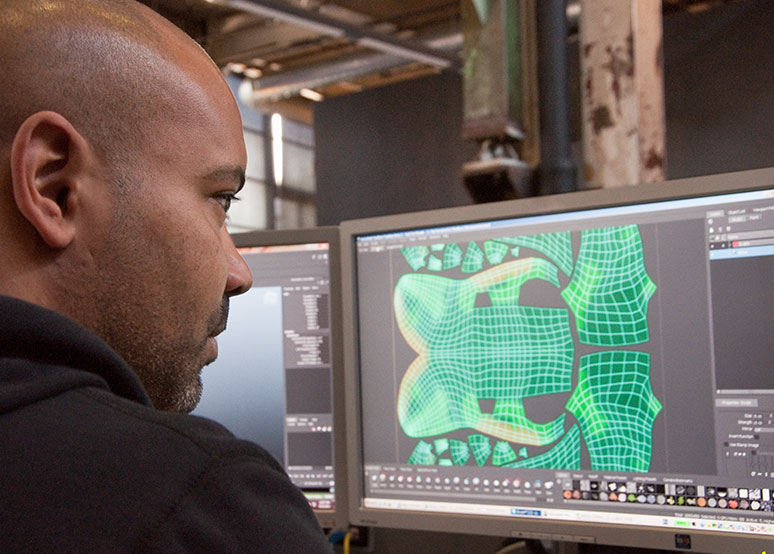
Computer aided design changed the engineering realm just a few decades ago. The latest change to the tools available to engineers is the full integration of computer aided manufacturing (CAM) into CAD programs. Let’s take a look at the biggest benefits that a CAD/CAM integrated workspace brings us as engineers.
One thing that CAD did when it first was implemented was shorten the transfer time between departments on projects. Even with this shortened process, there were still communication barriers between the design engineering and manufacturing departments, as many of you likely know. Bringing CAM into the CAD space allows an ease of knowledge sharing between departments so that the initial design can be seamlessly integrated into the designated manufacturing process. Having CAM internal to CAD keeps the design engineer honest and practical in the design phase and it helps out the manufacturing engineer when it comes time to make the product. Some CAD/CAM systems have the ability to store features in a common library, which allows for custom features later down the line. This allows CNC programmers and manufacturing engineers to work with designers to include specifications that take into account the manufacturability of a product. All in all, CAD/CAM has drastically improved our ability as engineers to consider every step of the design-make-use process.
Time. Any engineer that uses integrated CAD/CAM on a regular basis understands how much time it saves. Having both features integrated into one software eliminates a majority of costly data translation steps up front. On the back end, if a change in the component needs to be made due to manufacturing problems, this can easily be changed on the CAD side while automatically updating the CAM. This functionality has made our lives exponentially easier and it saves companies hundreds to thousands of man hours on a grand scale.
Having manufacturing software integrated into CAM allows us to automate much of our CNC and numerically controlled programming using basic design requirements developed in the CAD model. Not only this, but the NC data for a part’s manufacturability can be stored directly within the 3D model to allow constant updating, as I mentioned previously. This functionality makes sure that when a design is altered, it doesn’t become non-manufacturable. Any engineer who has been involved in the product redesign process likely understands how helpful it is to instantly understand manufacturability concerns when a design is updated.
These three changes – time savings, automated CAM, the breakdown of communication barriers – are the biggest changes brought to the modern engineer through integrated CAD/CAM. With that said, if you are an engineer who uses integrated CAD/CAM, you likely have other changes that this capability has brought to your design process. As the software continues to get better and cross-platform integration continues to grow, we will likely start seeing even greater functionality improvements in the workflow tools for engineers.