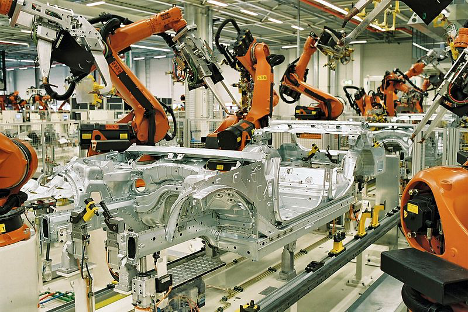
The future is bright. Robotics, the Internet of Things, augmented reality, and 3D printing, these are all directions where the manufacturing industry is headed.
For much of manufacturing’s history, it has been a hands-on trade-oriented skill that took years to master. With the advent of computer design, all of that changed. We are now well into the life of computer-aided design in manufacturing, and it continues to shape the direction our industry is headed. Outside of sheer software developments, the industry is gaining top-of-the-line robotics systems in an increasingly connected manufacturing process. These advances only make the job of the manufacturing engineer easier. In some sense, the manufacturing engineer has the ability to play god in part production, knowing virtually every aspect of the process in real-time. Let’s look at some emerging innovations that will direct the manufacturing industry for years to come.
Robots. The machines that one day may terminate us are currently helping us produce parts better than ever. China has become the biggest producer of manufacturing robots in the last decade, with estimates of them producing 150,000 machines in 2017. The days of completely robotic factories, while still here, seem to be fading. In more developed manufacturing economies like the US, companies see fully automating the manufacturing process as hindering innovation. The thought is that if we replace all of our workers with robots, there will be no one to think of innovative ideas. This is a viable and sustainable thought process, which has moved the robotic manufacturing industry into more of a complementary role. Companies are now seeking to implement robotics to complement factory workers, thus improving efficiency while retaining an essential workforce. This spells good things for the manufacturing job market and means that robotic innovation is nothing to fear.
Virtual reality. If you think you’ll be designing parts in virtual reality in the future, well, you’d be right. 3D printing created the idea of rapid prototyping, but VR may eliminate the need for physical prototyping altogether. Physical prototyping will always have its place, but why spend money on materials when you can simply step into a virtual world and experience parts or machines in a perspective never before possible. While not widespread, there are many cutting edge CAD designers that use VR headsets and technologies to design parts. Companies like Samsung and Boeing are already using VR to train technicians and workers. The daily life of a manufacturing engineer may soon involve less time in the real world and more in a virtual design space, and that’s pretty awesome.
Connectivity. In a less broad sense, this is now known as the Internet of Things or IoT. This is an overarching concept of connecting all objects of life through networks and signals. From connecting automobiles to stoplights or even couches to televisions, soon every aspect of our lives will be connected. While the IoT is an overarching concept in many industries, within manufacturing it poses a significant advantage. Connecting every aspect of a manufacturing plant enables operators to see and manage all of the complexities of operation from one single hub. It means knowing exact temperature data on the material at specific points in the production process. It means understanding the stresses imposed on a component in real-time. It means everything to manufacture plant automation.
By bringing these cutting edge aspects of the manufacturing industries together, we will soon see connected virtual plants that can produce any part on demand. It’s a manufacturer’s dream and a maker’s nirvana. Hold onto your seats manufacturing engineers, because we’re headed for ultimate optimization.
Sources: Strategyand, Design News, Ennomotive, Automation World