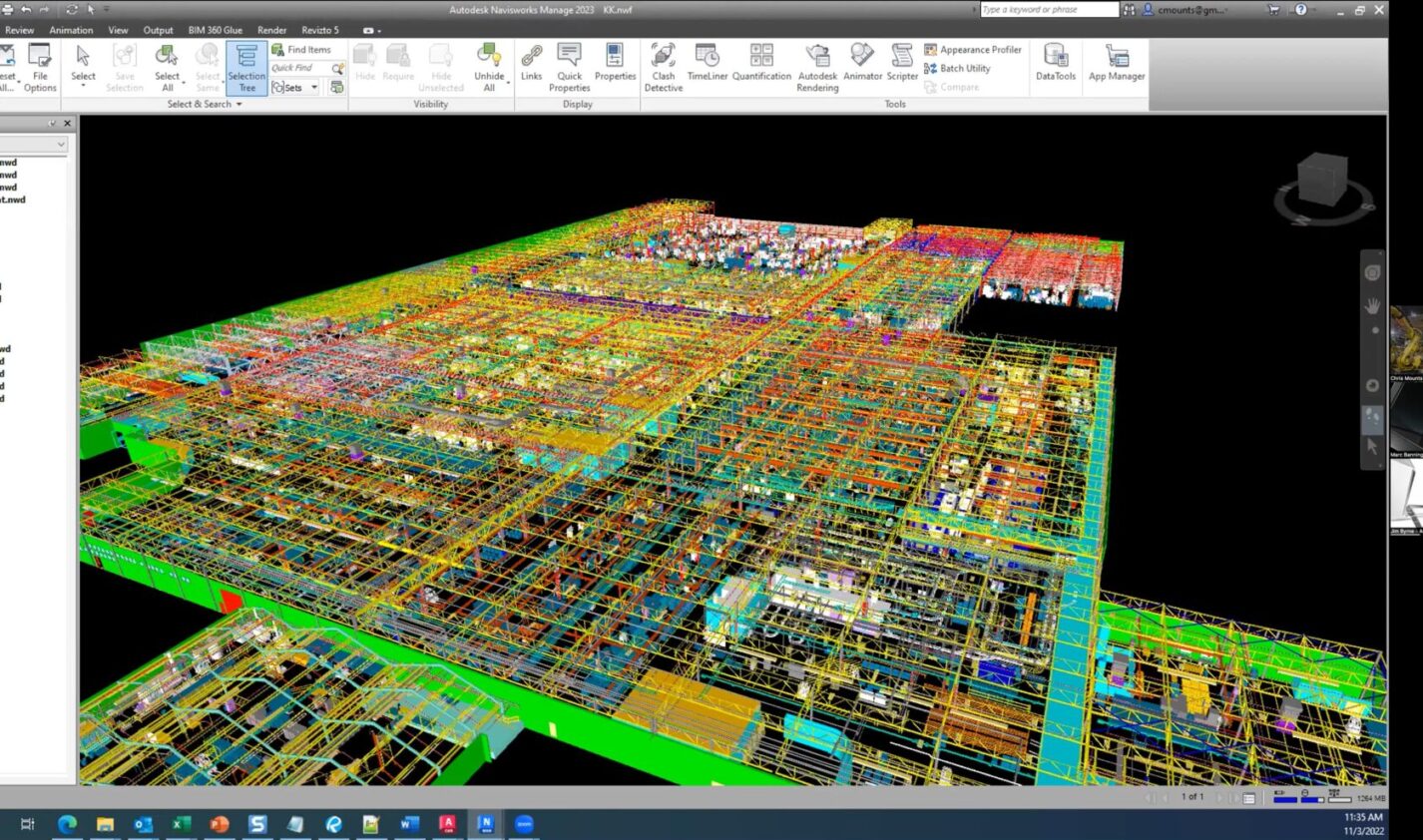
New webinar shows how integrated factory modeling saves money and protects schedules
Factories change constantly, and these changes involve a range of teams using disparate tools. The stakes are high because any error could put the project’s budget and schedule at risk. Digitalization is paving the way for a more streamlined, collaborative, and efficient approach.
We explored this situation in depth in a recent webinar, available now on-demand. Outpace & Outperform: Proven Strategies for Successful Factory Projects features insights from Chris Mounts, Director of Laser Scanning and CAD Services at Production Modeling Corporation (PMC). Chris has more than 20 years of experience designing, scanning, and modeling factories for a wide range of industries, including automotive, aerospace, heavy equipment, and more.
Chris is joined in the webinar by Marc Banning—who has 25 years of experience providing strategic manufacturing consulting for the automotive industry, and Jim Byrne—who has spent more than 24 years working on technologies for simulation and factory planning.
