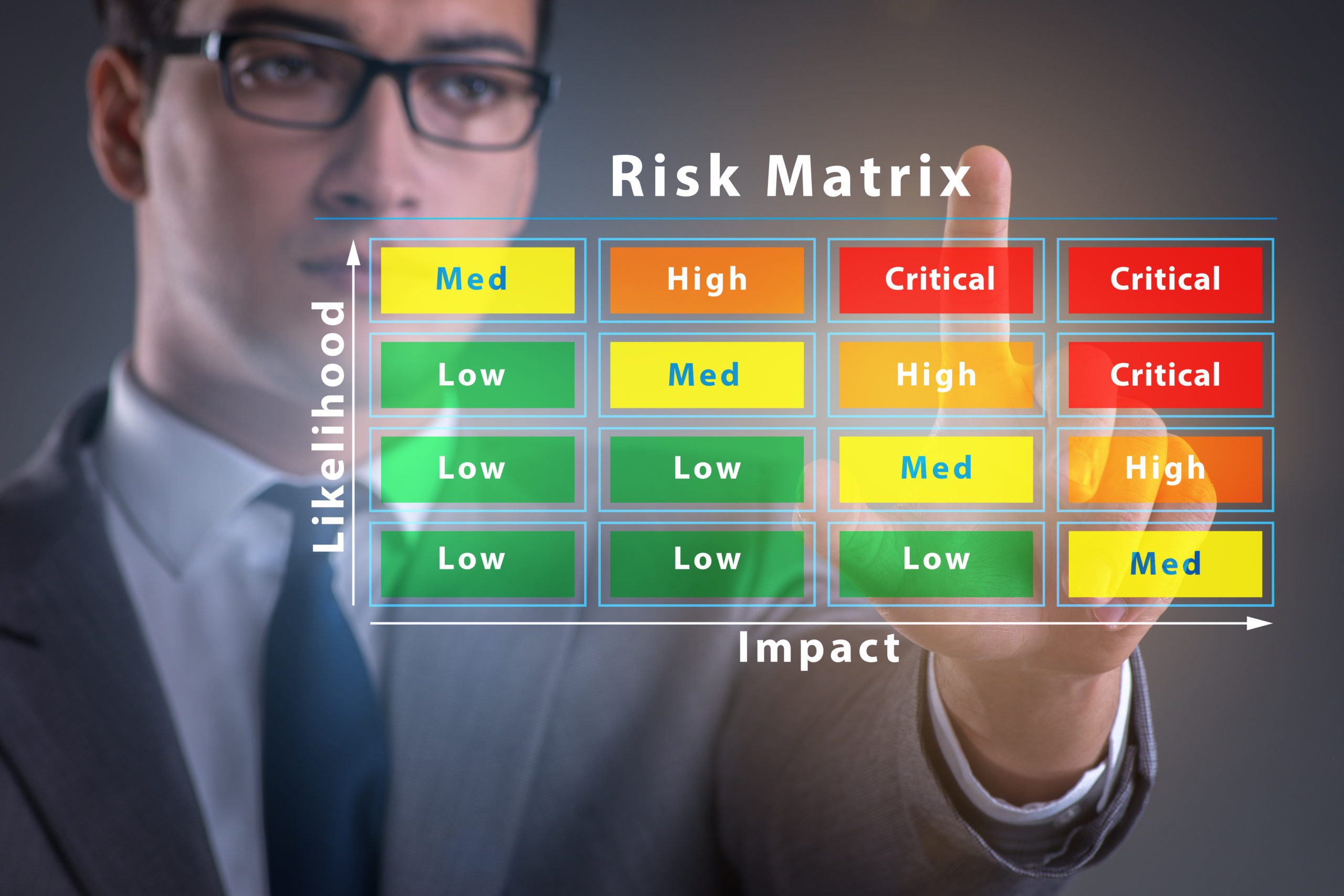
Technology is steadily evolving, forcing businesses to think about adapting quicker to suit the needs of ever-demanding customers.
It is common that many companies, particularly small businesses, avoid addressing their technology problems due to uncertainty and the time it takes to solve the issues. This article will give you three potential solutions and help you overcome technology challenges while saving time and money in the process.
