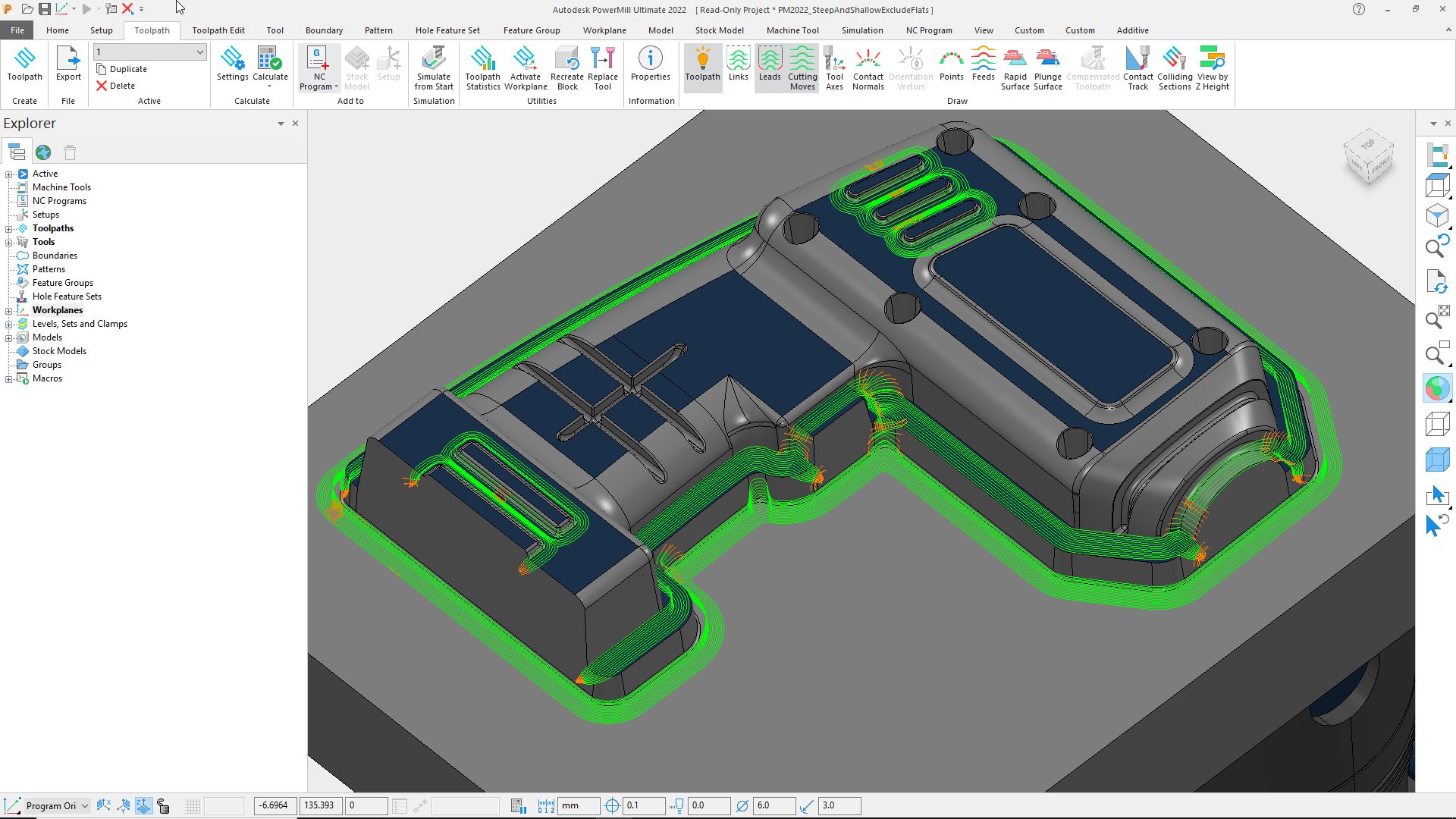
With Christmas on the way (and thanksgiving even closer), we’re pleased to announce the release of the latest update to Autodesk’s CAM software Fusion 360 with PowerMill (version 2022.1). This release includes a bumper collection of speed-ups, usability improvements, and a sneak preview of a really nice new toolpath coming in the near future.
