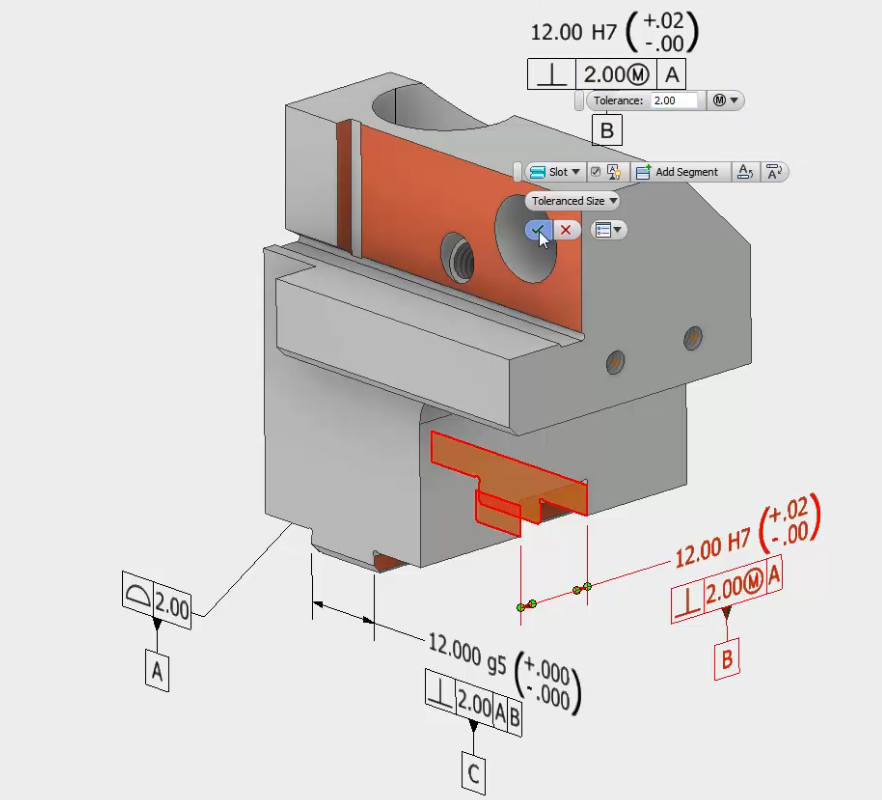
Part 1: The Problem We’re Trying to Solve
For decades, the manufacturing industry has relied on 2D drawings, and struggled with interpretation and communication issues that go along with it. Although they’re deep-rooted in most companies, 2D drawings-based processes require human interpretation and are hence error-prone. Also, they do not lend themselves well for paradigms in Industry 4.0.
Fig 1: Is there an elephant in the room? Are manufacturing engineers interpreting the data on 2D drawings correctly?
There has been a significant amount of buzz lately around Model Based Definition (MBD), oftentimes associated with discussions regarding paperless and/or drawingless initiatives. There has also been an equal amount of skepticism. The primary argument against it being that the concept of MBD, also referred to in the past as 3D Annotations (3DA) and PMI (Product Manufacturing Information), has been around for years and has failed to gain substantial traction. While there’s a counter-argument that the aerospace and automotive segments have in fact realized dramatic benefits from MBD, leading other segments to take a serious look at this philosophy, we’ll focus instead on what’s changed recently to rekindle MBD efforts.
Firstly, there’s a growing realization that the real benefits of MBD are in enabling and digitizing downstream processes (like automatic toolpath & inspection path generation, tolerance analysis, etc.) rather than in incremental improvement of documentation processes. MBD does indeed have the side-benefit of improving 2D drawing creation productivity, but it should be thought of as just that: a side-benefit. The goal should be to maximize the usage of 3D models in order to improve design quality and drive better design-to-manufacturing efficiency.
Fig 2: Focus on enabling downstream apps while recognizing that derivative outputs are important for documentation and archival
Next, there has been a steady decline in the availability of 2D drafting skills and expertise. It’s rare to find traditional drafting courses in universities and companies are eliminating traditional drafting jobs. However, the need to properly dimension and tolerance models still exists. Appropriate use of Geometric Dimensions and Tolerances (GD&T) not only ensures higher quality and better fit of products, but also results in cost savings by preventing tolerances tighter than required. The logical progression is for designers to embed such information in the model during the design process and for manufacturing software to directly interpret this information.
Finally, the STEP AP242 standard is now established and maturing quickly. This provides a great baseline for exchanging model data, with MBD, across CAD, CAM, CMM and other applications. Deeper integrations between design and manufacturing are possible by connecting directly to native CAD models using the application’s APIs. Ultimately, it means that a machinist or a manufacturing engineer doesn’t have to manually translate all the 2D PMI into a CAM or CMM setup. Some or all of that information can be re-used, reducing the potential for error and saving the manufacturing expert considerable time.
Following are a couple of quotes from Autodesk customers that nicely sum up their needs with regards to these…
|
|
If you fast forward 10 years, it’s hard to imagine that 2D drawings will still be interpreted by a human on a shop floor, that information will be manually entered for generating toolpaths or inspection paths, or that assembly stack-up analyses will be done manually or using spreadsheets. With the quick onset of automation in various fields and industries, it is imperative for manufacturers to evaluate the changes needed in their processes and culture, to digitize their processes.
In the next part of this article, we’ll look at how Autodesk Inventor enables manufacturers to move towards a model-based enterprise and set up for digitization.
Sanjay Ramaswamy, Product Manager, Inventor Product Line