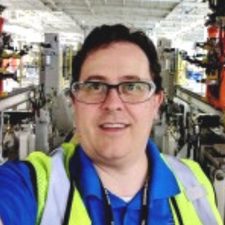
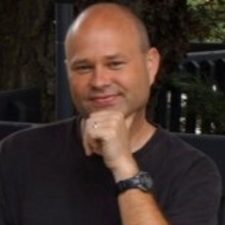
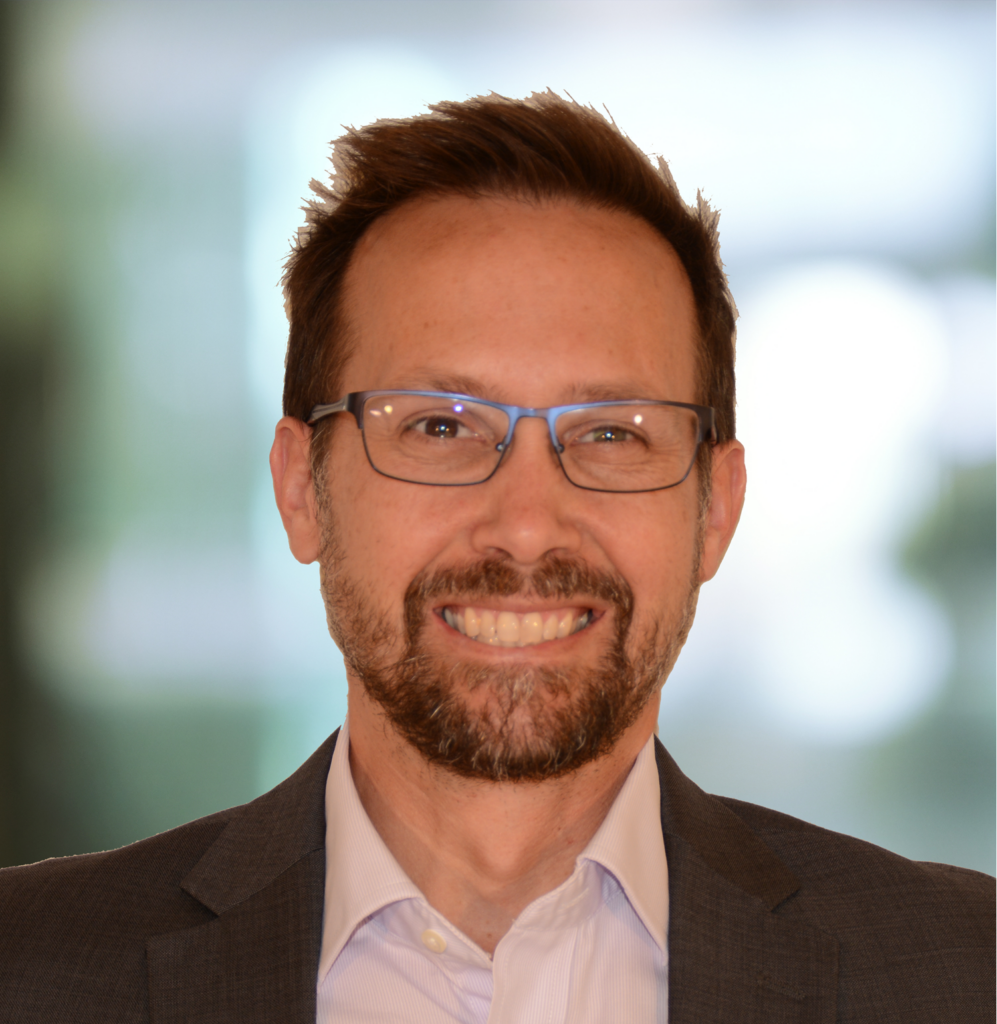
Here are 3 key takeaways from the webinar.
1. Integrated factory modeling bridges silos with a trusted data source.
The goal of integrated factory modeling is to shift from disparate systems and inconsistent data to a common digital 3D factory environment that allows teams to collaborate confidently and intuitively. Integrated factory modeling provides a “single source of truth” that can help multiple manufacturing disciplines execute projects with fewer errors, lower costs, and higher efficiency.
2. Potential cost savings with integrated factory modeling are significant.
Typical projects allow between 20% to 50% in construction cost overages when adding production lines, products, or processing techniques to an existing factory. Integrated factory modeling can reduce these cost overages to nearly zero by helping you catch potential conflicts and mistakes before they happen. For typical projects, this represents millions in savings.
3. You can start small and still see big results with integrated factory modeling.
You don’t have to overhaul your entire production planning process to start digitalizing your factory. The first step is bringing layouts into 3D. From there, you can employ automation to free up time for value-add work, combine layouts with BIM data to create a high-fidelity virtual representation of the entire facility, and unify the factory lifecycle around a common data source.
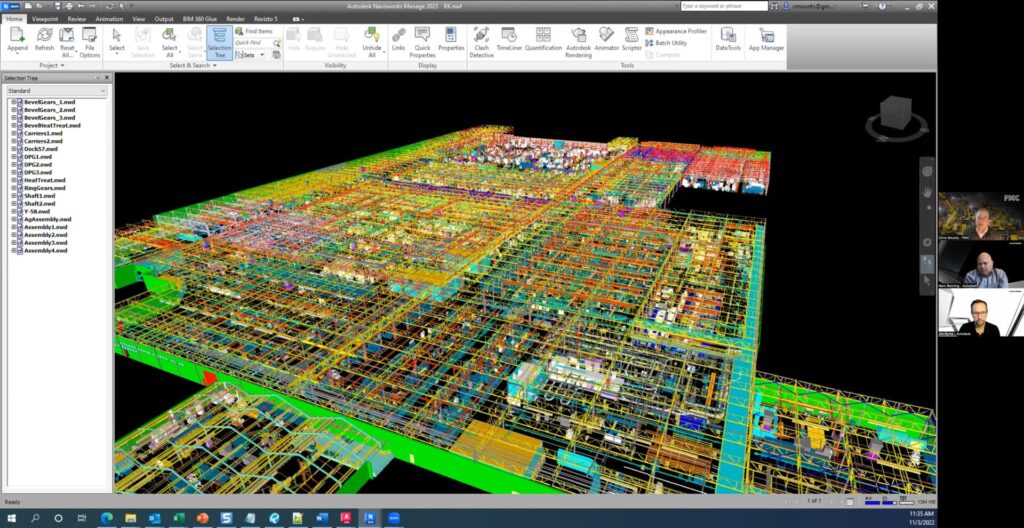
Watch the full webinar here and learn more about the value of integrated factory modeling.