PowerMill 2022.1 – Customer Release: November 8, 2021
In this blog, we’ll provide a brief overview of the top 6 highlights in this specific release. We’ll also provide links to more detailed tutorial videos (for those of you wanting to see the improvements in action).
1. Background NC program and toolpath verification
Verification! Arguably one of the most important things you can do if you’re outputting NC code to drive a CNC machine. Regardless of the cost of your CNC machine (whether it be an entry-level 3-axis router or a top-of-the-range, 5-axis wonder), it’s essential you can validate the safety of your machining process before going anywhere near your actual machine to find and avoid machine collisions, near-misses, and axis over-travel.
PowerMill has provided the ability to check toolpaths and NC programs for these common issues for a number of years. Crucially (with previous releases) the verification itself was carried out using what’s called the “foreground processor”. In simple terms, this means that the verification consumes 100% of your computer resources – stopping you from doing anything else. This latest release of PowerMill (2022.1) changes this and includes an option to “queue” the verification so that it uses the “background processor”. How does this change things? Well, the answer is big time! The background processor doesn’t consume 100% of your resources, meaning you cancontinue with other CAM programming tasks while the verification is being processed behind the scenes.
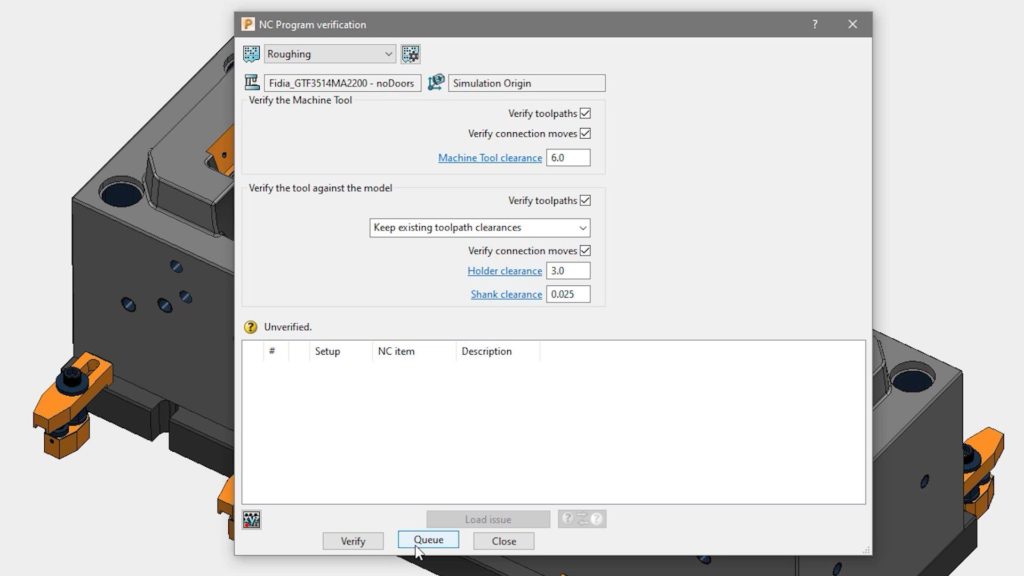
Background verification allows you to shorten your overall CAM programming time, but there’s something more subtle going on here. By making verification more accessible, we also believe this reduces the temptation to bypass verification completely (something that might sound like a risk worth taking until you experience a collision for yourself).
To learn more about this specific improvement, watch this handy tutorial
2. Projection ranges now available for Line, Plane, and Point toolpath types
In the previous update (see blog post for PowerMill 2022.0), we introduced manual Projection Ranges that could be used to control the extents of both Curve Projection and Surface Projection toolpaths. Without the range control options, it was commonplace for toolpaths to be created that would machine neighboring surface geometry (as can be seen in the image below).