I can think of numerous examples from my days at Rid-Lom Precision, where our goal was to improve the manufacturing process every day. I had many areas that I thought I could improve if I just spent the time and money, but it wasn’t until I heard about NASA’s $167 million space pen that I realized many of the improvements might already be within my reach.
In case you don’t know the NASA space pen myth, NASA supposedly spent $167 million doing the space race with the Russians to create a pen that will write in a non-gravity environment. The Russians used a pencil.
Now, I have already stated that this is a myth, but the point is clear: are there tools within your reach that can help you be better today?
With Inventor at the center of product design and manufacturing, there are many opportunities to adopt new technologies. Here are three challenges that can be solved and put you one step closer to eliminating the technology barrier.
Challenge #1: Choosing technology according to the company’s needs can be challenging, and investing in new technology can seem like a daunting and overwhelming task. Automation has been a hot topic in the industry for years, but there is a fear of choosing tools that will lead the business in the wrong direction. However, to stay competitive, companies must be willing to make changes; we all understand that. Choosing the right technology for your business means choosing a system that not only delivers the capacity you need today but can also meet tomorrow’s expansion needs.
How to overcome: If you are already utilizing Inventor in your design process, you might already take the automation process of updating a dimension on a part, which also updates the drawing as a simple automation process. A natural next step would be to look into using iLogic and add more automation to your designs. iLogic has enabled many companies to leap into the next level of automation. However, don’t let your advancement stop with iLogic; using the Forge platform, you can integrate Inventor and iLogic workflows into the Forge’s web service APIs, allowing you to implement Inventor components in new web and mobile applications.
Take a look at how American Drainage Systems utilizes Inventor and Forge in ways most designers and engineers can only dream off here
Challenge #2: Integrating applications: Another challenge that businesses often face involves integrating applications. Often, newer technologies do not integrate well with other systems or legacy applications. Two areas where improvements are often sought in manufacturing are precision and communication. Your business needs to ensure existing systems will integrate with any new technologies you want to leverage.
How to overcome the challenge: With The Product Design and Manufacturing collection, you have access to Model-Based Definition and Tolerance Stack-up Analysis. You can use Model-Based Definition to communicate important data and tolerances beyond your 2D drawings. This can bring critical dimensions to the forefront and avoid mistakes. Tolerance Analysis can eliminate Excel spreadsheets and, worse, costly over-engineered parts by visually and mathematically ensuring all the components fit together at the assembly station. These two applications, Model-Based Definition and Tolerance Analysis are available in your design package to ensure you extract as much information from your 3D models and push for higher precision parts.
Learn more about Tolerance Analysis Stack-up here
Challenge #3: Securing the design data: According to an undisclosed study floating around the engineering community, engineers and designers are spending 35% of their time searching for or recreating 3D models. One single part produced from the wrong revision can cost thousands of dollars. It is time to manage your CAD data; if you are not doing so already, the risk of errors is not just around the corner, it is breathing down your neck.
How to overcome: At Autodesk, we understand that time is your most precious asset, and the time spent in your design tool adds up to a significant amount. With Vault, you can stay organized, ensure that the hours spent creating 3D models are secure and saves your business from costly mistakes. We stress the importance of taking the necessary steps to secure your data and ensure that the shop floor is always working to the right revision. It is important to remember that anything that relies on teams to be organized and aware of what everyone else is working on will fail from time to time. We are aware of the risks and make it easier for you to protect yourself from losing money.
Learn more about data security with Vault here
Written by:
Lars Christensen
Technical EvangelistLars Christensen is an award-winning Design & Manufacturing Expert who helps people that haaa-ate struggling with their CAD&CAM Software. Through his totally-addictive blog posts and videos on his YouTube channel, he shares his experience so people can create and make their product in greater happiness. He has shared his know-how around the country, featured in manufacturing magazines as well as influential online engineering sites. And when he is not teaching and sharing in the design and manufacturing space, you can find him with his nose in the latest business/development book and is occasionally spotted indulging in scoops of ice-cream. Explore his YouTube channel to get the power to add “chop-chop” to your next design and manufacturing project.