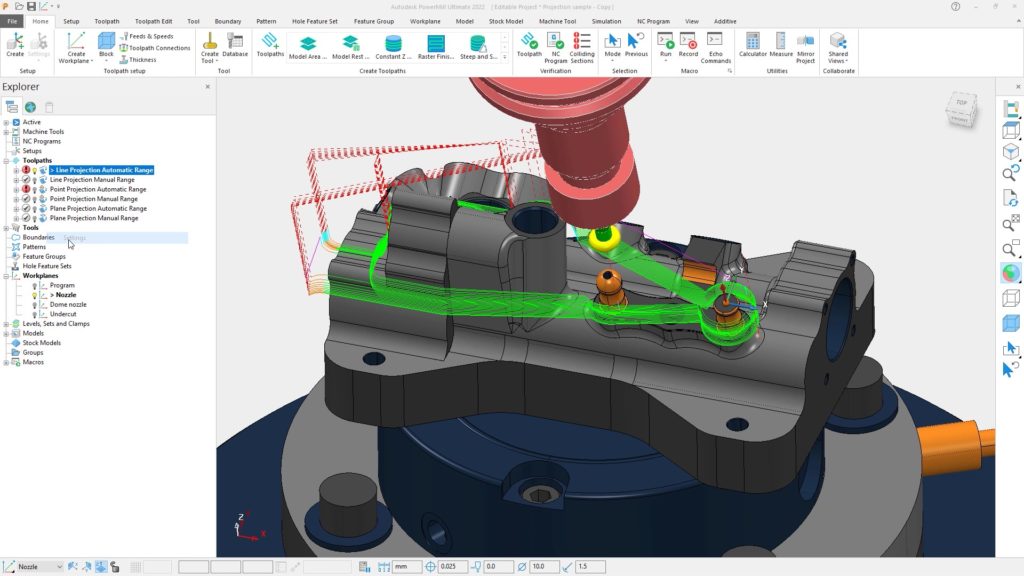
This latest release of PowerMill extends the projection range options so that they can be applied to Line, Plane, and Point Projection toolpath types. This increases the likelihood that toolpaths will be created right-first-time, and reduces the need for additional toolpath editing to remove excess toolpath segments. In this example, we can see how projection ranges help limit this Line Projection toolpath to machine the cylindrical upstand on an automotive part.
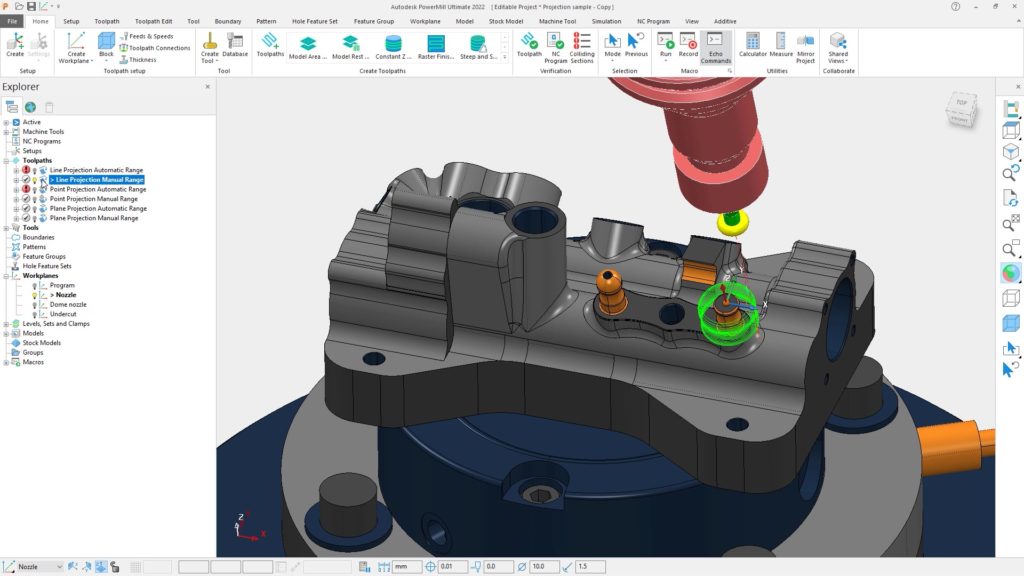
To learn more about this specific improvement, watch this handy tutorial
3. (Much) faster toolpath settings form
The toolpath settings form is arguably one of the most commonly-used parts of the PowerMill interface. It is used to setup toolpath parameters, as well as calculate and re-calculate toolpaths. Over the years, this form has grown in terms of its capability (more options, extra toolpath types, explanatory images, and hyperlinks to learning content). While these additions are incredibly useful, they also meant the form became a little sluggish to open, something that was becoming increasingly frustrating for many of our customers.
As a direct response to this, the PowerMill development team has worked to speed up the form so that it is much faster to load. In fact, in our tests (using a fairly standard workstation laptop) we’ve seen the form loading between 47% and 65% faster than previous releases.
The chart below shows a comparison of form load times for four different toolpath types.
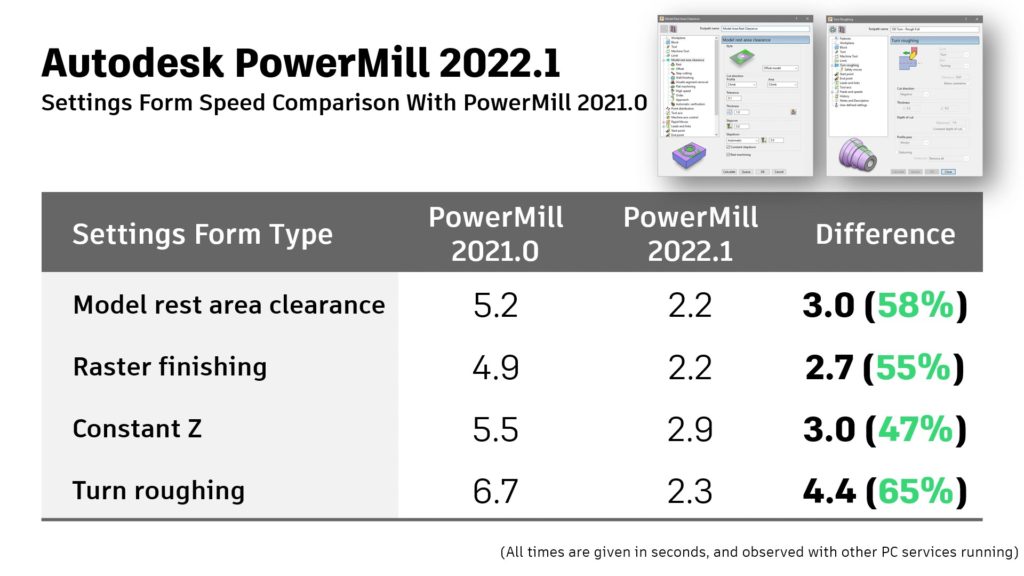
During BETA testing, a number of customers actually saw even bigger time savings here. In fact, one large automotive mold manufacturer carried out independent testing and found that the form was 90% faster in this release than the previous version. Their tests involved opening a very large (5.7Gb) PowerMill project and accessing the toolpath settings form. In previous releases, the form typically took 12 seconds to open, whereas PowerMill 2022.1 took less than 1 second.
While these savings certainly sound impressive, it’s the accumulative impact over time that is most beneficial. As an example, if a CAM programmer accesses the form 100 times, they’ll be saving more than 18 minutes of time.
To learn more about other Quality of Life improvements, watch this overview video
4. Faster model preparation (for faster toolpath calculation & editing)
Still on the subject of speed, this latest release of PowerMill includes some pretty neat improvements that will impact a number of toolpath related processes. “Model Preparation” is an integral part of many processes including; toolpath calculation, toolpath editing, and modifying leads and links. During a routine algorithm review, the PowerMill development team identified that the model preparation part of the code could be made more efficient.
What does this mean for you?
Now, while we could go into details as to what model preparation means, it’s probably simpler to say that these improvements should result in faster toolpath calculation and editing times. In our tests, we saw the greatest savings occurred when editing toolpaths that machined large parts, or where toolpaths were calculated using very small tolerances.
Take this large press tool die as an example. Measuring 2000mm by 1300mm by 560mm in size, we’ve produced a corner multi-pencil finishing toolpath using a tolerance of 0.001mm.
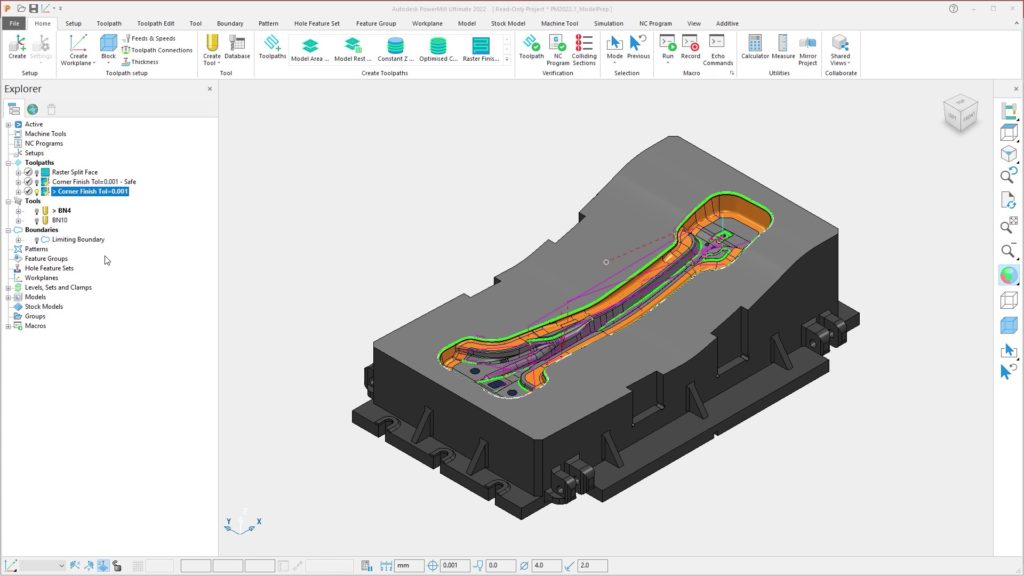
For various reasons, we need to limit this toolpath to extract a small area to machine. We do this by limiting the toolpath using a sketched polygon (something that’s been in PowerMill for many years).
When we compare the total time taken to complete the toolpath edit using PowerMill 2021.0 and 2022.1 we can see a small, but significant time saving of 16%. However, during BETA testing, another customer reported even bigger time savings. In their tests, the time taken to edit a toolpath reduced from 48 seconds to 18 seconds – a saving of 62.5%. Remember, as mentioned earlier, the time savings you’ll experience will vary based on a number of variables, including your computer specification and the size of your PowerMill projects.
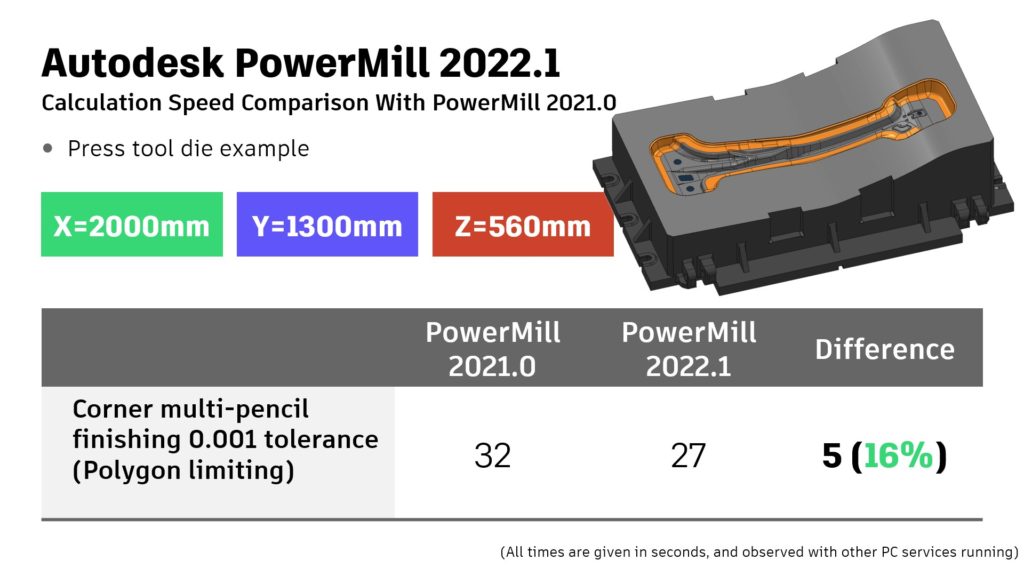
To learn more about this specific improvement, watch this handy tutorial
5. Improved toolpath limiting user experience
It’s often the little things that have the biggest impact on life. That’s certainly true when it comes to toolpath limiting in PowerMill which is arguably the most commonly used toolpath edit (based on usage metrics). The ability to limit a toolpath whilst avoiding unnecessary re-calculations has been one of PowerMill’s unique selling points for a long time. The release of PowerMill 2022.1 builds on this by including a couple of small improvements to user experience.
The introduction of a “rubber band preview” during polygon sketching helps visualize the regions of toolpath that will be removed or preserved, which reduces the likelihood of an incomplete sketch being defined.
At the same time, a new “Restore View” button helps reinstate the 3D view that was used to initially define the sketched polygon. This last command is particularly useful in cases where you’ve spent time sketching a polygon and then accidentally rotated the view, meaning the sketch becomes misaligned with the view. Clicking on this button simply resets the view and allows you to continue sketching the polygon instead of having to stop and restart the entire command.
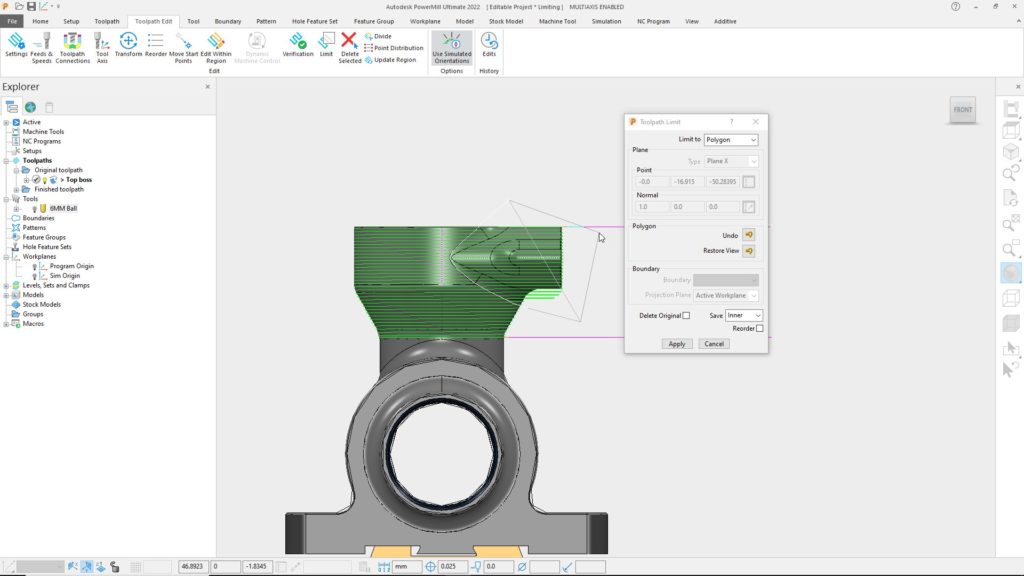
To learn more about this specific improvement, watch this handy tutorial
6. Improved macro security
If you routinely use PowerMill macros, you probably already appreciate just how powerful they are and the impact they can have on your productivity through automation. While macros certainly provide all this (and more) they also represent a potential security risk as they can provide a means of interacting with, and potentially damaging, data on your local hard-drive or extended network.
It is for this reason that the PowerMill development team has introduced additional security checks that are run every time a macro is started. These checks ignore all of the standard PowerMill commands (e.g. creating a block, producing a toolpath, verifying NC programs) but will be triggered if a macro contains one of a number of pre-defined commands that interact with data outside of the PowerMill interface.
If a suspicious macro command is identified, PowerMill will display a message with three options:
- “Trust” – the macro is deemed safe and is allowed to run. It is also added to a folder of “safe” macros for future use
- “Don’t Trust” – the macro is stopped from running.
- “Inspect” – the macro is opened in a text editor for closer inspection.
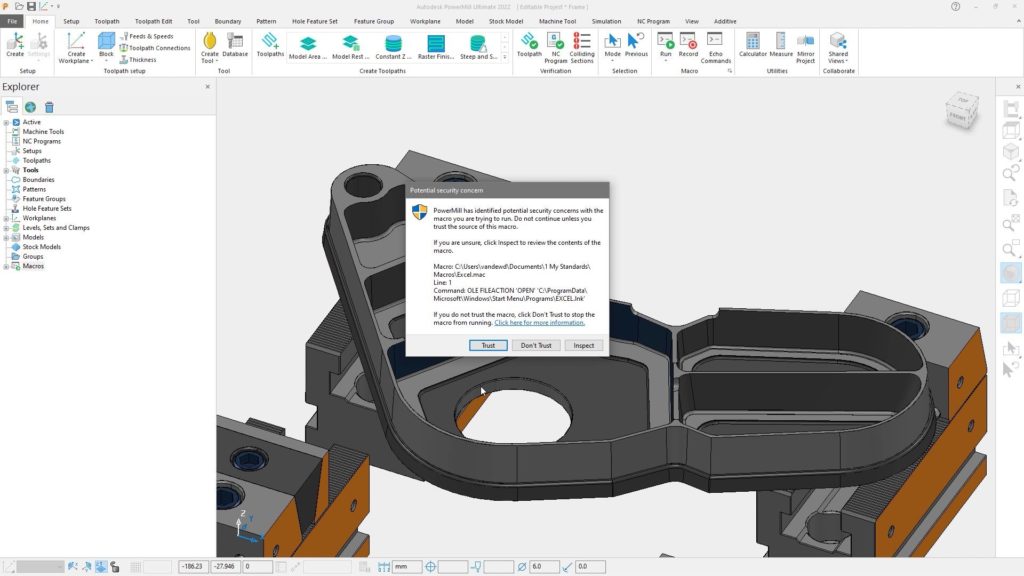
Example commands that can trigger this behavior include:
- TRACEFILE OPEN “<path_string>”[this creates a file on your hard-drive or network then populates it with all commands and error messages that occur in PowerMil until the file is closed]
- MKDIR “<path_string>”[this creates a folder on your hard-drive or network]
- FILE OPEN “<path_string>” FOR APPEND AS <var>[this opens an existing file and appends additional text into it]
- TOUCH “<path_string>”[this updates the last modified information for the named file]
- STRING $Y = ‘OLE FILEACTION “open” “<path_string>”’ DO COMMAND $Y[this runs a 3rd party product, such as Excel, and then sends commands to that product]
Macros can be “trusted” individually each time they are run. Alternatively, it is possible to add pre-defined folders to a “safe” list inside PowerMill allowing multiple macros to be trusted in one go. Crucially these settings are remembered across PowerMill sessions, for improved security.
To learn more about this specific improvement, watch this handy tutorial
7. New rest finishing toolpath (preview)
OK, so we said top 6 reasons but (like all good Marvel films) we thought we’d include a little bonus – and what a bonus it is.
For many years, PowerMill has provided different ways to identify and remove rest-material (i.e. the stock left un-machined by large cutters or rough machining). Tools and strategies like Pencil Finishing, Corner Finishing, and Rest Boundaries all have definite strengths but they also have their weaknesses. It’s for this reason that we’ve developed a completely NEW toolpath called “Rest Finishing” (yes, we know, it’s not the most imaginative name).
The new “Rest Finishing” strategy aims to combine the accuracy of rest-boundaries (these are great at identifying un-machined stock) with the flow of pencil finishing (these result in smooth machine motion), and the safety of corner finishing (the ability to machine steep and shallow corners in different ways) into a strategy that can remove rest material safely, accurately, and efficiently.
We can see an example of this command in action on this power drill mold core. Pay attention to the extent of machining, and the way the toolpath flows around the part.
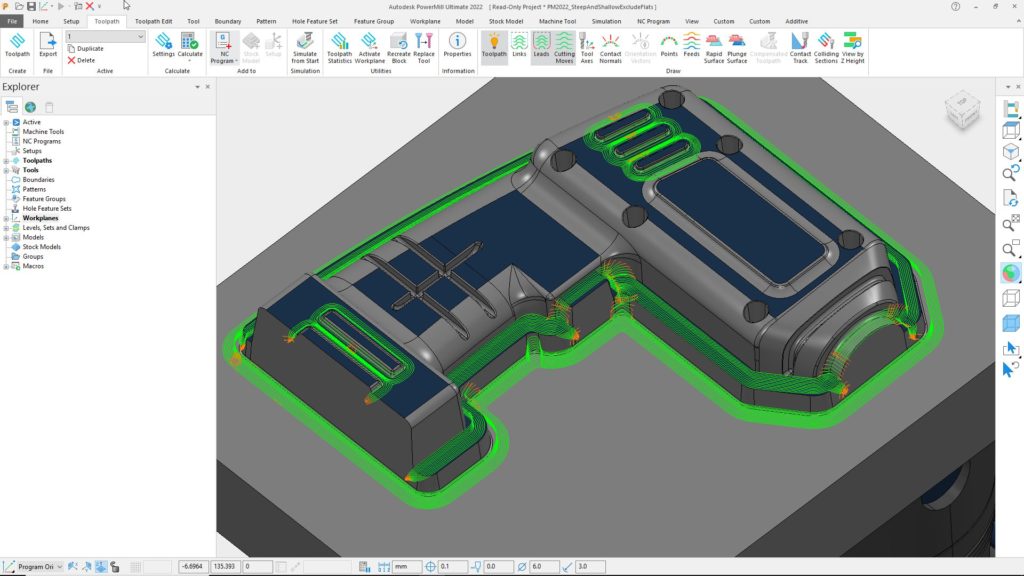
IMPORTANT – PREVIEW: The new Rest Finishing strategy has been available in BETA for a number of weeks. Initial results are very impressive but we’re not quite ready to classify this as being a FULL CUSTOMER RELEASE. As such, this new strategy is released UNDER PREVIEW. We encourage you to try this command on your own data and use the PowerMill user forum to provide feedback to the development team. We aim to update this to a FULL CUSTOMER RELEASE in the near future.
Want to learn more?
So that’s it. The top 6 (OK 7) improvements in Fusion 360 with PowerMill (version 2022.1). There are more improvements, and you can read about them all in the official release notes at https://help.autodesk.com/view/PWRM/2022/ENU/
If you want to take a deeper dive into this release, why not watch this 36min release highlights.
Ready to download this latest version (2022.1)?
Existing customers.
Fusion 360 with PowerMill 2022.1 will be released to customers starting November 8, 2021.
Eligible customers with an active subscription or maintenance agreement will be able to download the latest release starting November 8, 2021. Customers can download using the Autodesk Desktop App or by logging into their Autodesk Account. Alternatively, visit our Services Marketplace to contact your local Autodesk team and discuss your specific business needs.
New to Fusion 360 with PowerMill? Why not try a free evaluation.
New to PowerMill and want to see how it can help you solve your toughest CNC machining challenges? Contact our team of manufacturing specialists at www.autodesk.com/powermill-evaluation to learn more. Submit your contact details and our team will contact you to discuss how Autodesk can help your business to be more successful.